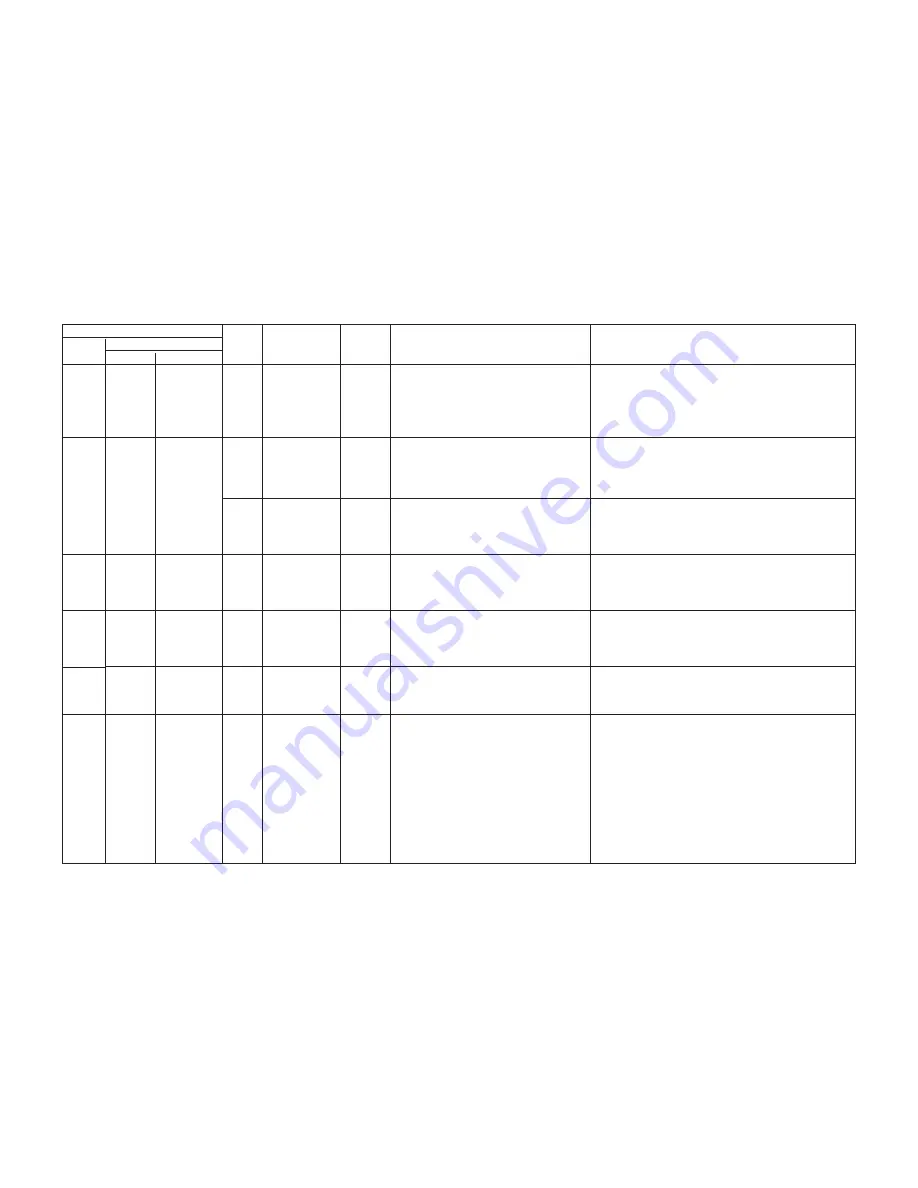
82
Check code
Wired
remote
controller
P13
P15
P17
P18
P19
P20
Outdoor 7-segment display
Check code
Auxiliary code
P13
—
P15
01: TS condition
02: TD condition
P17
—
P18
—
P19
Detected outdoor
unit No.
