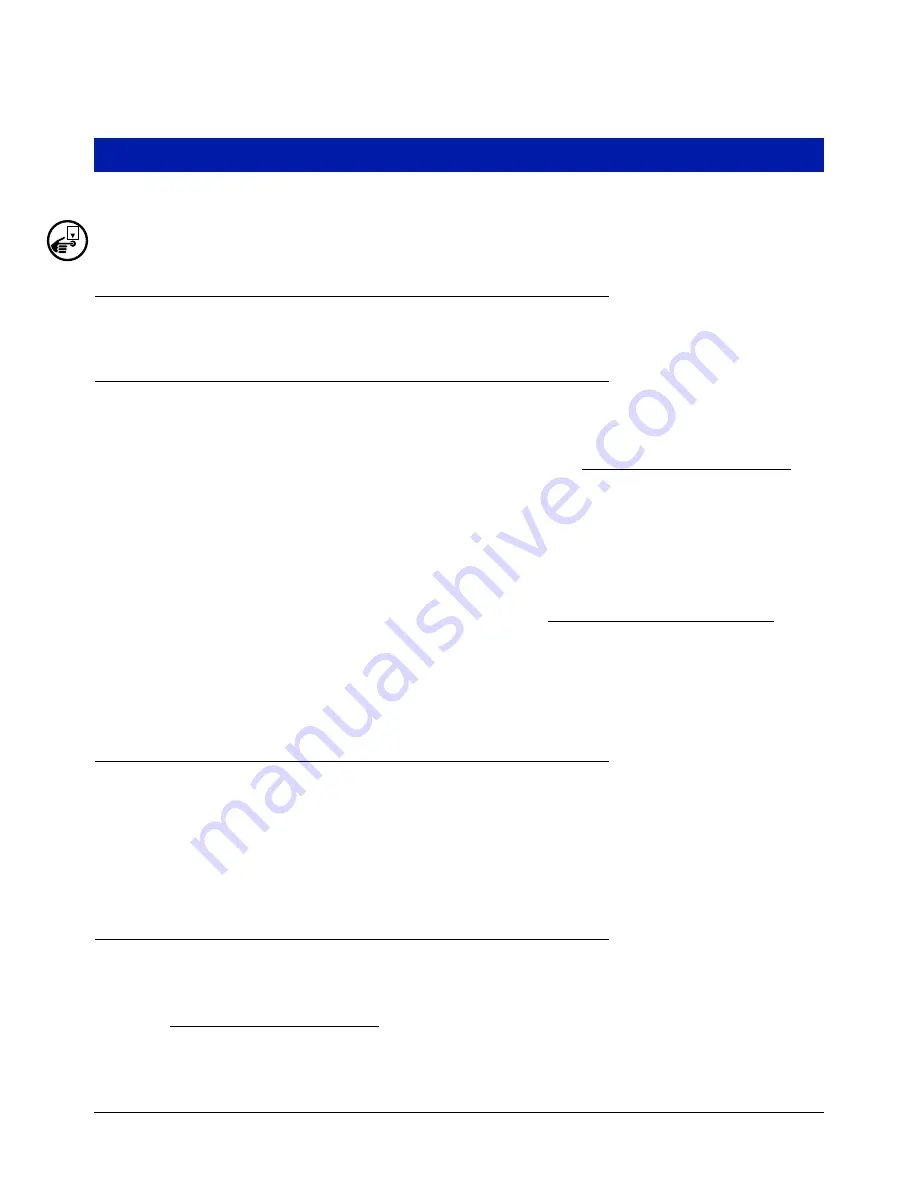
10-1
10 Sensor Troubleshooting
This section contains suggested corrective actions for troubleshooting sensor problems.
Turn off, tag, and lockout power to the console before opening display door assembly!
Sensor Alarm Will Not Clear
Liquid or fuel in containment area.
Sensor Out Alarms
Follow these steps in sequence to troubleshoot Sensor Out alarms.
1. Verify that the distance from the sensor to the TLS is less than 1000 feet.
2. Verify that the sensor wiring conforms to the requirements detailed in the Site Prep and Installation Manual
(P/N 577014-073) and that it connects the console to the sensor.
3. Verify that the console grounding is correct. Make sure there are two grounds and that one is at least a 12
AWG (or larger diameter) conductor. Check that the grounding conductors are properly connected to a good
ground source. Measure the resistance to ground, it should be less than one ohm.
4. Verify that the console is on a separate circuit breaker with no shared branch circuits.
5. Verify that the sensor connects to the proper connector position and that polarity (required for some sensors) is
maintained from the sensor to the console. If necessary, refer to the Sensor Products Application Guide (P/N
577013-750) for correct sensor/console compatibility and sensor specifications.
6. View the diagnostic screen for the problem sensor and search for information that may help you determine the
root cause of the sensor’s problem.
7. Consider directly connecting the sensor to the console to confirm a faulty sensor.
Setup Data Warning
This alarm could be posted by one of three setup errors:
1. A label for the sensor was not entered during setup.
2. The wrong sensor type was selected during setup.
3. The sensor was not configured during setup but the console measures a resistive value and determines a
device is connected.
Unstable Sensor Readings
Unstable sensor readings may be the result of intermittent signals or electro-magnetic interference (EMI). Some
causes of unstable sensor readings are discussed below.
1. Shielded cable was not used between the sensor and the console, or if it was, it was not grounded correctly.
See the Site Prep and Installation Manual
(P/N 577014-073) for installation requirements.
2. Extra wires (not connected to the console) in the sensor conduit. They should be removed.
OFF