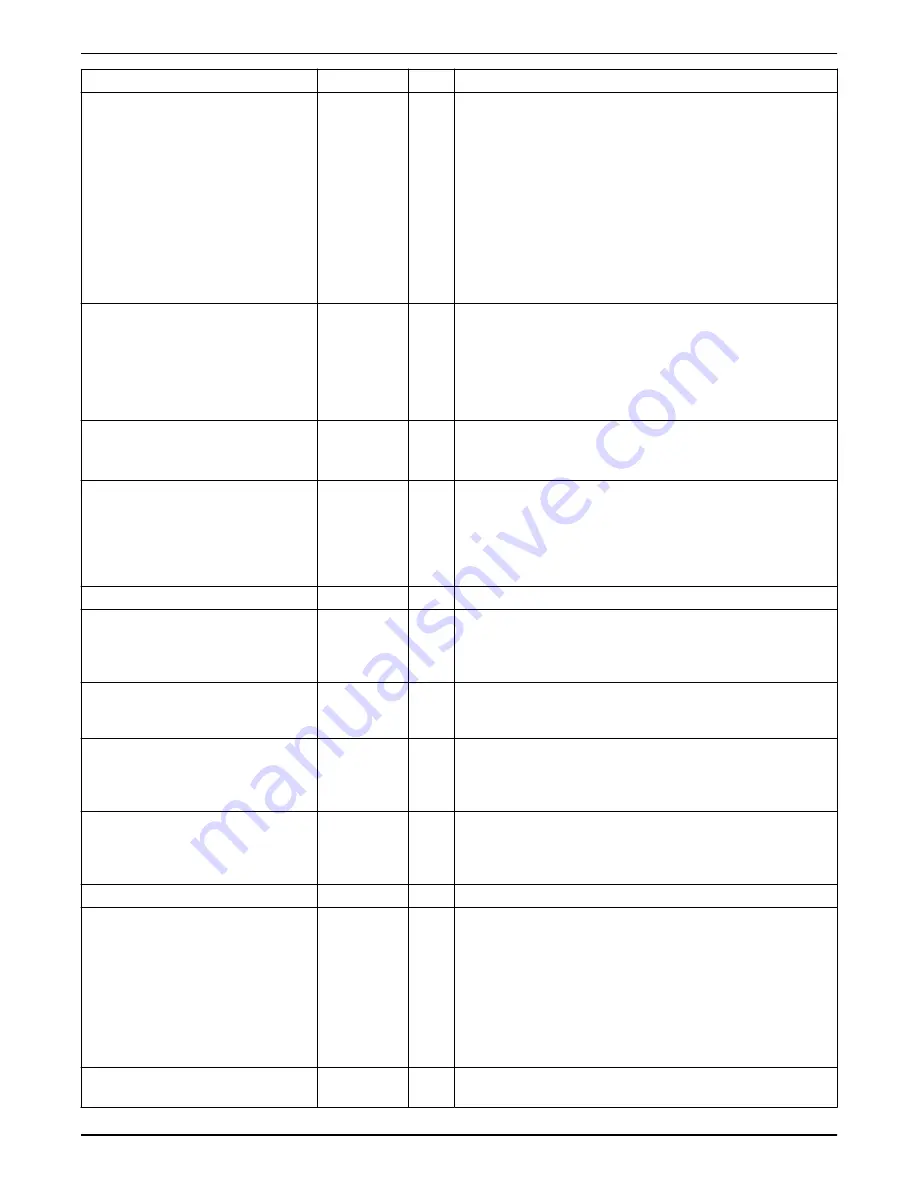
Parameter name
Default value
Level
Description
P2-13:Analog output 2 function
0: Drive
running
2
• 0: Drive running
• 1: Drive healthy
• 2: At target speed
• 3: Motor speed > 0
• 4: Speed >= limit
• 5: Current >= limit
• 6: Reserved
• 7: An-input2>=limit
• 8: Speed
• 9: Current
• 10: Reserved
P2-14:Analog output 2 format
0: 0-10V
2
• 0: 0-10V
• 1: 10-0V
• 2: 0-20mA
• 3: 20-0mA
• 4: 4-20mA
• 5: 20-4mA
P2-24:Switching frequency
Varies
2
Configures the effective power stage switching frequency. Default value
depends on drive size.
For more information, see
P2-35:Analog input 2 offset
0.0%
2
Defines an offset for the analog level sensor input on terminal 10, as a
percentage of the full range of the input. A positive offset is deducted
from the incoming analog signal and a negative offset is added to the
signal. A value of +0.3% is a recommended setting for the drives that
do not have the level sensor directly connected. This offset compensates
for the level offset added to from terminal 10 to terminal 8.
P2-39:Parameter lock
0: unlocked
2
Configures the lock of the parameters so that they cannot be changed.
P4-01:Motor control mode select
0: AC motor
vector IM speed
control
2
Configures the motor control mode for different types of motors. If the
motor is asynchronous or a synchronous permanent motor (LSPM) that
can also start and run without the frequency inverter, then set
parameter to 0.
P4-02:Auto-tune enable
0: disable
2
Configures the auto-tune process. To start the process, set the
parameter to 1, auto tune. This setting improves the motor
performance.
P4-13:Pump cycle time
30 min
2
Configures the time that is allowed to pass in auto-running mode
before the pump frequency is increased from energy frequency to max
frequency by 1 Hz/min to empty the sump and end the current pump
cycle.
P4-14:Max freq start run time
5 s
2
The amount of time that the pump runs at maximum frequency at each
pump cycle start. This function is used to tune the operation of pumps
equipped with a flush valve or to force sediments in pipes into
suspension.
P4-15:High lvl sensor run time
10 s
2
The run time after the high-level switch has been toggled.
P4-16:Sump cleaning time out
4
2
Displays the time-out factor of the snoring detection function which
determines what the calculated snoring time is scaled with.
The calculated snoring timeout is adaptive and calculates the expected
time that is required to pump the level from the stop level to the
snoring level. The calculation is based on the level lowering rate as
measured when pumping from start level to stop level. The function
assumes that the analog zero level is equal to the snoring level. Setting
the parameter to 1 corresponds to a timeout equal to the dynamically
calculated period.
P4-17:Number of pump cleanings
0
2
Displays the number of hard clog pump cleanings. Reset the counter by
writing zero to the parameter.
Technical Reference
54
SRC 311 - SmartRun
™
Installation, Operation, and Maintenance Manual