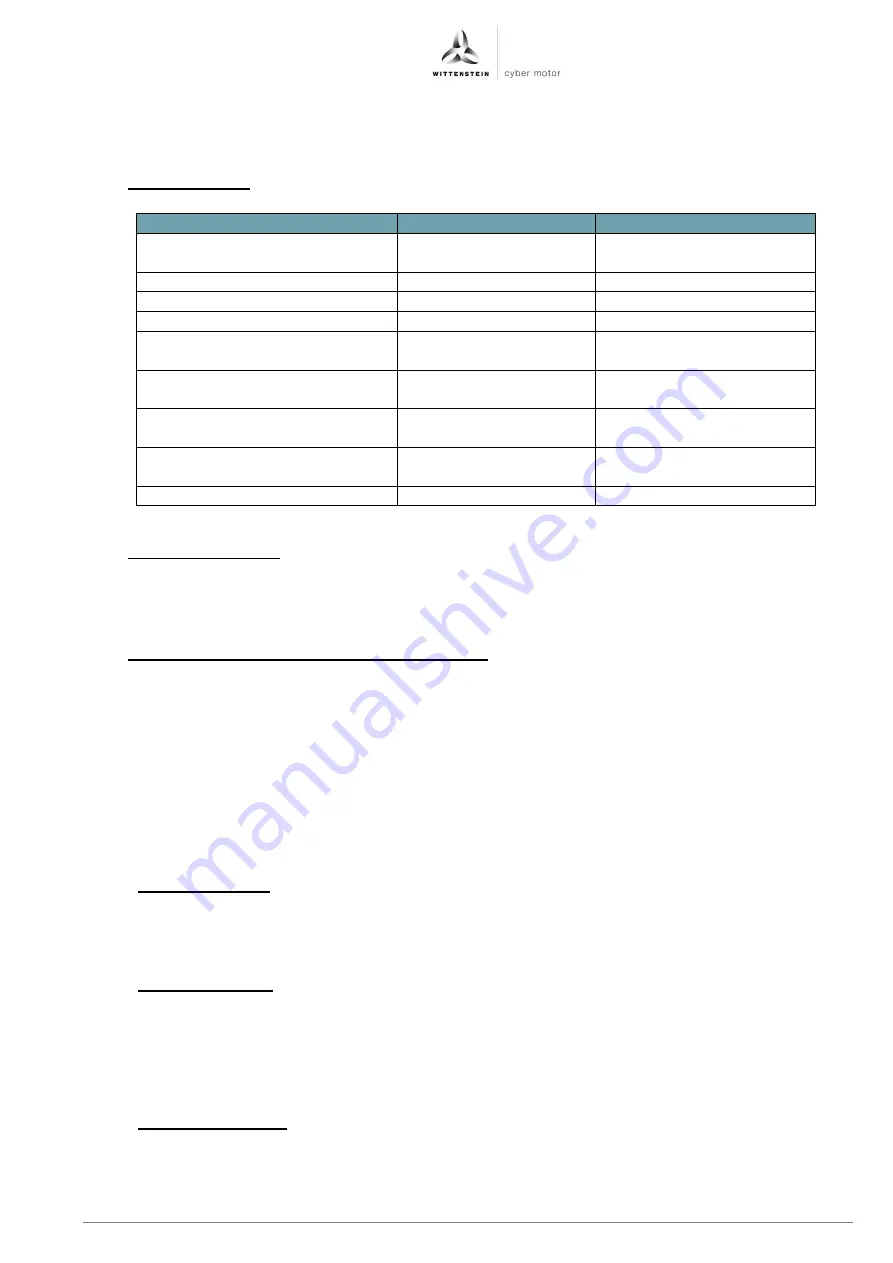
cyber
®
dynamic system
Operating manual
Revision: 01
Doc. no.: 5022-D056658
en-15
Customized deviations are permissible.
The data matrix code (DMC) is in the format C18x18 according to ECC200. It contains the
service portal address including the service portal code.
3.4 Electrical data
Electrical data
Unit
Value
Nominal supply voltage,
intermediate circuit
V DC
48
Nominal power
W
nom. 150 / max. 500
Intermediate circuit voltage
V DC
12
… 60
Logic power supply
V DC
12
… 60
Current consumption of
logic supply
mA DC
50 ... 230
Nominal output current of
the output stage
Aeff
3.3
Peak output current of the
output stage (for 5s)
Aeff
11.5
Clock frequency of the
output stage
kHz
16
STO voltage
V
12
… 60
Table 5: Electrical data
3.5 Performance data
Refer to the system characteristics (5012
–...) for the maximum permissible technical data.
For additional information, please contact our Sales department. Always state the
serial number (SN) when doing so.
3.6 Description of the cyber
®
dynamic system
WITTENSTEIN cyber
®
dynamic system
is an intelligent drive system with a continuous power
of up to 137
W and a peak output of up to 315 kW.
The housing with protection class IP65 enables decentralized assembly, which means that the
drive system can be integrated modularly and flexibly in the machine structure, reducing wiring.
Depending on the device version, CANopen according to DS402, EtherCAT with CoE,
PROFINET RT/IRT, Ethernet/IP Cip Sync or SERCOS III with FSP Drive is available as
a communication interface.
The intelligence is reflected in high-resolution power regulation and decentralized motion tasks.
Intuitive startup and diagnosis is possible using the PC-based, MotionGUI 2 graphic user
interface.
3.6.1 Integrated safety
-
Comprehensive functions to protect the drive system, such as overvoltage, overcurrent,
short circuit or ground fault.
-
Temperature monitoring of the drive system
3.6.2 Digital regulation
-
Digital d-q current controller (PI) with a sampling rate of up to 32 kHz
-
Digital position and speed controller (PI) with a sampling rate of 8 kHz
-
Feed forward control of speed and current possible
-
Pulse width modulation with a clock rate of 16 kHz
-
Anti-windup structure for all controllers
3.6.3 Inputs and outputs
-
4 programmable galvanically isolated digital inputs, 24 V
-
2 programmable galvanically isolated digital outputs, 24 V (short-circuit proof)