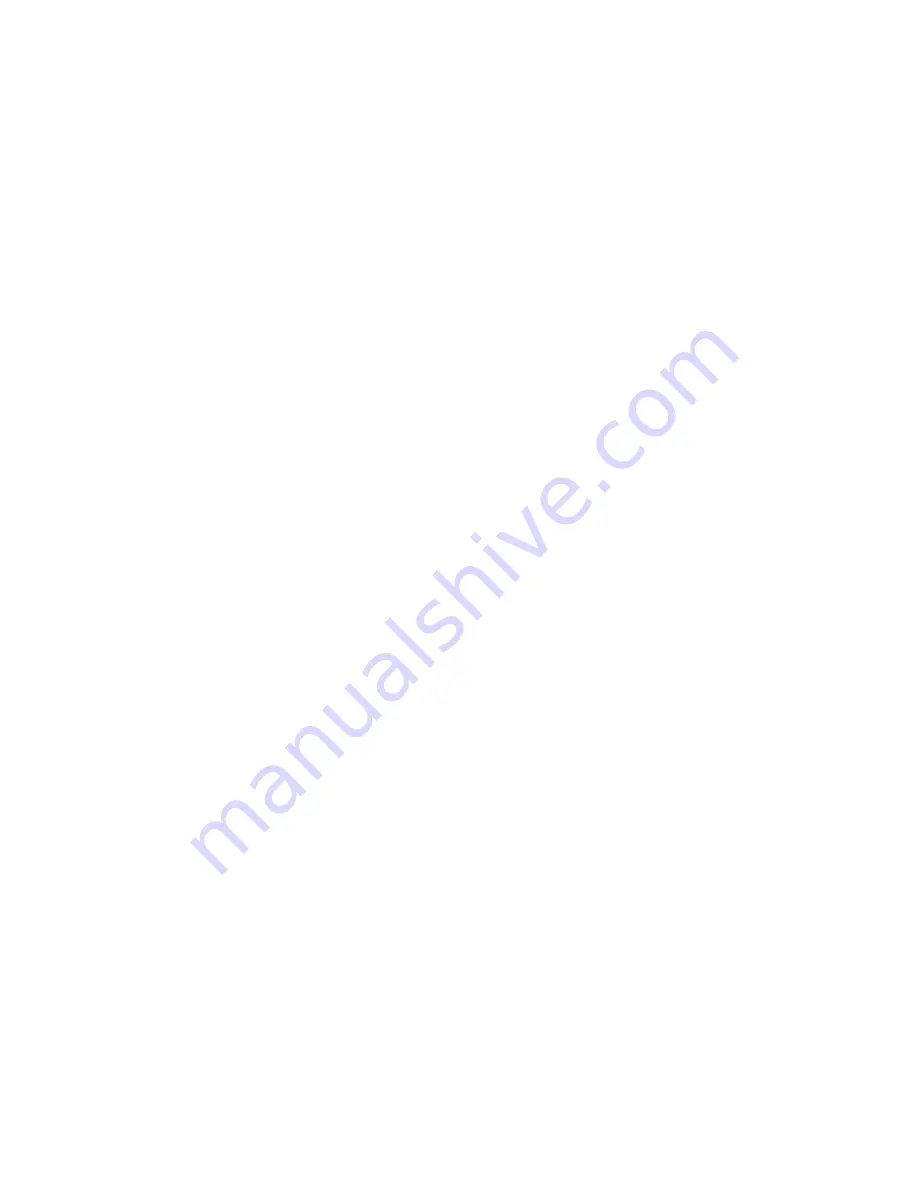
MedWeld 5000 Overview
MedWeld 5000 Technical Reference Manual
1 - 5
M-032170
DeviceNet Integration
This integration scheme supports a network of DeviceNet devices,
allowing for rapid communications between industrial devices.
The DeviceNet communications protocol is an open network standard,
maintained by the Open DeviceNet Vendor Association (ODVA). The
DeviceNet protocol allows for peer-to-peer data (where any product can
produce or consume messages and the DeviceNet product can function
as Client, Server or both. The network can have up to 64 node
addresses, and each node supports an infinite number of I/O.
NOTE:
For more information on DeviceNet, contact your WTC representative.
Timer Interface to the
Inverter
The interface between the timer unit and the MFDC inverter allows the
MedWeld 5000 to specify the amount of current to the work piece, allow
the inverter to alert the timer of fault conditions it detects during the
weld, and provides weld data to the timer, which is then displayed on the
DEP.
The inverter responds to the gating signals from the timer unit. The
timer unit tells the inverter when to pull in the main isolation contactor
and receives the signal from the inverter when the inverter is ready to
weld.
Timer Unit Output
The timer unit activates the Turn On The Isolation Contactor output to
the inverter when it executes Function #88 in the weld sequence. This
output is NOT directly wired to the isolation contactor: It sends a signal
to the inverter that the contactor should be pulled in. (The inverter’s
regulator board receives the signal. The regulator board is wired to the
isolation contactor.)
Timer Unit Input
The timer unit receives the isolation contactor input directly from the
isolation contactor. This input indicates the status of the contactor
(pulled in or dropped out).
The timer unit also receives a Ready to Weld signal from the inverter
(IRTW). This indicates when the inverter is capable of providing weld
current:
•
The inverter thermal switches indicate that cooling water is present
•
The isolation contactor can be pulled in
•
The inverter capacitors are ready for charging (to provide DC bus
voltage).
Summary of Contents for MedWeld 5000
Page 2: ...MedWeld 5000 Technical Reference Manual Modified 1 31 06 M 032170...
Page 6: ...MedWeld 5000 Technical Reference Manual Modified 1 31 06...
Page 38: ...Installing the MedWeld 5000 2 12 MedWeld 5000 Technical Reference Manual M 032170...
Page 82: ...Advanced Software Features 5 12 MedWeld 5000 Technical Reference Manual M 032170...
Page 120: ...Hardware Troubleshooting 9 10 MedWeld 5000 Technical Reference Manual M 032170...