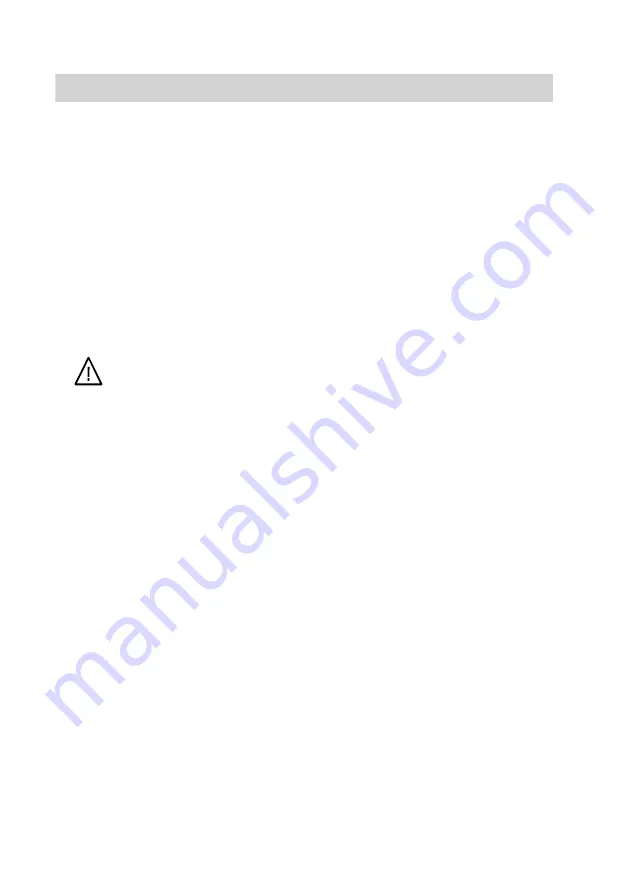
26
3.
If required, retighten the flue gas col-
lector seal
A
at the tensioning tog-
gles
E
or replace. Replace lip seal
D
in case it leaks.
Note
Prior to removing the flue gas collec-
tor, pull the plug at flue gas tempera-
ture sensor
F
.
4.
Check the fittings on the water side
for leaks and replace the seals/gas-
kets if required.
Danger
There is a risk of injury when
working on pressurised com-
ponents.
Only open the connections on
the heating water side after
the boiler has been de-pres-
surised.
Only drain the boiler with a
suction pump when the boiler
air vent valve is open.
5.
Check the boiler thermal insulation
for good fit and correct if required or
replace if it is damaged.
Checking the diaphragm expansion vessel and system pressure
Note
Carry out this test on a cold system.
1.
Drain the system or close the cap
valve at the diaphragm expansion
vessel to depressurise the system
until the pressure gauge indicates
"0".
2.
If the pre-charge pressure of the dia-
phragm expansion vessel is lower
than the static system pressure, top
up with nitrogen until the pre-charge
pressure is raised by 0.1 to 0.2 bar.
3.
Top up your heating system with
water until the filling pressure of a
cooled system is 0.1 to 0.2 bar higher
than the pre-charge pressure of the
diaphragm expansion vessel.
Permiss. operating pressure: 3 bar
Min. operating pressure: 1 bar
Commissioning, inspection, maintenance
Further details regarding the individual steps
(cont.)
5692 860 GB
Summary of Contents for CU3A
Page 147: ...147 5692 860 GB ...