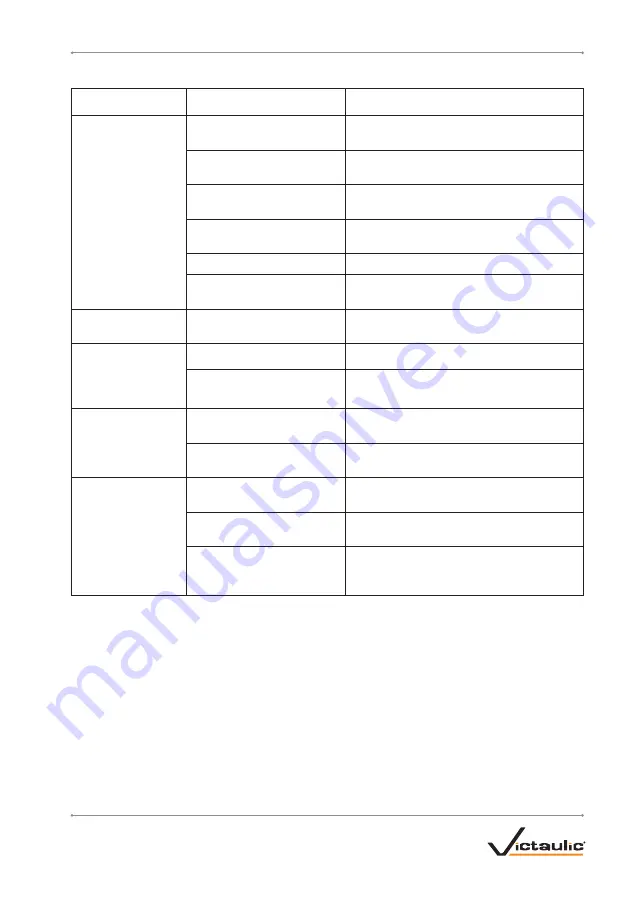
PROBLEM
POSSIBLE CAUSE
SOLUTION
Pipe flare is excessive.
Pipe support is adjusted too high for
long pipe.
Refer to the “Grooving Long Pipe Lengths” section.
Tool is tilted forward (out of level) while
grooving long pipe.
Refer to the applicable “Tool Setup” section.
Incorrect pipe support positioning of long
pipe. Pipe is “over-tracking.”
Move the pipe support to the right. Refer to the “Grooving Long
Pipe Lengths” section.
Pipe stabilizer is adjusted too far inward.
Back off the pipe stabilizer to the furthest point where it still
stabilizes the pipe effectively.
Ram speed is not set correctly.
Refer to the “Ram Speed Control Valve Adjustment” section.
Excessive ram pressure.
Reduce ram pressure by turning the selector valve on the front of
the tool to the
“BLACK”
setting.
Larger diameter pipe sways or
vibrates from side to side.
Incorrect pipe stabilizer adjustment.
Move the pipe stabilizer in or out until the pipe rotates smoothly.
The tool will not groove the
pipe, or the tool comes up to
operating pressure excessively
slowly.
Air is present in the hydraulic system.
Refer to the “Air Bleeding” section.
Pipe is beyond the wall thickness or pipe
yield strength capacity of the tool.
Refer to the applicable “Tool Rating and Roll Selection” section.
Pipe groove diameters do not
meet Victaulic specifications.
Groove diameter stop is not adjusted
properly.
Refer to the “Groove Diameter Stop Adjustment” section.
Pipe is beyond the wall thickness or pipe
yield strength capacity of the tool.
Refer to the applicable “Tool Rating and Roll Selection” section.
The “A” Gasket Seat or “B”
Groove Width dimensions
do not meet Victaulic
specifications.
Upper roll bearing is not lubricated
adequately.
Refer to the “Maintenance” section.
Incorrect upper roll, lower roll, or both
installed on the tool
Install the correct rolls. Refer to the applicable “Tool Rating and Roll
Selection” section.
Pipe not inserted fully onto the lower roll,
or pipe is not tracking properly.
Make sure pipe is against the lower-roll backstop flange. Refer to
the “Grooving Long Pipe Lengths” section for proper pipe stand
positioning.
In the event of tool malfunction outside the scope of the troubleshooting section, contact Victaulic for
assistance.
TROUBLESHOOTING (CONTINUED)
TM-VE268_47
REV_H
TM-VE268
/ Operating and Maintenance Instructions Manual
Summary of Contents for VE268
Page 2: ......