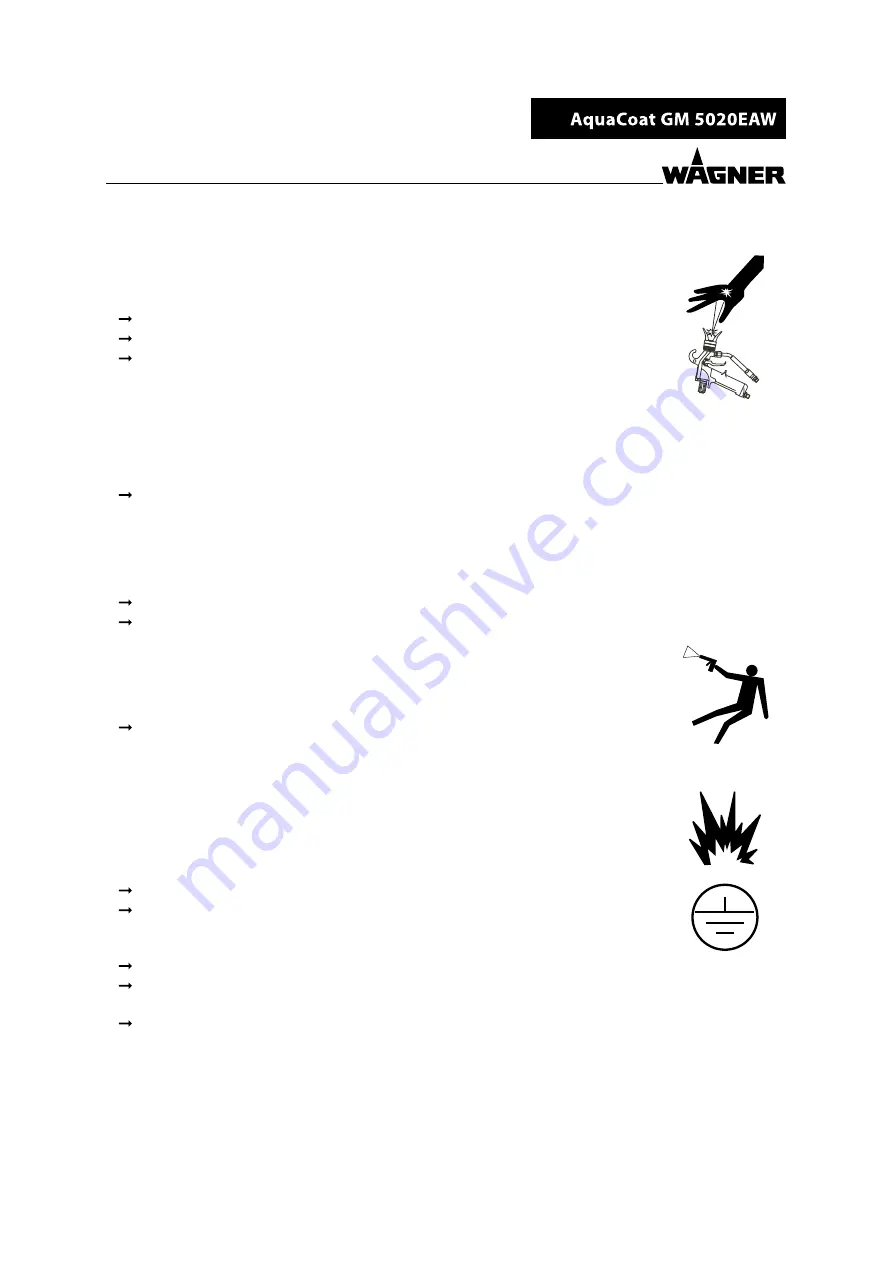
16
OPERATING MANUAL
VERSION 02/2018
ORDER NUMBER DOC 2366717
4.2.2 SAFE HANDLING OF WAGNER SPRAY DEVICES
Hazard due to injection of lacquer or flushing agent into the skin!
The spray jet is under pressure and can cause dangerous injuries. Avoid injection of paint
or flushing agents:
Never point the spray gun at people.
Never reach into the spray jet.
Before any work on the device, in the event of work interruptions and malfunctions:
– Switch off the energy/compressed air supply.
– Relieve the pressure from the spray gun and unit.
– Secure the spray gun against actuation.
– Disconnect the control unit from the mains.
– In the event of functional faults: remedy the fault as described in the "Troubleshooting"
chapter.
If needed, the liquid ejection devices must be checked by experts (e.g., WAGNER service
technician) at least every 12 months for their work-safe condition in accordance with
DGUV regulation 100-500 Chapter 2.29 and Chapter 2.36.
– For shut down devices, the examination can be suspended until the next start-up.
In the event of skin injuries caused by lacquer or flushing agents:
Note the lacquer or flushing agent that you have been using.
Consult a doctor immediately.
Danger due to recoil forces!
Actuating the trigger can causes strong recoil forces. Thereby the user can lose his balance
and injure himself during falling.
Avoid risk of injury from recoil forces:
Ensure that you have firm footing when operating the spray gun.
4.2.3 GROUND THE UNIT
Hazard due to electrostatic charge!
Risk of injury, explosion hazard and damage to the device.
Friction, flowing liquids and air or electrostatic coating processes create charges. Flames or
sparks can form during discharge.
Correct grounding of the entire spraying system prevents electrostatic charges.
Ensure that all devices and tanks are grounded before each spraying process.
Make sure that the ground and potential equalization of all system parts are performed
reliably and continuously and can withstand the expected stress (e.g., mechanical stress,
corrosion).
Ground the work pieces to be coated.
Ensure that all persons inside the working area are grounded, e.g., that they are
wearing static dissipative shoes.
Wear static dissipative gloves when spraying. The grounding takes place via the spray
gun handle or the trigger.