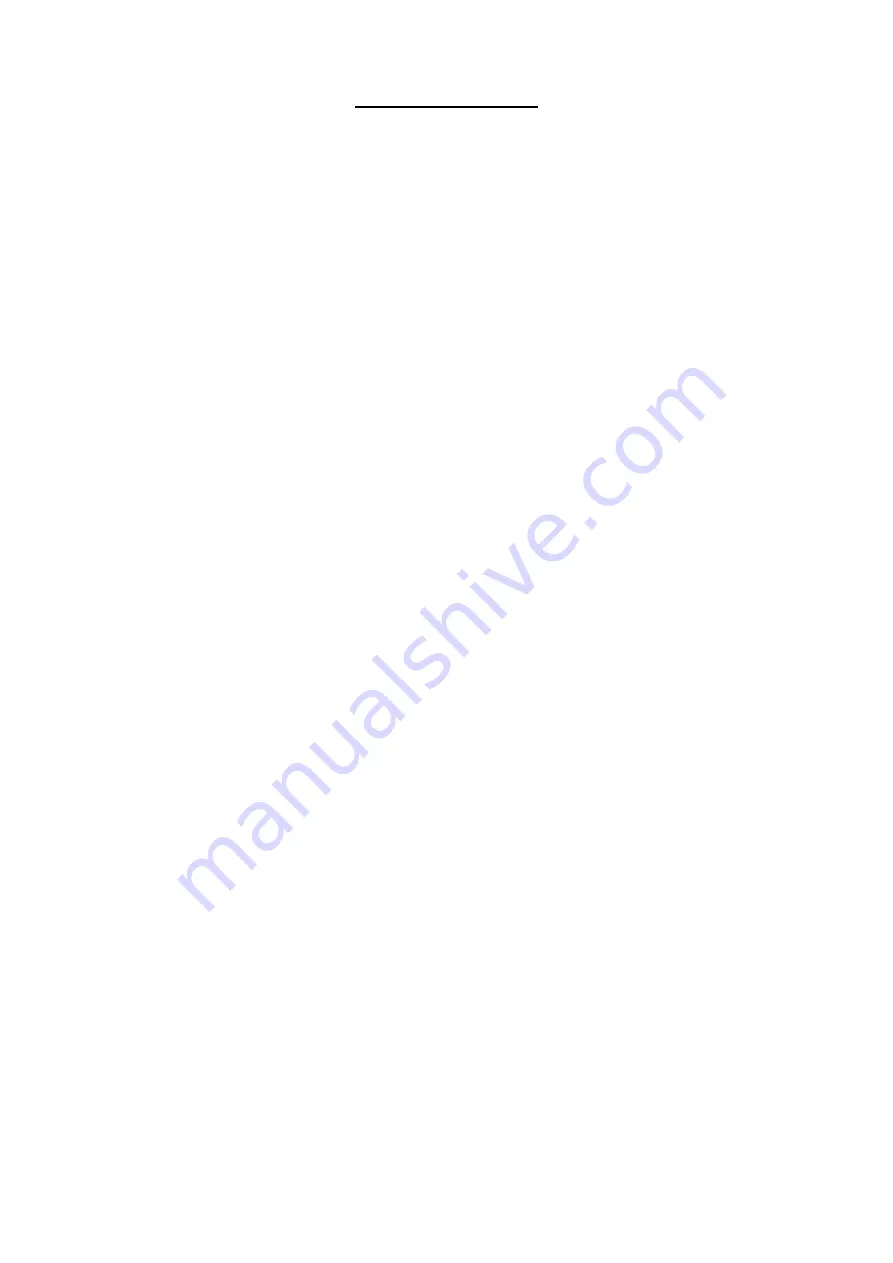
INSTALLATION
Please refer to contract arrangement and site instructions as applicable.
It is recommended that a concrete foundation (to take foundation bolts – not
supplied) of at least 0.6m
2
by 0.3m thick to take M20 bolts should be provided
for each leg of the support structure and runway when fitted. When the machine
is supplied without a support structure it should be mounted on supports of
sufficient strength and rigidity to prevent undue vibration when the machine is
working. When making provision for a loading hopper pit it is strongly
recommended that the pit is concreted out so that it can easily be kept clean and
free from any build up which could prevent the bottom limit switch from
operating correctly.
Before completing the installation, check that the main mixer frame is level
with a spirit level. Packings should be inserted as required under the structure
legs or main frame. The packings under the mixing pan roller brackets are set
during manufacturing and must not be disturbed under any circumstances.
Check that the pan is seated and that the pan rack and drive gear are in mesh..
Also check that all the blade clearances are in line with the maintenance
instructions.
On connecting to the power supply, the wiring diagram must be referred to.
A check that the wiring is correct is the rotation of the following:-
•
The mixing pan and mixing star rotate anti-clockwise when looking from
the top.
•
The loader winch rotates anti-clockwise looking from the rope drum end
when the raise button is pressed.
•
The whirler unit rotates clockwise when looking from the top.
