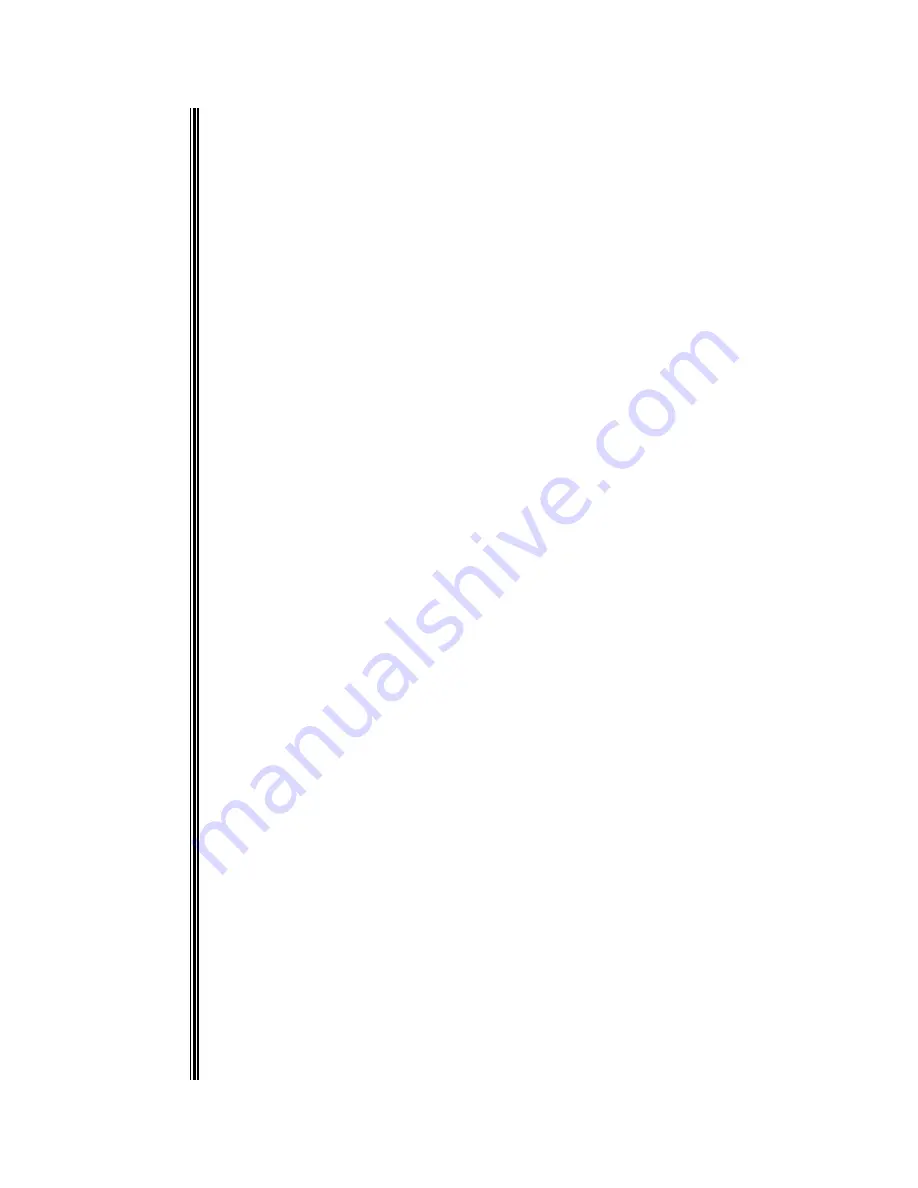
Calibration (Cal)
Pressing the CAL momentary switch activates the Calibration function.
The Calibration function of the leak detector is available only after the
Cal-Check procedure has been completed. After the Cal-Check cycle is
completed, when the actual leak rate measured by the unit is close to, but
not exactly the same as the internal leak rate standard, the Calibration
function may be used. Since the Calibration function adjusts the amplifier
gain, once initiated, the leak check of the Cal-Check function will now
conform to the internal leak rate standard. Note that consistent differences
greater than 15% may indicate an improperly tuned mass spectrometer or
a fault within the unit.
Tune
Pressing the TUNE momentary switch initiates an automatic tuning cycle.
During the tuning cycle, voltages applied to the mass spectrometer are
adjusted and optimized for peak sensitivity and performance. It is
recommended that the Tune function be used in conjunction with the Cal-
Check function. Since the Calibration function basically increases or
decreases the measurement gain of the unit, without the optimization of
the Tune function, the unit eventually may not be able to self-calibrate.
Vacuum Instrument Corp.
2099 Ninth Avenue
Ronkonkoma, NY 11779
631.737.0900
1109-186-00 Rev. C
2-35
Summary of Contents for MS40
Page 1: ......
Page 5: ...Figure 1 1 VIC Model MS 40 Portable Automatic Leak Detector 1109 186 00 Rev C 1 2...
Page 9: ...6 3 4 2 5 7 1 9 8 FIGURE 1 2 INTERNAL ROTARY VANE MECHANICAL PUMP 1109 186 00 Rev C 1 6...
Page 17: ......
Page 19: ...FIGURE 2 1 MS 40 USER PANEL 1109 186 00 Rev C 2 2...
Page 32: ...FIGURE 2 2 MS 40 REAR PANEL CONNECTIONS 1109 186 00 Rev C 2 15...
Page 35: ...Figure 2 3 MS 40 Hand Held Remote Control 1109 186 00 Rev C 2 18...
Page 45: ...1109 186 00 Rev C 2 28...
Page 53: ......
Page 60: ...1109 186 00 Rev C 3 7...
Page 69: ......
Page 85: ...1109 186 00 Rev C 4 16...
Page 98: ...1109 186 00 Rev C 4 29...
Page 103: ...1109 186 00 Rev C 4 34...
Page 104: ...1109 186 00 Rev C 4 35...
Page 105: ...1109 186 00 Rev C 4 36...
Page 106: ...1109 186 00 Rev C 4 37...
Page 107: ...1109 186 00 Rev C 4 38...
Page 108: ......
Page 112: ...1109 186 00 Rev C 5 4...
Page 115: ...1109 186 00 Rev C 5 7...
Page 118: ......
Page 122: ......
Page 136: ...1109 186 00 Rev C b ii...
Page 137: ...1109 186 00 Rev C b iii...
Page 138: ......
Page 160: ......
Page 162: ......
Page 164: ...1109 186 00 Rev C f ii...
Page 165: ...1109 186 00 Rev C f iii...
Page 167: ...1109 186 00 Rev C f v...
Page 168: ...1109 186 00 Rev C f vi...
Page 169: ...1109 186 00 Rev C f vii...