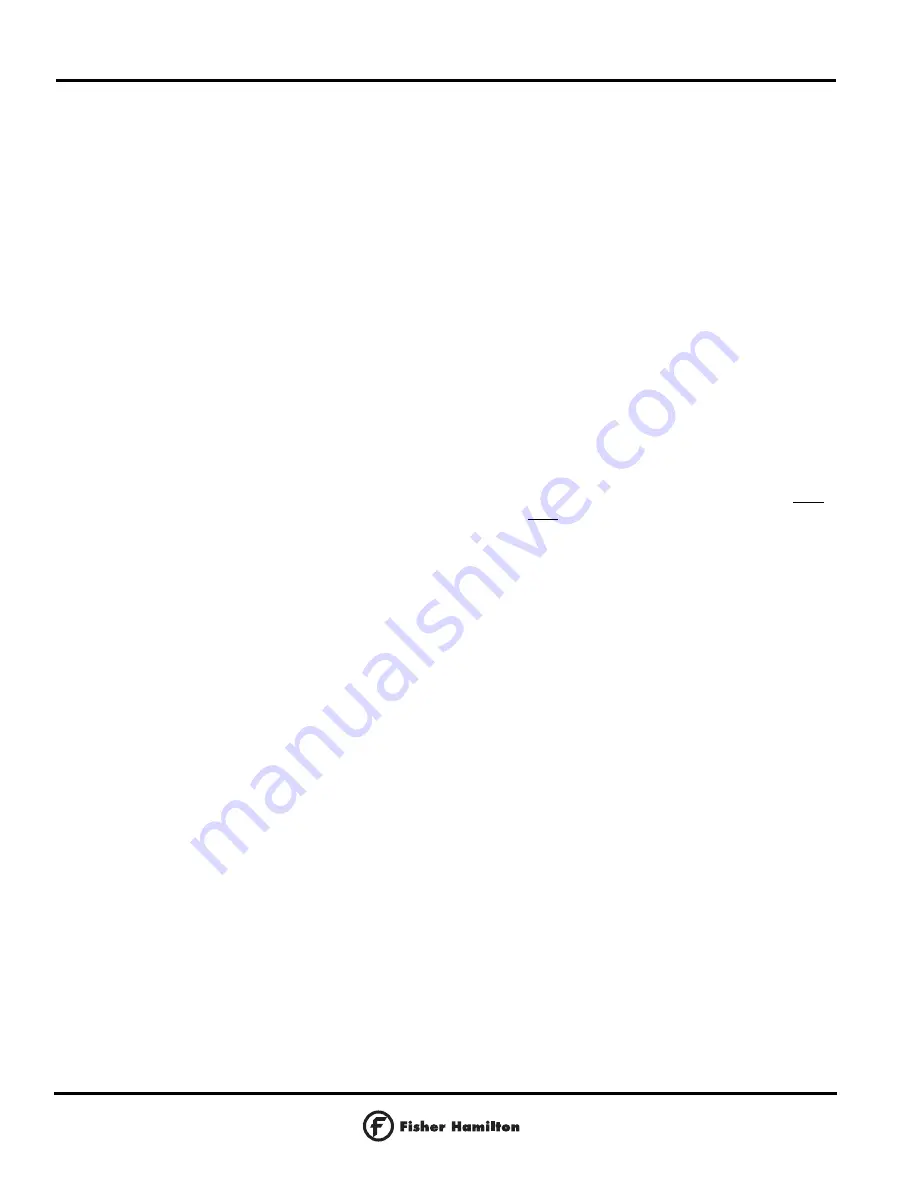
MAX/Wall
®
Technical Wall System
4
Section 1 – Introduction
Tools Required:
3/8" Drive socket set, including the following:
Extension (2" or 3")
Universal joint
Hex bits (4" long min.) - 3/16", 5/16".
Combination wrenches - 3/8", 3/16", 1/2", 9/16".
Phillips screwdrivers - (#2 and #3 tips)
1/2" drill motor (Hammer drill preferable)
1/2" masonry drill bit
Torque wrench
Rubber mallet
Jigsaw with metal cutting blade
Chalk line
Carpenter’s level (4' min.)
Facing insert removal tool
Flat blade screwdriver
Hammer
Knife
Measuring tape
Optional Tools to speed installation:
Drill motor or cordless drill including: set of drill bits
(specifically #12 or 3/16")
1/2" hex shank (2-1/2" long)
2 C-clamps (4" min. throat depth)
Masking tape
This manual is intended as a procedural tool for the
installation and assembly of Fisher Hamilton furni-
ture. It also serves as an aid to designers and plan-
ners during layout and cost analysis, and to facility
managers to carry out periodic modifications.
Disclaimer and Warning:
Fisher Hamilton disclaims liability for installations
(including re-arrangements and additions) not in
strict conformity with the instructions contained here-
in or with other written instruction of Fisher Hamilton.
Fisher Hamilton further disclaims liability if its
products are modified, altered, abused or misused.
1.1 Preparation for Installation
1. Select a staging area as close to the installation
as possible. If more than one floor is involved,
provide a staging area for each floor.
2. Check actual floor dimensions against the layout
print for possible un-planned obstructions. These
could include walls, columns, service entrances,
or changes in floor elevation such as slopes or
steps.
3. Mark the proposed layout on the floor with mask-
ing or a chalk line. Find and mark the high spot on
the floor by sliding a four foot carpenter’s level
across the floor.
4. Start the installation of each run at a corner near-
est the high point and adjust the leveler out 1-1/4"
at that point. Caution: Support structures must be
1-1/4" minimum off the floor to provide adequate
clearance for power cables and installation of
supported structural table.
Caution: Support structures must be 1-1/4" mini-
mum off the floor to provide adequate clearance
for power cables and installation of supported
structural table.
5. If possible, start the installation at the farthest
point from the staging area to avoid hauling prod-
ucts through areas already installed.
6. Installation sequence:
a. Assemble the panels and cores per to floor
plan,
making sure adequate support is provided to
stabilize the configuration.
If structural tables are to be installed, they
should, whenever possible, be attached to
individual panels before assembling panels into
runs.
b. Install the appropriate wiring, and plumbing.
c. Attach the base covers and facing inserts.
d. Install cantilevered work surfaces, upper and
lower storage, and other accessories.
e. Move primary tables and any other free-
standing furniture into place.
7. To avoid soiling the fabric on fabric covered
facing inserts, handling them with white cotton
gloves is recommended.
8. When installation of the Max Furniture System is
complete, extra hardware and components may
have accumulated. It is recommended that all
”extra parts” be saved for future additions or re-
arrangements to the system.
Summary of Contents for FISHER HAMILTON MAX/WALL
Page 1: ......
Page 58: ...MAX Wall Technical Wall System 58...