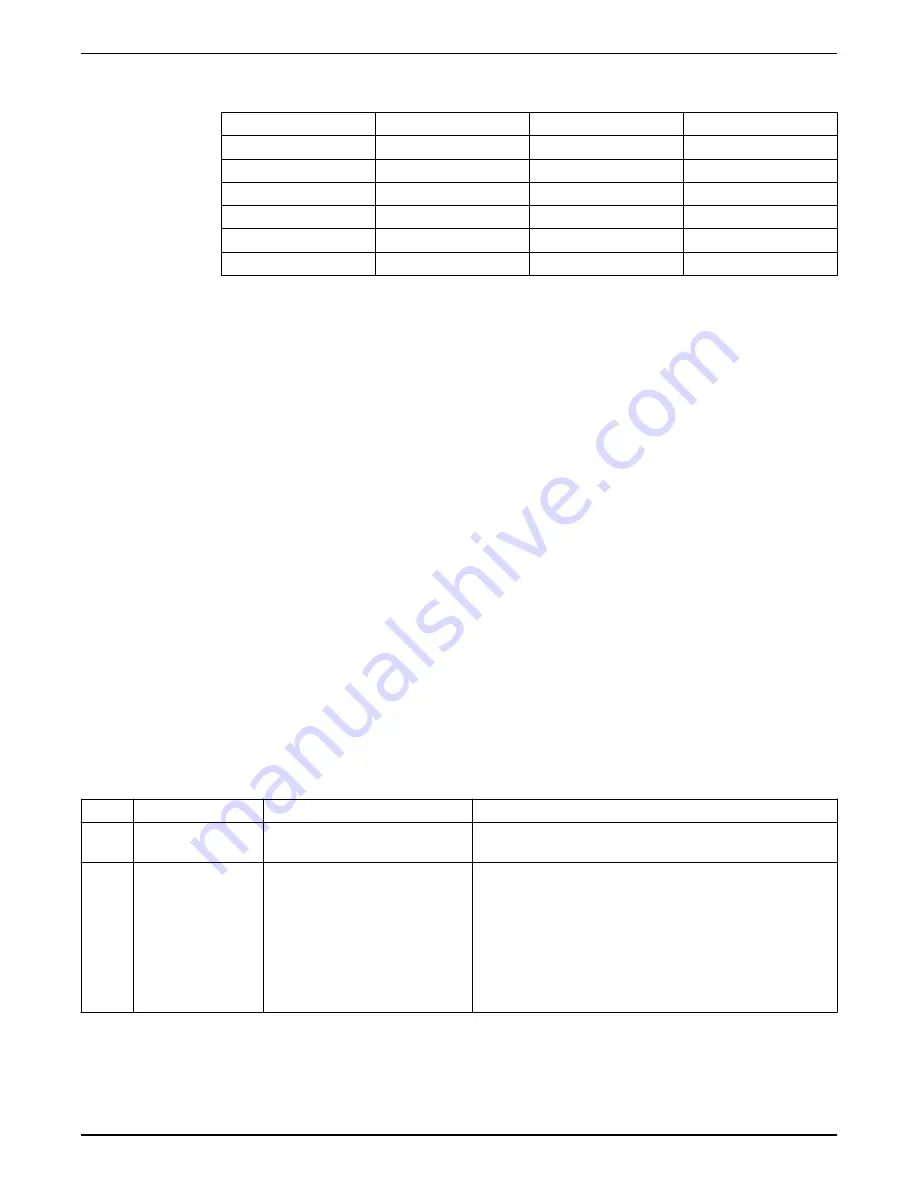
sensor error and high level are active, the alarm code is sensor error alarm (8) + High-level
alarm (4) + alarm active (16) = 28. If the alarm is reset, then the alarm code is reset to 0.
Alarm display text
Display text
P1-19:Alarm state
P0-50:Alarm log
Pump leakage
Pump leakage
1
1
Pump over temperature
High pump temperature
2
2
High level, digital
High sump level
4
3
Sensor error
Level sensor error
8
4
High level, analog
High sump level
4
5
Alarm active
-
16
-
Alarm communication
Pump and process alarms that are communicated externally using the fieldbus, Modbus
RTU, and relays 1–4. The communication requires the P6-19:Relay output 1,P6-20:Relay
output 2, and P6-21:Relay output 3 and 4 parameters are set to communicate alarms.
For details regarding alarm codes, registers and terminals, see
(page
57). When a process alarm from the pump or the sump is triggered, the relevant register
contains the Modbus alarm code and the sum alarm on the relevant relay terminal.
Reset active alarm
The name of the tripped alarm is displayed in the display and an alarm code is visible in
the P1-19:Alarm state parameter. The contact on the sum-alarm relay that is set to
communicate alarms is open.
The alarms are reset by one of the following steps.
• Reset the alarm manually:
a) Press the Off button when in auto mode to reset the alarm.
b) Press the On button to enable the drive.
• Reset the alarm using Modbus RTU:
a) Write 3456 to the P1-19:Alarm state register
• Reset the alarm with a digital signal:
a) Send a digital input signal (8-30V DC) to terminal 3.
Fault codes
The fault codes are displayed when there is a trip. A log of the last four trips is stored in
the parameter P0-13:Trip log.
No.
Display message
Description of display messages
Corrective action
0
no-Flt
No fault
Displayed in P0-13 if no faults are recorded in the log.P0-13:Trip
log.
3
O-l
Instantaneous over current on drive
output
Fault occurs on drive enable.
• Check the motor and motor connection cable for short circuits.
• Check the load mechanically for a jam, blockage, or stalled
condition.
• Ensure that the motor data plate parameters are correctly
entered in the parameters P1-07:Motor rated voltage,
P1-09:Motor rated frequency
• Increase the ramp up time in P1-03:Acceleration ramp time
Troubleshooting
SRC 311 - SmartRun
™
Installation, Operation, and Maintenance Manual
47