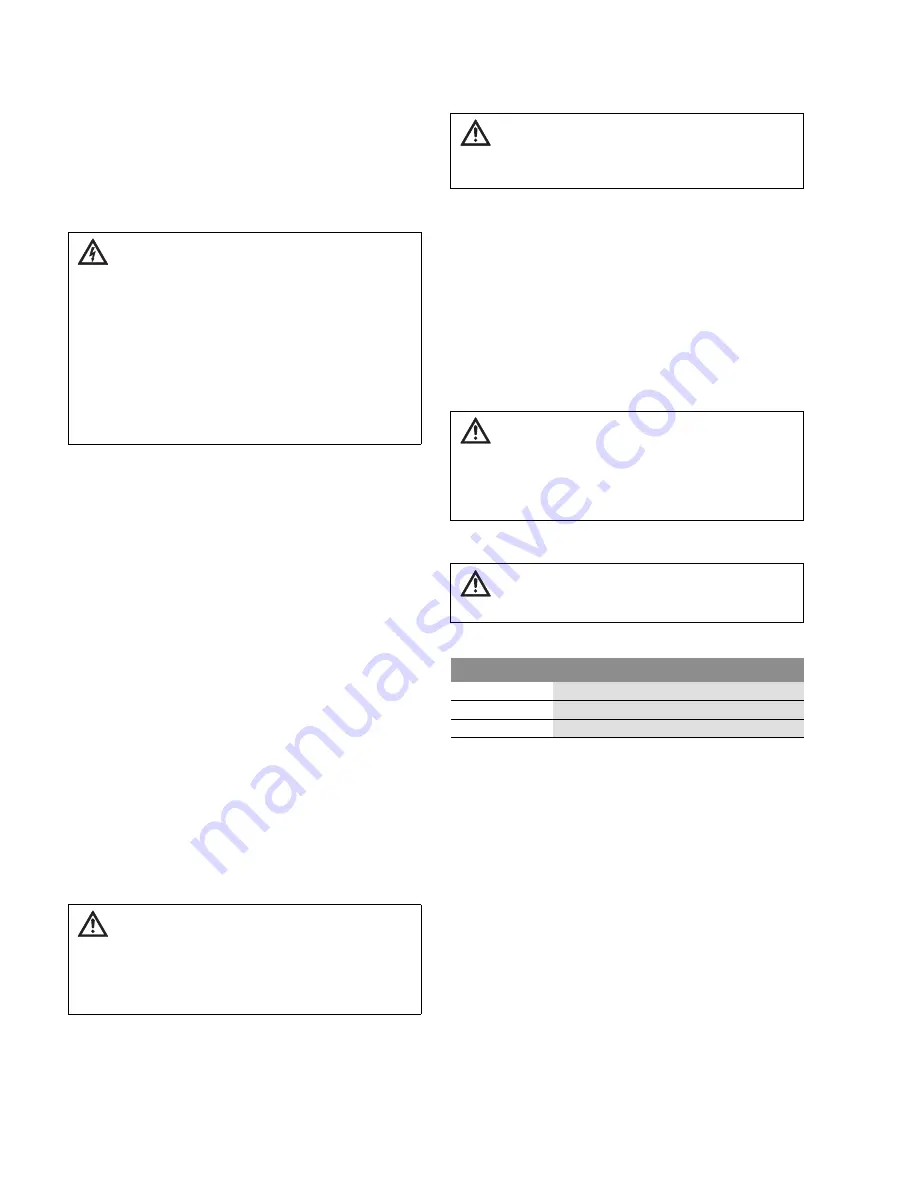
English
6
WILO SE 03/2009
• For direct connection to a public drinking water sys-
tem, the suction pipe must also have a check valve
and an isolation valve.
• For indirect connection via a tank, the suction pipe
must have a strainer, to keep any impurities out of
the pump.
7.2 Electrical connection
• The operating voltage and frequency are marked on
the nameplate.
• The pump must be connected to the power supply
by a solid cable equipped with a grounded plug-con-
nection or a main power switch.
• Three-Phase motors must be connected to an
approved motor starter. The set nominal current of
which must correspond to the electrical data on the
pump name plate
• The supply cable must be laid so that it never
touches the pipework and/or the pump and motor
casing.
• The pump/installation should be grounded in com-
pliance with local regulations. A ground fault inter-
rupter can be used as extra protection.
• The motor has a thermal overload sensor and con-
tact (P1 & P2 in the motor control box), normally
closed no load (potential free) type, maximum volt-
age 250 V.
• The connection to the power supply must be in
accordance with the connection plan (see fig. 4).
8 Start up
8.1 Preliminary rinsing
8.2 System filling - Venting
Air evacuation process (see fig. 3):
• Close the two isolation valves and give one and an
half to two turns of the air bleed screw (fig. 3 -
item 5).
• Slowly open the isolation valve on the suction side
until air escapes at the air bleed screw and the
pumped liquid flows. The escaping air produces a
clearly audible whistle. Retighten the air bleed
screw.
• Slowly open the isolation valve on the discharge
side. The gauge on the discharge side is used to
monitor the pressure.
8.3 Starting up
Minimum continuous flow is:
WARNING! Electrical shock hazard
Dangers caused by electrical energy must be
excluded.
• Electrical work by a qualified electrician only!
• National Electrical Codes, local codes and regula-
tions must be strictly followed.
• All electrical connections must be performed
after the electrical supply has been switched off
and secured against unauthorized switching.
• For safe installation and operation a proper
grounding of the pump to the power supply’s
grounding terminals is required.
WARNING! Health hazard
Each pump could be tested regarding hydraulic
features in factory, some water may remain in
them. It is recommended for hygiene purposes, to
flush the pump of any fluids used during testing
before any using with potable water supply.
CAUTION! Possible damage of the pump
Never operate the pump dry.
The system must be filled before starting the
pump. Ensure that all isolation valves are open.
WARNING! Bodily injury
Pump under pressure! When the pumped liquid is
hot and the pressure high, the stream escaping at
the air bleed screw may cause burns or other inju-
ries. For this reason, the air bleed screw should
only be loosened a turn and a half.
CAUTION! Possible damage of the pump
The pump must not operate at zero flow (closed
discharge valve)
Pump type
Min Flow
Max Flow
MVIS 15
1.7 GPM (0.4 m
3
/h)
30 GPM (7 m3/h)
MVIS 30
2.6 GPM (0.5 m
3
/h)
44 GPM (10 m3/h)
MVIS 50
4.4 GPM (1 m
3
/h)
75 GPM (17 m3/h)