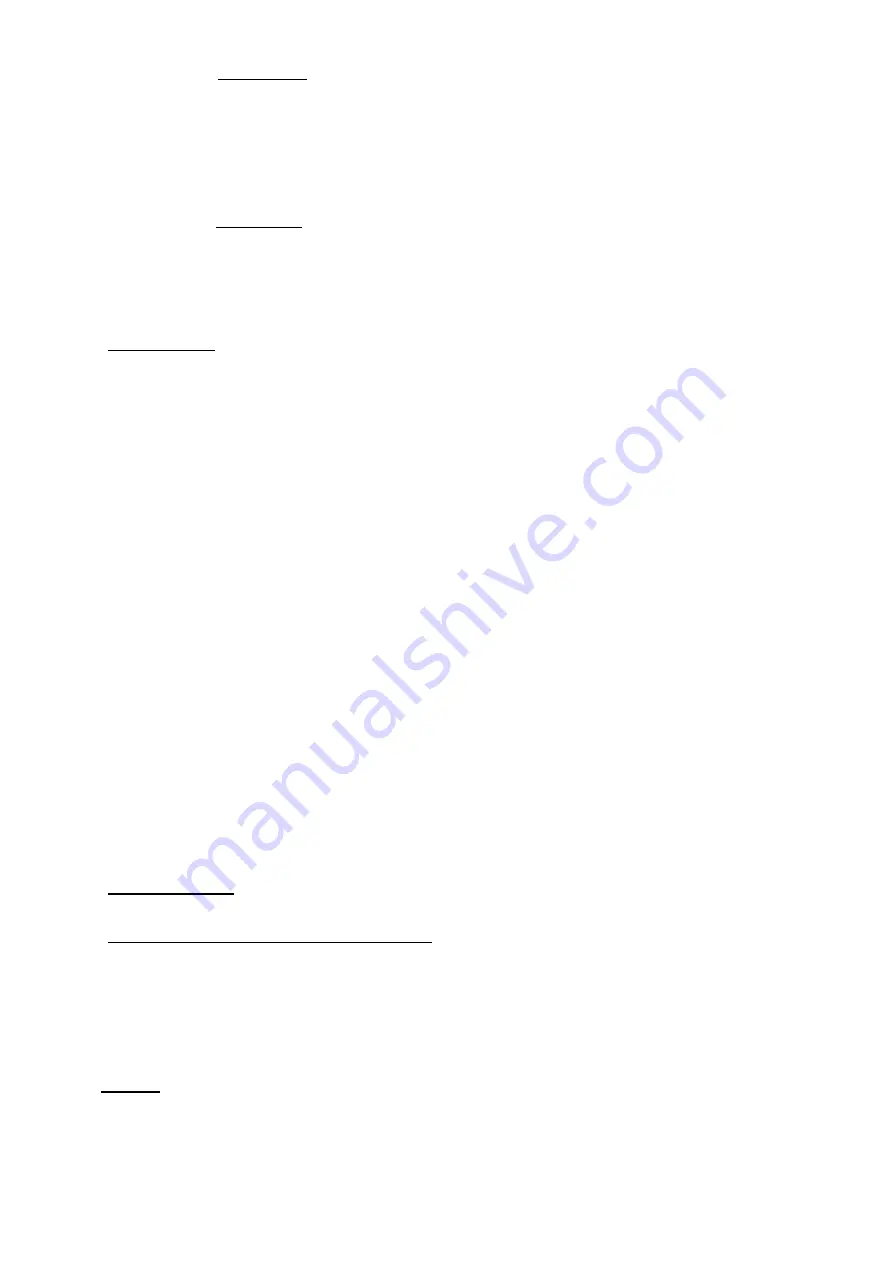
Mounting:
Set the brake so that the horizontal centre-line of the shoe corresponds
with the centre-line of the brake wheel shaft and the shoe pivots are
equally spaced from the vertical centre-line.
Installing:
Slacken back equalising screw (Item 14) Slack nut (Item 5) and adjust
screw (Item 3) to give required braking torque.
WARNING:
The end of the adjusting screw (Item 3) must always be visible in the hole at the end
of the adjusting nut (Item 6).
Set nuts (Item 5) so that contact is made with the load spring block in the shoe lever
when solenoid plunger has moved through half its stoke. Once properly set, this
setting should not be altered. With solenoid plunger right down, set equalising screw
(Item 14) to give equal friction lining clearances.
Tighten locknuts (Item 5 & Item 14) and be sure that the load spring bracket is in
place.
Check adjustments frequently and lubricate brake shoe pivots. To adjust for ware,
screw in adjusting screw (Item 3) until the adjusting nuts are clear and only touch
lever (Item 1) when plunger is depressed through half its stroke.
When new linings are fitted, repeat all adjustments.
Orders and enquiries should always state full description of parts required. The serial
number on the brake should always be quoted.
