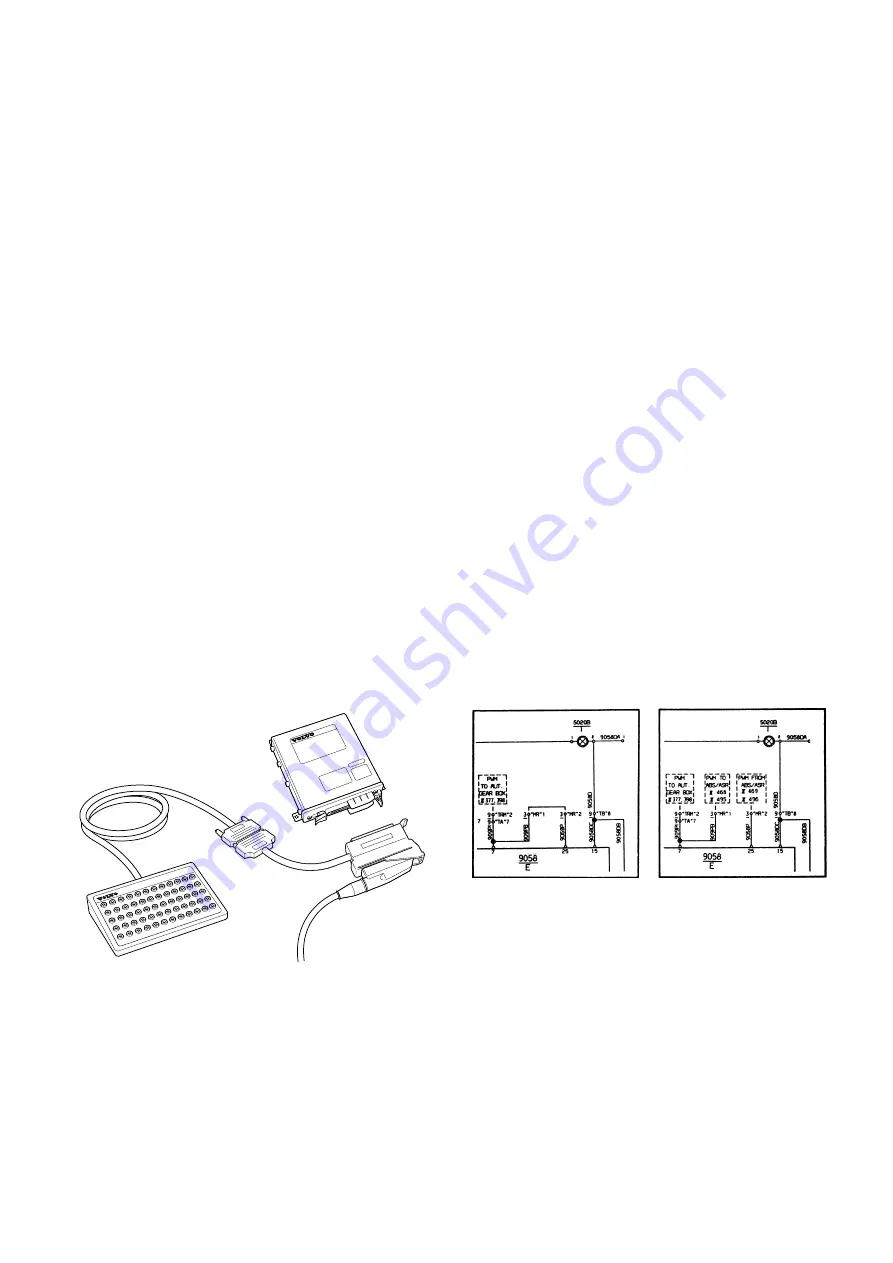
157
The following measurements are made with the engine started
Pin+
Pin–
Nominal value
Component
Remarks
32
19
9.7 V ~ (300 Hz)
Speed sensor, engine
low idle 5
32
19
9.4 V ~ (840 Hz)
Speed sensor, engine
1650 rpm 5
9
19
1.3–2.5 V ~ (70 Hz)
Speed signal, C3
30 km/h 6
9
19
2.2–3.3 V ~ (150 Hz)
Speed signal, C3
60 km/h 6
26
35
2.5–3.9 V
Intercooler temp. sensor
60
°
C 7
23
35
0.9–1.85 V
Coolant temp. sensor
60
°
C 8
34
19
2.5–4.0 V*
Turbopressure sensor
110–165 kPa 9
25
19
6.9–7.3 V ~
Without ASR
low idle
25
19
10–11.5 V ~
Without ASR
approx. 1650 rpm
25
19
ca 5.5 V~
With ASR
4
7
19
6.9–7.3 V ~
Signal to Automatic transmission and AST
control unit. Control value low idle
3
7
19
10–11.5 V ~
Signal to Automatic transmission and ASR
control unit. Control value 1650 rpm
3
28
35
2.6–3.05 V*
Control rod travel, accelerator pedal in max. position
and engine max. loaded. Measured while driving.
2
31
35
**
Speed sensor, injection pump
10
* Depending on engine variant, see Specifications.
** Measured with oscilloscope.
6
29
18–24 ohm
Control rod travel sensor, injection pump
2
6
10
18–24 ohm
Control rod travel sensor, injection pump
2
31
35
0.9–1.1 ohm
Speed sensor, injection pump
10
1
21
0.5–1.2 ohm
Adjuster device, injection pump
19
earth
ca 0 ohm
Control, earth connection
20
earth
ca 0 ohm
Control, earth connection
Measuring resistance, control unit
disconnected
NOTE! Never pull out or plug in the control unit cable
contact when the power supply (ignition) is on.
EDC
1
13
25
37
49
2
14
26
38
50
3
15
27
39
51
4
16
28
40
52
5
17
29
41
53
6
18
30
42
54
7
MÄTBOX
19
31
43
55
8
20
32
44
56
9
21
33
45
57
10
22
34
46
58
11
9813190
23
35
47
59
12
24
36
48
60
981 31 92
Without ASR
With ASR
Extract from “Wiring diagram EDC-system”