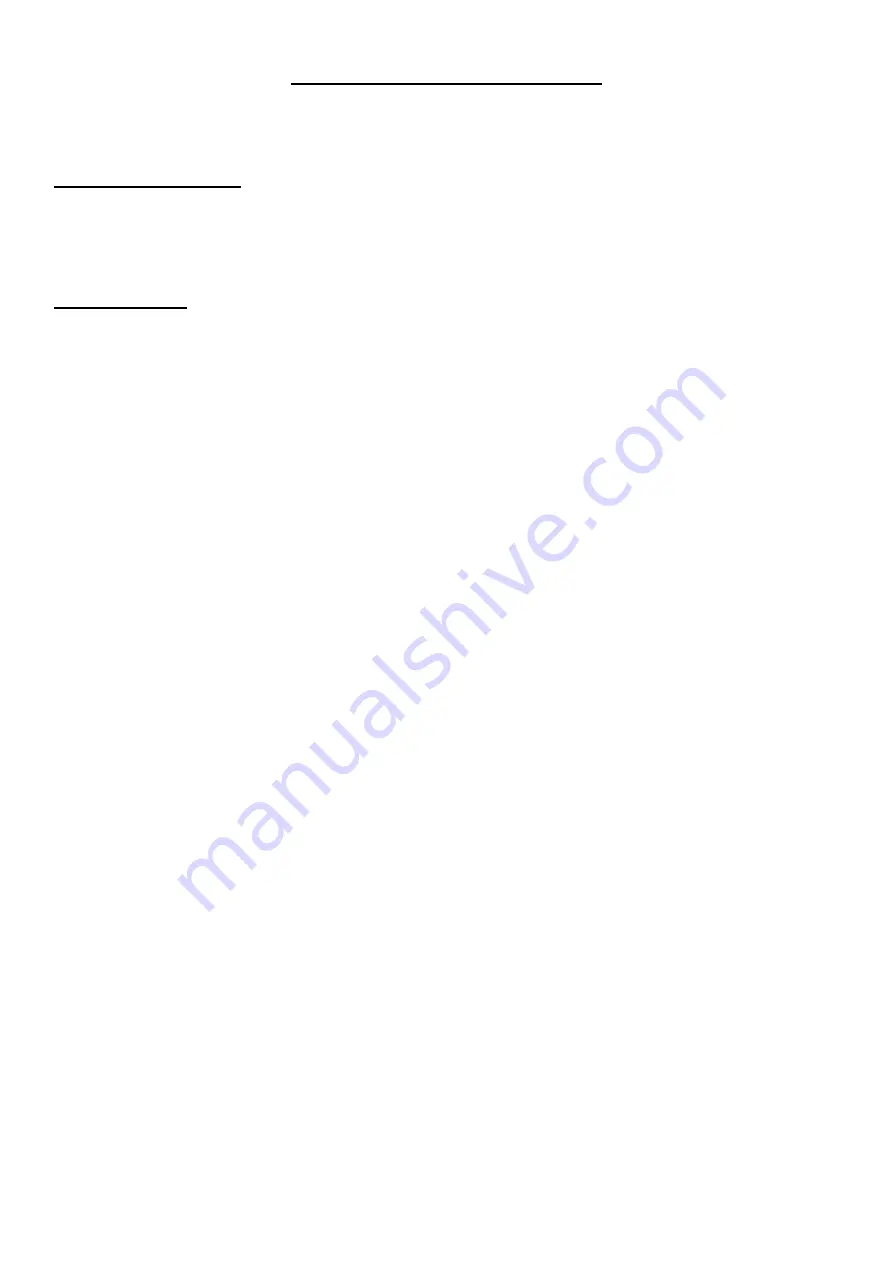
MAINTENANCE OF MIXER
IMPORTANT NOTE:
Ensure that all maintenance is carried out in accordance with the Parts and Operating
Manual and Proprietary Manufacturer’s specific instruction.
PROCEDURE
1
ISOLATE ELECTRICAL, PNEUMATIC AND OTHER SERVICES TO THE
MIXER (see separate section).
2
Service at recommended intervals.
3
Use Croker manufactured replacement parts available from
WINGET LIMITED
.
4
Ensure all safety guards and interlocks are reinstated prior to operating the mixer
.
5
Main items of wear (see Section 4).
A)
Star Blades
B)
Fixed Blade
C)
Discharge Blade
D)
Whirler Blades
Access to mixing pan internals is via the safety interlocks. Each of the above are
bolted components and are replaced by simple method and usually achieved in situ
without dismantling other components.
E)
Pan base and rim wearing plates are also bolted construction and can be
replaced in situ. However, pan covers will need to be dismantled to provide the
necessary access.
