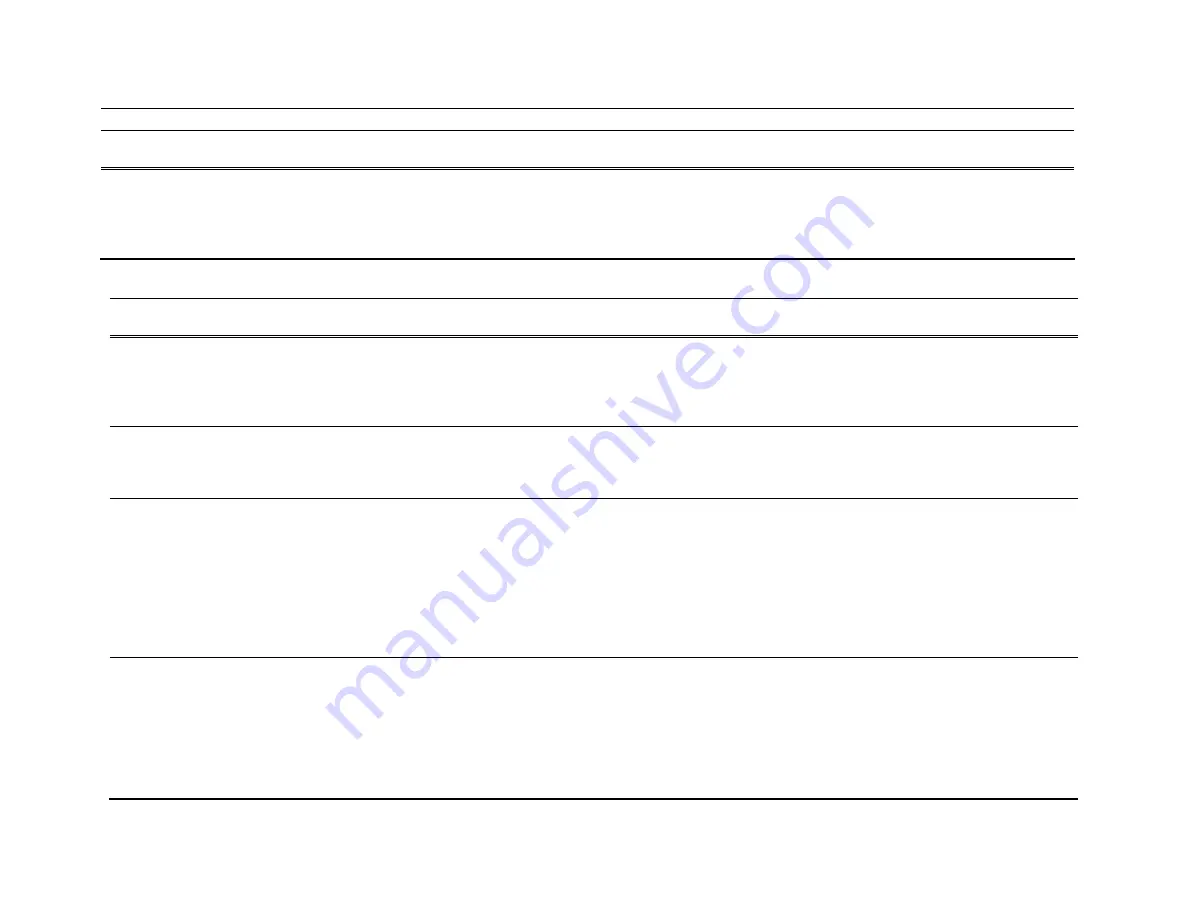
T
ec
hn
ic
al
S
ec
tio
n
1
7
SET POINTS MENU
(continued)
MENU ITEM
SOFTWARE
NAME
ITEM DESCRIPTION
ITEM RANGE
DEFAULT
VALUE
END
OF
MENU
The
END OF MENU
item informs you that the end of a menu
has been reached. You can either scroll back up the menu to
make changes, or press the
SELECT
or
MENU
key to exit out of
the menu.
ALARM MENU
MENU ITEM
SOFTWARE
NAME ITEM
DESCRIPTION
ITEM RANGE
DEFAULT
VALUE
LOW PRESSURE
ALARM
LOW ALARM
The
LOW ALARM
item sets the low pressure alarm set point. A
low alarm condition is defined as when the room pressure falls
below or goes in the opposite direction of the
LOW ALARM
set
point.
OFF
0 to -0.18500 in. H
2
O
0 to +0.18500 in. H
2
O
OFF
HIGH PRESSURE
ALARM
HIGH
ALARM
The
HIGH ALARM
item sets the high pressure alarm set point. A
high alarm condition is defined as when the room pressure rises
above the
HIGH ALARM
set point.
OFF
0 to -0.18500 in. H
2
O
0 to +0.18500 in. H
2
O
OFF
REMOTE OR
ALTERNATE
LOW PRESSURE
ALARM
REM LOW
ALM
The
REM LOW ALM
item sets a remote or second low pressure
alarm set point. A remote low alarm condition is defined as when
the room pressure falls below or goes in the opposite direction of
the
REM
LOW ALM
set point.
This item is enabled when the REMOTE SWT contact closure,
pins 3 and 4, is closed, or the RS 485 communications sends a
command.
OFF
0 to -0.18500 in. H
2
O
0 to +0.18500 in. H
2
O
OFF
REMOTE OR
ALTERNATE
HIGH PRESSURE
ALARM
REM HIGH
ALM
The
REM HIGH ALM
item sets a remote or second high-pressure
alarm set point. A high alarm condition is defined as when the
room pressure rises above the
REM HIGH ALM
set point.
This item is enabled when the REMOTE SWT contact closure,
pins 3 and 4, is closed, or the RS 485 communications sends a
command.
OFF
0 to -0.18500 in. H
2
O
0 to +0.18500 in. H
2
O
OFF