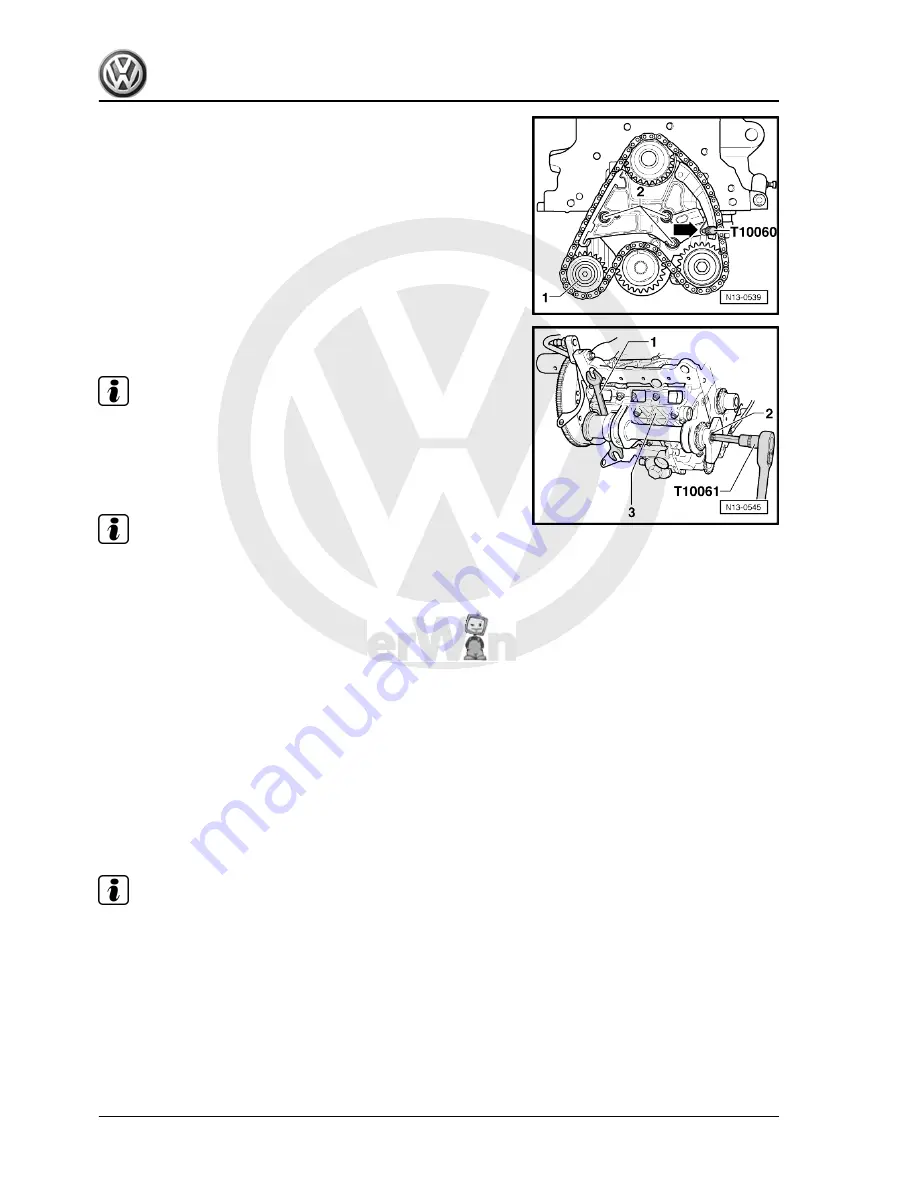
Pro
te
cte
d b
y c
op
yri
gh
t. C
op
yi
ng
fo
r p
riv
at
e
o
r c
o
m
m
e
rc
ia
l p
u
rp
o
s
e
s
, i
n
p
a
rt
o
r i
n
w
h
o
le
, i
s
n
o
t p
e
rm
itt
ed
u
nl
es
s a
ut
ho
ris
ed
by
Vo
lksw
agen
AG. Volkswagen AG doe
s not
gua
ran
tee
or a
cc
ep
t a
ny
lia
b
ilit
y w
ith
re
s
p
e
c
t t
o
th
e
c
o
rr
e
c
tn
e
s
s
o
f
in
fo
rm
a
tio
n
in
th
is
d
oc
um
en
t.
C
op
yrig
ht b
y V
olk
sw
age
n A
G.
– Immobilise chain tensioning element with Retaining pin -
T10060 A- -arrow-.
– Loosen the gear -1- from mounting frame.
– Remove securing bolt --2-- from chain tensioning element and
remove it.
– Remove the chain and put it on a clean surface.
– Immobilise counterbalance shaft, as shown, with a Spanner
(24/27 mm AF) -1-.
Note
When immobilizing the counterbalance shaft, make sure that the
spanner is centred on the counterbalance and at right angles to
counterbalance shaft.
– Loosen fastening bolt -2- of the counterbalance.
Note
Only loosen the fastening bolt -2- of the counterbalance; do not
remove.
– Unbolt mounting frame --3-- from engine block and remove it
with counterbalance shaft.
– Put the mounting frame on a clean surface.
– Remove counterbalance securing bolts.
– Remove counterbalance and counterbalance shaft gear.
– Turn the counterbalance shaft so that it can be removed from
the bearing.
3.1.2
Installing
– Sliding surfaces of the bearing oil.
– Set counterbalance shaft in bearing.
– Fit the gear and counterbalance on counterbalance shaft.
Note
Installing the gear and counterbalance is only possible in a single
position.
– Hand tighten securing bolt for counterbalance weight and
gear.
– Tighten mounting frame to engine block by hand so that there
is no play.
Fox 2004 ➤
3 - Cyl. diesel engine - Edition 02.2009
26
Rep. Gr.13 - Crankshaft, pistons