P20
—
Detected
position
I/F
I/F
I/F
I/F
I/F
I/F
I/F
Check code name
Outdoor liquid back
detection error
Gas leak detection
(TS1 condition)
Gas leak detection
(TD condition)
Discharge temp
TD2 error
Discharge temp.
TD3 error
4-way valve
operation error
High-pressure
protective operation
Status
All stop
All stop
All stop
All stop
All stop
All stop
All stop
Error detection condition
<In cooling>
While the system operated in cooling mode, high ststus
of high pressure value was detected in the stopped
follower unit.
<In heating>
While the system is operating in HEAT mode, outdoor
PMV of which opening degree was 100 pulse or less for
a certain time.
Protective stop which generates when the status that
suction temperature is over the judgment standard
temperature continued for 10 minutes was repeated for 4
times or more.
<TS error judgment standard temperature>
In cooling operation: 60°C or higher
In heating operation: 40°C or higher
Protective stop which generates when the status that
while compressor is under low frequency operation, the
discharge temperature TD1, TD2 or TD3 detected 108°C
or more continuously for 10 minutes was repeated for 4
times or more.
Protective stop which generates when the discharge
temperature (TD2) was over 115°C was repeated for 4
times or more.
Discharge temp. (TD3) exceeded 115°C.
When abnormal refrigerating cycle data was detected in
heating
Pd sensor detected 3.6MPa or more.
Check item (position)
• Check full close operation of outdoor PMV (1, 2, 4).
• Check Pd and Ps sensor error.
• Check clogging of SV2 circuit.
• Check clogging of balance pipe.
• Check clogging of SV3B circuit.
• Check outdoor P.C. board (I/F) error.
• Check capillary clogging of oil return circuit from oil separator.
• Check leakage of stop valve in discharge assembly part.
• Check refrigerant shortage.
• Check full open of outdoor service valves (gas side, liquid side).
• Check outdoor PMV clogging (PMV1, 2).
• Check characteristics of TS1 sensor resistance value.
• Check 4-way valve error.
• Check leakage of SV4 circuit.
• Check refrigerant shortage.
• Check outdoor PMV clogging (PMV1, 2).
• Check characteristics of TD1, TD2 sensor resistance value.
• Check indoor air filter clogging.
• Check pipe clogging.
• Check SV4 circuit (Valve leakage, misinstallation)
• Check full opening of outdoor service valves (gas side, liquid side).
• Check clogging of outdoor PMV (PMV1, 2, 4).
• Check characteristics of TD2 sensor resistance value.
• Check 4-way valve error.
• Check leakage of SV4 circuit.
• Check SV4 circuit. (Miscabling and misinstallation of SV41, SV42 and SV43)
• Check full opening of outdoor service valve (gas side, liquid side).
• Check clogging of outdoor PMV (PMV1, 2, 4)
• Check characteristics of TD3 sensor resistance value.
• Check 4-way valve error.
• Check leakage of SV4 circuit.
• Check SV4 circuit (Miswiring and mismounting of SV41, SV42, and SV43).
• Error of 4-way valve error.
• Check coil error and connector connection of 4-way valve.
• Check characteristics of TS1/TE1 sensor resistance value.
• Check characteristics of Pd, Ps pressure sensor output voltage.
• Check misconnection of TE1 and TL sensors.
• Check Pd pressure sensor error.
• Check full opening of service valves (Gas side, Liquid side).
• Check outdoor fan error.
• Check outdoor fan motor error.
• Check clogging of outdoor PMV. (PMV1,2, 4)
• Check clogging of indoor/outdoor heat exchangers.
• Check air short-circuiting in outdoor unit.
• Check clogging of SV2 circuit.
• Check outdoor P.C. board (I/F) error.
• Check indoor fan system error. (Cause of air volume decrease)
• Check valve opening of indoor PMV.
• Check miscabling of communication line between indoor and outdoor.
• Check operation error of stop valve in discharge assembly part.
• Check circuit of gas balance SV4 valve.
• Check circuit of SV5 valve.
• Check refrigerant overcharge.