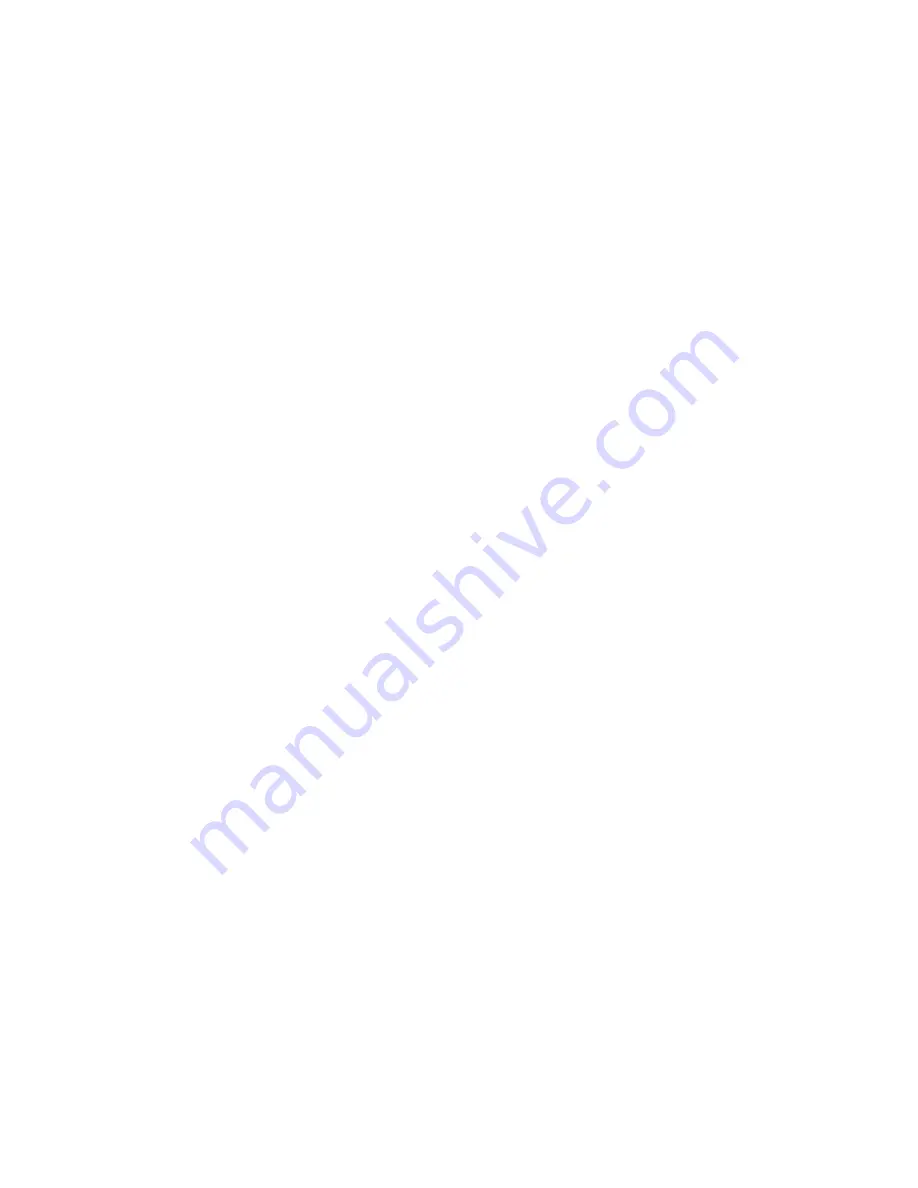
FCC COMPLIANCE STATEMENT
FOR AMERICAN USERS
This equipment has been tested and found to comply with the limits for a CLASS A digital device,
pursuant to Part 15 of the FCC Rules. These limits are designed to provide reasonable protection
against harmful interference when the equipment is operated in a commercial environment. This
equipment generates, uses, and can radiate radio frequency energy and, if not installed and used in
accordance with the instructions, may cause harmful interference to radio communications. Operation
of this equipment in a residential area is likely to cause harmful interference in which case the user
will be required to correct the interference at his expense.
EMS AND EMI COMPLIANCE STATEMENT
FOR EUROPEAN USERS
This equipment has been tested and passed with the requirements relating to electromagnetic
compatibility based on the standards EN50081-1 (EN55022 CLASS A) and EN61000-4-2/-3/-4/-5/-6/
-8/-11 (IEC Teil 2,3,4). The equipment also tested and passed in accordance with the European
Standard EN55022 for both the Radiated and Conducted emissions limits.
CAUTION
Danger of explosion if battery is replaced incorrectly.
Only replace battery with an equivalent type as recommended by the manufacturer.
Dispose of used batteries according to the manufacturer’s instructions.
Copyright and Trademark Notice
© 2005 by Tharo Systems, Inc.
It is illegal to photocopy or electronically transmit a facsimile of this manual or any portion
of its contents for any means or purpose without the publisher’s permission. Fines of up
to $10,000.00 may be imposed for violation.
All brand or product names are trademarks or registered trademarks of their respective companies.
- 1 -