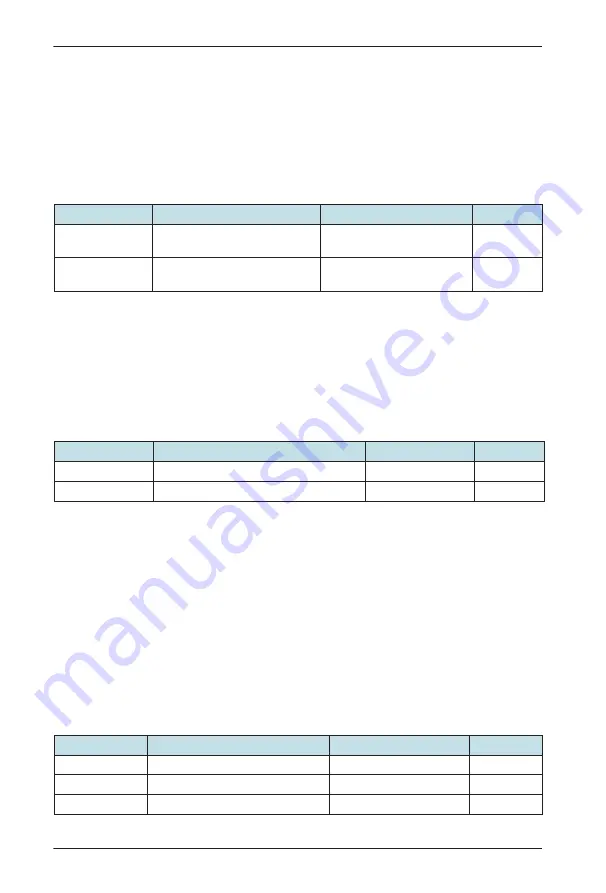
Description
of
Function
Codes
VDF650
User
Manual
-
224
-
PROFIBUS
-
DP
,
CANopen
and
CANlink
.
They
cannot
be
used
simultaneously
.
If the communication mode is used
,
a communication card must be installed
.
The
VDF650 provides four optional communication cards and you can select one based
on actual requirements
.
If the communication protocol is Modbus
,
PROFIBUS
-
DP
or CANopen
,
the corresponding
serial communication
protocol needs to be selected
based
on
the
setting
of
P0
-
28
.
The
CANlink
protocol
is
always
valid
.
Function
Code
Parameter
Name
Setting
Range
Default
A0
-
05
Forward
maximum
frequency
in
torque
control
0
.
00
Hz
to
maximum
frequency
(
P0
-
10
)
50
.
00
Hz
A0
-
06
Reverse
maximum
frequency
in
torque
control
0
.
00
Hz
to
maximum
frequency
(
P0
-
10
)
50
.
00
Hz
two
parameters are
used to set
the
maximum frequency
in
forward
or
reverse
rotation in
torque
control
mode
.
In torque control
,
if the load torque is smaller than the motor output torque
,
the motor
'
s
rotational speed will rise continuously
.
To avoid runaway of the mechanical system
,
the
motor
maximum
rotating
speed
must
be
limited
in
torque
control
.
You can implement continuous change of the maximum frequency in torque control
dynamically
by
controlling
the
frequency
upper
limit
.
Function
Code
Parameter
Name
Setting
Range
Default
A0
-
07
Acceleration
time
in
torque
control
0
.
00
–
65000s
0
.
00s
A0
-
08
Deceleration
time
in
torque
control
0
.
00
–
65000s
0
.
00s
In torque control
,
the difference between the motor output torque and the load torque
determines
the
speed
change
rate
of
the
motor
and
load
.
The
motor
rotational
speed
may
change quickly and this will
result
in noise
or too large mechanical stress
.
The setting
of
acceleration
/
deceleration time
in torque
control
makes the motor rotational
speed
change
softly
.
However
,
in
applications
requiring
rapid
torque
response
,
set
the
acceleration
/
deceleration
time
in
torque
control
to
0
.
00s
.
For
example
,
two
AC
drives
are
connected
to
drive
the
same
load
.
To balance
the
load
allocation
,
set
one AC
drive
as
master
in speed
control and the
other
as
slave
in
torque
control
.
The
slave
receives
the
master
'
s
output
torque
as
the
torque
command and must follow the master rapidly
.
In this case
,
the acceleration
/
deceleration
time
of
the
slave
in
torque
control
is
set
to
0
.
0s
.
Group
A1
:
Virtual
DI
(
VDI
)/
Virtual
DO
(
VDO
)
Function
Code
Parameter
Name
Setting
Range
Default
A1
-
00
VDI1
function
selection
0
–
59
0
A1
-
01
VDI2
function
selection
0
–
59
0
A1
-
02
VDI3
function
selection
0
–
59
0
Summary of Contents for VDF650 Series
Page 1: ...VDF650 Series High Performance AC Drive...
Page 9: ......
Page 10: ...1 Safety Information and Precautions...
Page 17: ...Safety Information and Precautions VDF650 User Manual 16...
Page 18: ...2 Product Information...
Page 29: ...Product Information VDF650 User Manual 28...
Page 30: ...3 Mechanical and Electrical Installation...
Page 46: ...4 Operation Display and Application Examples...
Page 79: ...Operation Display and Application Examples VDF650 User Manual 78...
Page 80: ...5 Function Code Table...
Page 136: ...6 Description of Function Codes...
Page 248: ...7 EMC...
Page 260: ...8 Selection and Dimensions...
Page 285: ...Selection and Dimensions VDF650 User Manual 284...
Page 286: ...9 Maintenance and Troubleshooting...