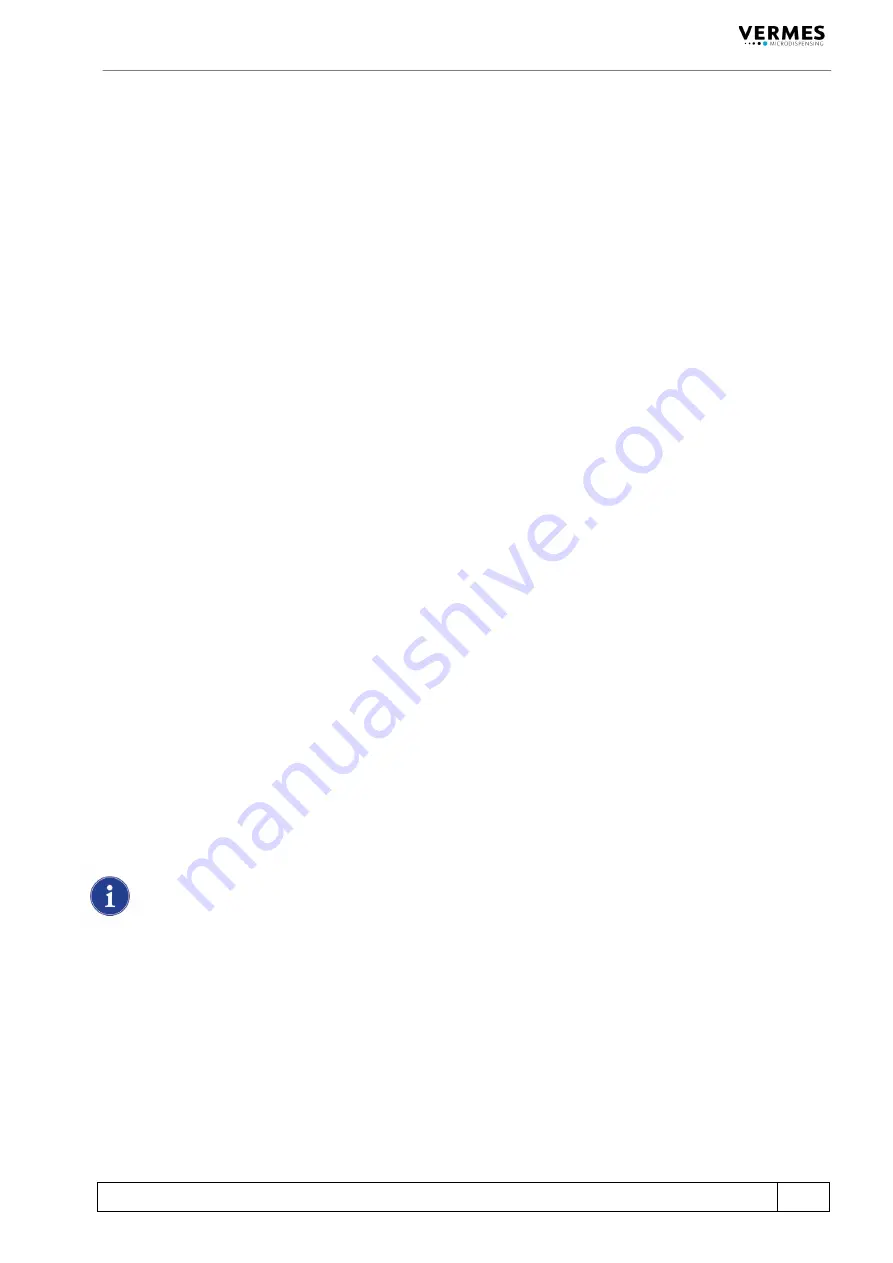
VTK-VS-BA-015e-A | User Manual MDS 3200+ Series
|
Communication Interfaces
81
Step 5:
In order to confirm step 4, a short trigger signal
(500μs
– 80 ms)
must be sent to the control
unit via PLC interface
(see Step 3)
.
Step 6:
The system sends 500 shots to clear the valve for the adjust. The message “500 Shots Please
Wait” is shown.
Step 7:
The system then returns the current adjust value, continuously repeating the transmission
to the PC in intervals of 500 ms
(via RS-232C)
.
An additional command to update the adjust value on the screen is not required.
Step 8:
Rotate the nozzle unit clockwise towards the fluid box, until the value displayed on the PC is
in the tolerance range
(between 1020 and 1039)
.
Step 9:
Confirm the indicated value
(e.g. 1035)
by sending a short trigger signal via PLC-interface, as
described above. The system returns the current adjust value and either:
1
(value too low)
2
(value ok)
3
(value too high)
Step 10:
In order to confirm step 7, a short trigger signal
(500μs
– 80 ms)
must be sent to the control
unit via PLC interface
(see Step 3)
. This will only be accepted, if the value is okay. After the
confirmation the system then returns the following response via RS-232C:
“MNL Calibration Please Wait“
This is only the case though, if your system is in F-mode. In A-mode
(i.e. with an A-valve or
an F-valve in reduced mode, see part 4.1.5.7)
the remote adjust ends here.
Step 11:
The system starts the MNL calibration.
During this process the following messages can appear on the screen:
IN
(You have to turn the MNL screw further in, clockwise.)
OUT
(You have to turn out the MNL screw, counter-clockwise.)
OK
(The MNL screw in the correct range. Please wait.)
Once the calibration measurements have been successfully done, the following three mes-
sages appear:
“Calibration OK”
“Ready”
“Adjust LED Green“
The adjust has been completed successfully and the green LED is lit.
INFORMATION!
Beyond the tolerance range
(1020–1039)
it is impossible to confirm the values.
Outside the adjust range, the adjust can only be interrupted by sending a long trigger signal
(100 ms – 200 ms)
to the control unit via PLC- interface. The system returns the message
“adjust failed“ to the PC.
Long Trigger signal:
5 V or 24 V
(PIN2 + PIN4 or PIN3 + PIN4 Input signal of MDC via 15 pin Sub-D)
Signal length: 100 ms – 200 ms