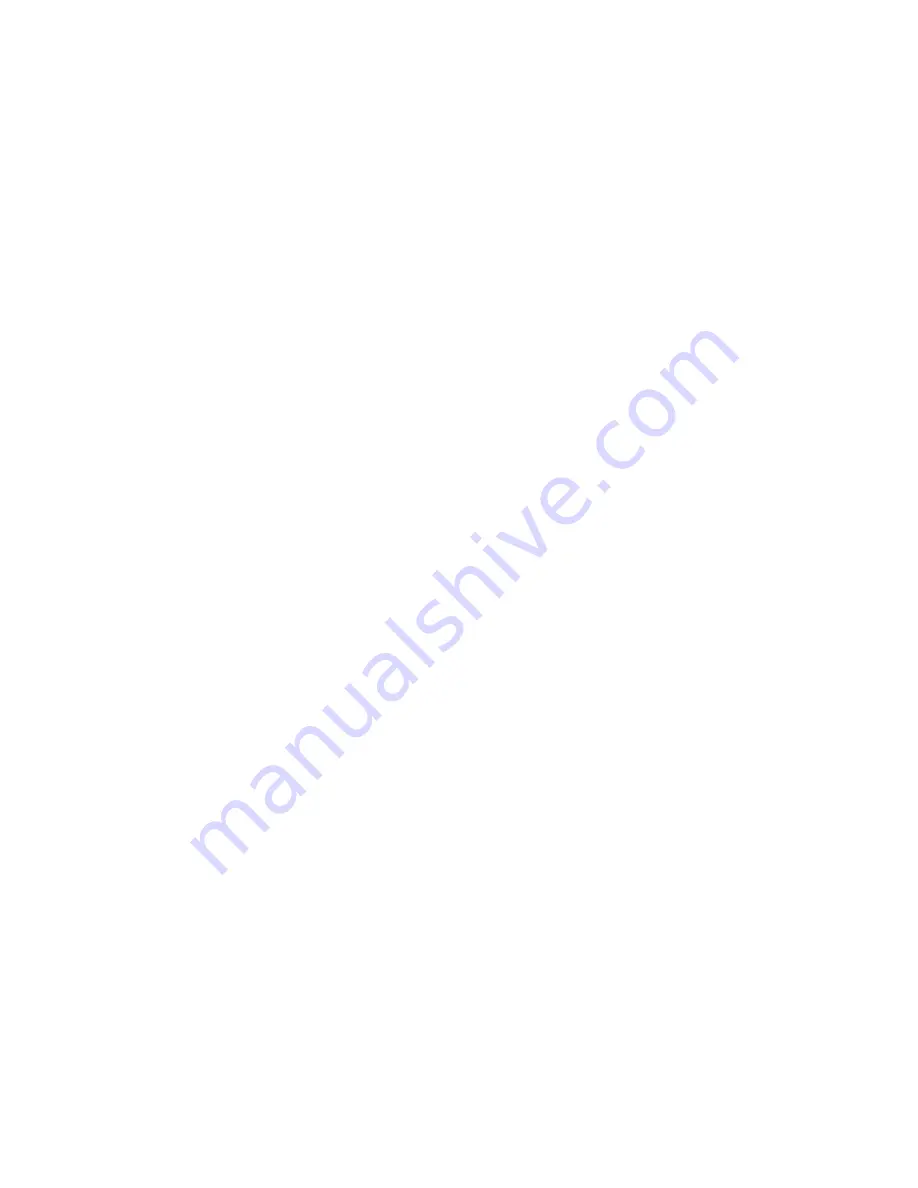
4
(2) Absorption
In the case of ABDA machines, a burner provides heat
energy input while the ABTF is a regulated supply of 115-
psig steam or 350°F hot water supplied to the high
temperature generator. In both cases refrigerant water
vapor is separated from the dilute lithium bromide solution
when it is boiled. The hot refrigerant vapor produced by the
high temperature generator is directed to the low
temperature generator tubes to further heat and boils the
lithium bromide and produce additional water vapor. This
vapor leaves the low temperature generator as condensed
refrigerant water that is piped to the condenser section. The
refrigerant vapor separated from the lithium bromide in the
low temperature generator passes to the condenser as
vapor where it also condenses. The entire condensed
refrigerant is then returned to the evaporator to replace the
refrigerant used by the evaporator. Using the refrigerant
vapor, that is produced in the high temperature generator
to produce additional refrigerant in the second stage
generator, provides the two-stage effect.
The lithium bromide cycle is reverse parallel. All the diluted
lithium bromide from the absorber is pumped through the
low temperature heat exchanger and then to the low
temperature generator where the lithium bromide is
partially concentrated.
When the partially concentrated lithium bromide solution
leaves the low temperature generator, part of the flow is
diverted to the high temperature solution pump, which
pumps the lithium bromide into the high temperature
solution and condensate heat exchangers, and then to the
high temperature generator. The lithium bromide that is not
diverted exits the low temperature generator and is mixed
with concentrated lithium bromide returning from the high
temperature generator, by way of the high temperature
heat exchanger and float valve. The resulting intermediate
lithium bromide solution passes through the low
temperature heat exchanger to the absorber spray solution
pump, for distribution over the absorber tubes completing
the lithium bromide cycle.
When the intermediate lithium bromide solution is sprayed
onto the absorber tubes, the solution is cooled from the
cooling tower water flowing through the tubes. The low
partial pressure created by this activity allows the lithium
bromide to absorb the refrigerant water vapor produced by
the evaporator section. The resulting dilute lithium bromide
solution falls to the bottom of the absorber, where it is
again pumped through the low temperature, high
temperature and condensate heat exchangers, before
entering the generators for refrigerant reclaim and
subsequent lithium bromide reconcentration.
The refrigerant pump circulates refrigerant that is stored in
the evaporator pan; to constantly wet the evaporator tubes.
As the refrigerant contacts the tubes containing warm
system water flowing through the evaporator tubes, the
refrigerant vaporizes, removing heat from the system
water. The resulting vapor is absorbed by the lithium
bromide in the absorber, to sustain the cooling process.
The fluid temperatures and lithium bromide concentrations
are illustrated in Figures 1 (Model ABTF) and 2 (Model
ABDA) and Tables 1 and 2, and are described in the
following text, are valid when the machine is operating at
the nominal design conditions of 44°F leaving evaporator,
85°F entering cooling water and 115 psig steam, or at
design burner input rate. The fluid temperatures and
concentrations will change if the cooling water drops below
design conditions, or the energy input are reduced for part
load operation. This machine is designed to operate
efficiently with an entering condenser water temperature of
95 to 54°F.