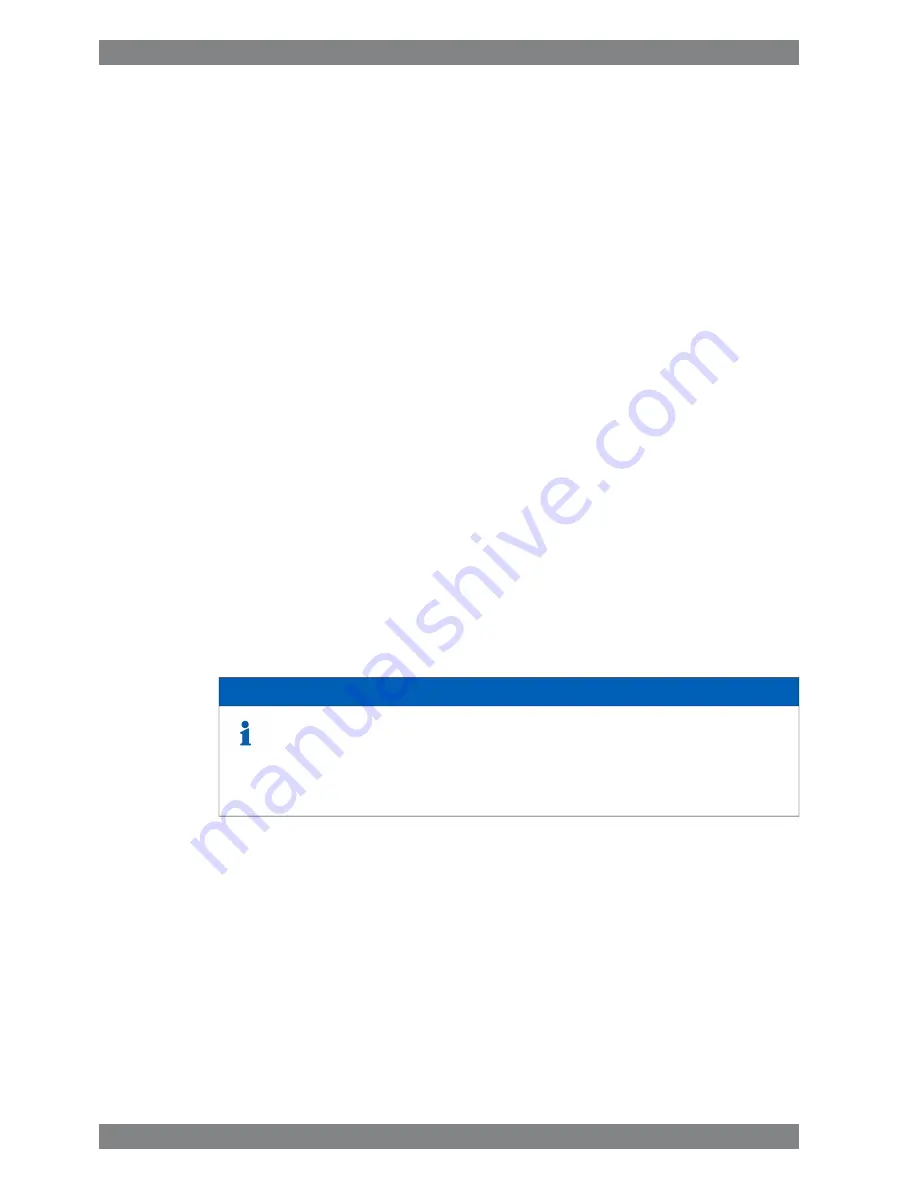
There are separate pipe connections for the main fuel oil and pilot fuel oil. Main fuel oil can
be Marine Diesel Fuel (MDF) or Heavy Fuel Oil (HFO). Pilot fuel oil is always MDF and the pilot
fuel system is in operation in both gas- and diesel mode operation.
A pressure control valve in the main fuel oil return line on the engine maintains desired pressure
before the injection pumps.
Leak fuel system
Clean leak fuel from the injection valves and the injection pumps is collected on the engine
and drained by gravity through a clean leak fuel connection. The clean leak fuel can be re-used
without separation. The quantity of clean leak fuel is given in chapter Technical data.
Other possible leak fuel and spilled water and oil is separately drained from the hot-box through
dirty fuel oil connections and it shall be led to a sludge tank.
6.4.2
External fuel oil system
The design of the external fuel system may vary from ship to ship, but every system should
provide well cleaned fuel of correct viscosity and pressure to each engine. Temperature control
is required to maintain stable and correct viscosity of the fuel before the injection pumps (see
Technical data). Sufficient circulation through every engine connected to the same circuit must
be ensured in all operating conditions.
The fuel treatment system should comprise at least one settling tank and two separators.
Correct dimensioning of HFO separators is of greatest importance, and therefore the
recommendations of the separator manufacturer must be closely followed. Poorly centrifuged
fuel is harmful to the engine and a high content of water may also damage the fuel feed system.
Injection pumps generate pressure pulses into the fuel feed and return piping. The fuel pipes
between the feed unit and the engine must be properly clamped to rigid structures. The
distance between the fixing points should be at close distance next to the engine. See chapter
Piping design, treatment and installation.
A connection for compressed air should be provided before the engine, together with a drain
from the fuel return line to the clean leakage fuel or overflow tank. With this arrangement it is
possible to blow out fuel from the engine prior to maintenance work, to avoid spilling.
NOTE
In multiple engine installations, where several engines are connected to the same
fuel feed circuit, it must be possible to close the fuel supply and return lines
connected to the engine individually. This is a SOLAS requirement. It is further
stipulated that the means of isolation shall not affect the operation of the other
engines, and it shall be possible to close the fuel lines from a position that is not
rendered inaccessible due to fire on any of the engines.
Fuel heating requirements HFO
Heating is required for:
●
Bunker tanks, settling tanks, day tanks
●
Pipes (trace heating)
●
Separators
●
Fuel feeder/booster units
To enable pumping the temperature of bunker tanks must always be maintained 5...10°C
above the pour point, typically at 40...50°C. The heating coils can be designed for a temperature
of 60°C.
The tank heating capacity is determined by the heat loss from the bunker tank and the desired
temperature increase rate.
6-22
Wärtsilä 50DF Product Guide - a16 - 9 September 2016
Wärtsilä 50DF Product Guide
6. Fuel System
Summary of Contents for WARTSILA 50DF
Page 1: ...WÄRTSILÄ 50DF PRODUCT GUIDE ...
Page 14: ...This page intentionally left blank ...
Page 40: ...This page intentionally left blank ...
Page 58: ...This page intentionally left blank ...
Page 102: ...This page intentionally left blank ...
Page 120: ...This page intentionally left blank ...
Page 154: ...This page intentionally left blank ...
Page 164: ...This page intentionally left blank ...
Page 176: ...This page intentionally left blank ...
Page 214: ...This page intentionally left blank ...
Page 232: ...This page intentionally left blank ...
Page 234: ...This page intentionally left blank ...
Page 237: ......
Page 238: ......
Page 239: ......