ANNUALLY:
Worm Reduction Gear Unit (Flender):
Drain and clean out the gear case and refill with Total Carter EP220 or equivalent.
When running conditions are severe this procedure should be adopted more
frequently. (Approx capacities – 10 Imperial Pints: 5.7 Litres: 1.6 American Gallons).
NOTE
Electrical cables particularly those with copper conductors suffer from a
condition known as ‘relaxation’ which may cause wiring to work loose over a
period of time, it is recommended that the tightness of wiring connections and
terminals are checked following the first month in service.
Summary of Contents for Crocker RP1500XD
Page 4: ...OPERATING AND MAINTENANCE MANUAL SECTION 1 GENERAL INFORMATION...
Page 11: ...Miscellaneous 10 1 Noise measured in accordance with Directive 79 113 EEC 85LPA...
Page 12: ...RP1500XD GENERAL ARRANGEMENT...
Page 13: ...RP1500XD GENERAL ARRANGEMENT WITH LOADER...
Page 14: ...INTENTIONALLY BLANK PAGE...
Page 15: ...OPERATING AND MAINTENANCE MANUAL SECTION 2 INSTALLATION AND OPERATING INSTRUCTIONS...
Page 25: ...OPERATING AND MAINTENANCE MANUAL SECTION 3 TECHNICAL SPECIFICATION AND MAINTENANCE...
Page 27: ...MACHINE SAFETY DIRECTIVE All Gears are suitably guarded...
Page 33: ...LUBRICATION LAYOUT...
Page 35: ...INTENTIONALLY BLANK PAGE...
Page 36: ...OPERATING AND MAINTENANCE MANUAL SECTION 4 MIXER SPARE PARTS...
Page 37: ...INTENTIONALLY BLANK PAGE...
Page 38: ...INTENTIONALLY BLANK PAGE...
Page 39: ...RP1500XD PAN PAN DRIVE...
Page 42: ...RP1500XD PAN ROLLER ASSEMBLY...
Page 44: ...RP1500XD PAN LOCATING ROLLER...
Page 47: ...RP1500XD STAR DRIVE...
Page 50: ...RP1500XD DISCHARGE BLADE FIXED BLADE...
Page 53: ...RP1500XD DISCHARGE DOOR AIR CYLINDER...
Page 56: ...RP1500XD PAN GUARDS...
Page 58: ...RP1500XD PAN SEALING STRIP...
Page 60: ...RP1500XD DECALS AND LOGOS CROKER CUMFLOW RP1500XD 1 2 4 5 6 7 8 9 10 11 12 13 14...
Page 62: ...INTENTIONALLY BLANK PAGE...
Page 63: ...INTENTIONALLY BLANK PAGE...
Page 64: ...OPERATING AND MAINTENANCE MANUAL SECTION 5 ANCILLARY EQUIPMENT SPARE PARTS...
Page 65: ...RP1500XD WINCH UNIT...
Page 67: ...RP1500XD LOADER RUNWAY ASSEMBLY...
Page 69: ...RP1500XD LOADING HOPPER...
Page 71: ...RP1500XD SPLIT SHAFT WHIRLER FROM SERIAL NUMBER 6066...
Page 74: ...RP1500XD SPLIT SHAFT WHIRLER...
Page 76: ...RP1500XD FIXED SHAFT WHIRLER...
Page 78: ...RP1500XD WEIGHING FRAME...
Page 82: ...RP1500XD WIRE ROPE RENEWAL PROCEDURE...
Page 86: ...180 LITRE WATER TANK...
Page 89: ...INTENTIONALLY BLANK PAGE...
Page 90: ...INTENTIONALLY BLANK PAGE...
Page 91: ...OPERATING AND MAINTENANCE MANUAL SECTION 6 ELECTRICAL SYSTEM...
Page 93: ...RP1500XD TYPICAL LAYOUT OF STARTERS...
Page 97: ......
Page 100: ...OPERATING AND MAINTENANCE MANUAL SECTION 7 PNEUMATIC SYSTEM...
Page 102: ...RP1500XD PNEUMATIC CIRCUIT...
Page 104: ...INTENTIONALLY BLANK PAGE...
Page 105: ...OPERATING AND MAINTENANCE MANUAL SECTION 8 MISCELLANEOUS...
Page 107: ...INTENTIONALLY BLANK PAGE...
Page 108: ...INTENTIONALLY BLANK PAGE...
Page 109: ...INTENTIONALLY BLANK PAGE...
Page 110: ...INTENTIONALLY BLANK PAGE...
Page 111: ...OPERATING AND MAINTENANCE MANUAL SECTION 9 ELECTRONIC LOADCELL INDICATOR READOUT BOX...
Page 112: ......
Page 113: ......
Page 114: ......
Page 115: ......
Page 116: ......
Page 117: ......
Page 118: ......
Page 119: ......
Page 120: ......
Page 121: ......
Page 122: ...INTENTIONALLY BLANK PAGE...