It is advisable to mount the starters away from the machine on supports free
from vibration. Ensure that the starters are fitted with suitable overloads – see
technical specification – power units.
Note:- it is recommended that the
mains electrical supply is taken via an earth leakage circuit breaker.
A simple Water Flow Meter is available as an option to the water tank, this has
a range of 0-100 litres and features an adjustable flow indicator with a reset
facility allowing very accurate measurement of water flow irrespective of the
pressure. The Flow Meter is normally fitted with a manual ‘on/off’ valve and is
protected by a washable in line strainer.
Summary of Contents for Crocker RP1500XD
Page 4: ...OPERATING AND MAINTENANCE MANUAL SECTION 1 GENERAL INFORMATION...
Page 11: ...Miscellaneous 10 1 Noise measured in accordance with Directive 79 113 EEC 85LPA...
Page 12: ...RP1500XD GENERAL ARRANGEMENT...
Page 13: ...RP1500XD GENERAL ARRANGEMENT WITH LOADER...
Page 14: ...INTENTIONALLY BLANK PAGE...
Page 15: ...OPERATING AND MAINTENANCE MANUAL SECTION 2 INSTALLATION AND OPERATING INSTRUCTIONS...
Page 25: ...OPERATING AND MAINTENANCE MANUAL SECTION 3 TECHNICAL SPECIFICATION AND MAINTENANCE...
Page 27: ...MACHINE SAFETY DIRECTIVE All Gears are suitably guarded...
Page 33: ...LUBRICATION LAYOUT...
Page 35: ...INTENTIONALLY BLANK PAGE...
Page 36: ...OPERATING AND MAINTENANCE MANUAL SECTION 4 MIXER SPARE PARTS...
Page 37: ...INTENTIONALLY BLANK PAGE...
Page 38: ...INTENTIONALLY BLANK PAGE...
Page 39: ...RP1500XD PAN PAN DRIVE...
Page 42: ...RP1500XD PAN ROLLER ASSEMBLY...
Page 44: ...RP1500XD PAN LOCATING ROLLER...
Page 47: ...RP1500XD STAR DRIVE...
Page 50: ...RP1500XD DISCHARGE BLADE FIXED BLADE...
Page 53: ...RP1500XD DISCHARGE DOOR AIR CYLINDER...
Page 56: ...RP1500XD PAN GUARDS...
Page 58: ...RP1500XD PAN SEALING STRIP...
Page 60: ...RP1500XD DECALS AND LOGOS CROKER CUMFLOW RP1500XD 1 2 4 5 6 7 8 9 10 11 12 13 14...
Page 62: ...INTENTIONALLY BLANK PAGE...
Page 63: ...INTENTIONALLY BLANK PAGE...
Page 64: ...OPERATING AND MAINTENANCE MANUAL SECTION 5 ANCILLARY EQUIPMENT SPARE PARTS...
Page 65: ...RP1500XD WINCH UNIT...
Page 67: ...RP1500XD LOADER RUNWAY ASSEMBLY...
Page 69: ...RP1500XD LOADING HOPPER...
Page 71: ...RP1500XD SPLIT SHAFT WHIRLER FROM SERIAL NUMBER 6066...
Page 74: ...RP1500XD SPLIT SHAFT WHIRLER...
Page 76: ...RP1500XD FIXED SHAFT WHIRLER...
Page 78: ...RP1500XD WEIGHING FRAME...
Page 82: ...RP1500XD WIRE ROPE RENEWAL PROCEDURE...
Page 86: ...180 LITRE WATER TANK...
Page 89: ...INTENTIONALLY BLANK PAGE...
Page 90: ...INTENTIONALLY BLANK PAGE...
Page 91: ...OPERATING AND MAINTENANCE MANUAL SECTION 6 ELECTRICAL SYSTEM...
Page 93: ...RP1500XD TYPICAL LAYOUT OF STARTERS...
Page 97: ......
Page 100: ...OPERATING AND MAINTENANCE MANUAL SECTION 7 PNEUMATIC SYSTEM...
Page 102: ...RP1500XD PNEUMATIC CIRCUIT...
Page 104: ...INTENTIONALLY BLANK PAGE...
Page 105: ...OPERATING AND MAINTENANCE MANUAL SECTION 8 MISCELLANEOUS...
Page 107: ...INTENTIONALLY BLANK PAGE...
Page 108: ...INTENTIONALLY BLANK PAGE...
Page 109: ...INTENTIONALLY BLANK PAGE...
Page 110: ...INTENTIONALLY BLANK PAGE...
Page 111: ...OPERATING AND MAINTENANCE MANUAL SECTION 9 ELECTRONIC LOADCELL INDICATOR READOUT BOX...
Page 112: ......
Page 113: ......
Page 114: ......
Page 115: ......
Page 116: ......
Page 117: ......
Page 118: ......
Page 119: ......
Page 120: ......
Page 121: ......
Page 122: ...INTENTIONALLY BLANK PAGE...