F)
Other items prone to less wear are star blade fingers, lower whirler shaft
assembly and mixing star. Each can be replaced again in situ but pan covers
would require tensing to provide necessary access.
G)
Pan rollers can be adjusted to accommodate wear during operation. These can
be replaced when required in situ using jacking method to support pan and
provide the necessary access.
Summary of Contents for Crocker RP1500XD
Page 4: ...OPERATING AND MAINTENANCE MANUAL SECTION 1 GENERAL INFORMATION...
Page 11: ...Miscellaneous 10 1 Noise measured in accordance with Directive 79 113 EEC 85LPA...
Page 12: ...RP1500XD GENERAL ARRANGEMENT...
Page 13: ...RP1500XD GENERAL ARRANGEMENT WITH LOADER...
Page 14: ...INTENTIONALLY BLANK PAGE...
Page 15: ...OPERATING AND MAINTENANCE MANUAL SECTION 2 INSTALLATION AND OPERATING INSTRUCTIONS...
Page 25: ...OPERATING AND MAINTENANCE MANUAL SECTION 3 TECHNICAL SPECIFICATION AND MAINTENANCE...
Page 27: ...MACHINE SAFETY DIRECTIVE All Gears are suitably guarded...
Page 33: ...LUBRICATION LAYOUT...
Page 35: ...INTENTIONALLY BLANK PAGE...
Page 36: ...OPERATING AND MAINTENANCE MANUAL SECTION 4 MIXER SPARE PARTS...
Page 37: ...INTENTIONALLY BLANK PAGE...
Page 38: ...INTENTIONALLY BLANK PAGE...
Page 39: ...RP1500XD PAN PAN DRIVE...
Page 42: ...RP1500XD PAN ROLLER ASSEMBLY...
Page 44: ...RP1500XD PAN LOCATING ROLLER...
Page 47: ...RP1500XD STAR DRIVE...
Page 50: ...RP1500XD DISCHARGE BLADE FIXED BLADE...
Page 53: ...RP1500XD DISCHARGE DOOR AIR CYLINDER...
Page 56: ...RP1500XD PAN GUARDS...
Page 58: ...RP1500XD PAN SEALING STRIP...
Page 60: ...RP1500XD DECALS AND LOGOS CROKER CUMFLOW RP1500XD 1 2 4 5 6 7 8 9 10 11 12 13 14...
Page 62: ...INTENTIONALLY BLANK PAGE...
Page 63: ...INTENTIONALLY BLANK PAGE...
Page 64: ...OPERATING AND MAINTENANCE MANUAL SECTION 5 ANCILLARY EQUIPMENT SPARE PARTS...
Page 65: ...RP1500XD WINCH UNIT...
Page 67: ...RP1500XD LOADER RUNWAY ASSEMBLY...
Page 69: ...RP1500XD LOADING HOPPER...
Page 71: ...RP1500XD SPLIT SHAFT WHIRLER FROM SERIAL NUMBER 6066...
Page 74: ...RP1500XD SPLIT SHAFT WHIRLER...
Page 76: ...RP1500XD FIXED SHAFT WHIRLER...
Page 78: ...RP1500XD WEIGHING FRAME...
Page 82: ...RP1500XD WIRE ROPE RENEWAL PROCEDURE...
Page 86: ...180 LITRE WATER TANK...
Page 89: ...INTENTIONALLY BLANK PAGE...
Page 90: ...INTENTIONALLY BLANK PAGE...
Page 91: ...OPERATING AND MAINTENANCE MANUAL SECTION 6 ELECTRICAL SYSTEM...
Page 93: ...RP1500XD TYPICAL LAYOUT OF STARTERS...
Page 97: ......
Page 100: ...OPERATING AND MAINTENANCE MANUAL SECTION 7 PNEUMATIC SYSTEM...
Page 102: ...RP1500XD PNEUMATIC CIRCUIT...
Page 104: ...INTENTIONALLY BLANK PAGE...
Page 105: ...OPERATING AND MAINTENANCE MANUAL SECTION 8 MISCELLANEOUS...
Page 107: ...INTENTIONALLY BLANK PAGE...
Page 108: ...INTENTIONALLY BLANK PAGE...
Page 109: ...INTENTIONALLY BLANK PAGE...
Page 110: ...INTENTIONALLY BLANK PAGE...
Page 111: ...OPERATING AND MAINTENANCE MANUAL SECTION 9 ELECTRONIC LOADCELL INDICATOR READOUT BOX...
Page 112: ......
Page 113: ......
Page 114: ......
Page 115: ......
Page 116: ......
Page 117: ......
Page 118: ......
Page 119: ......
Page 120: ......
Page 121: ......
Page 122: ...INTENTIONALLY BLANK PAGE...