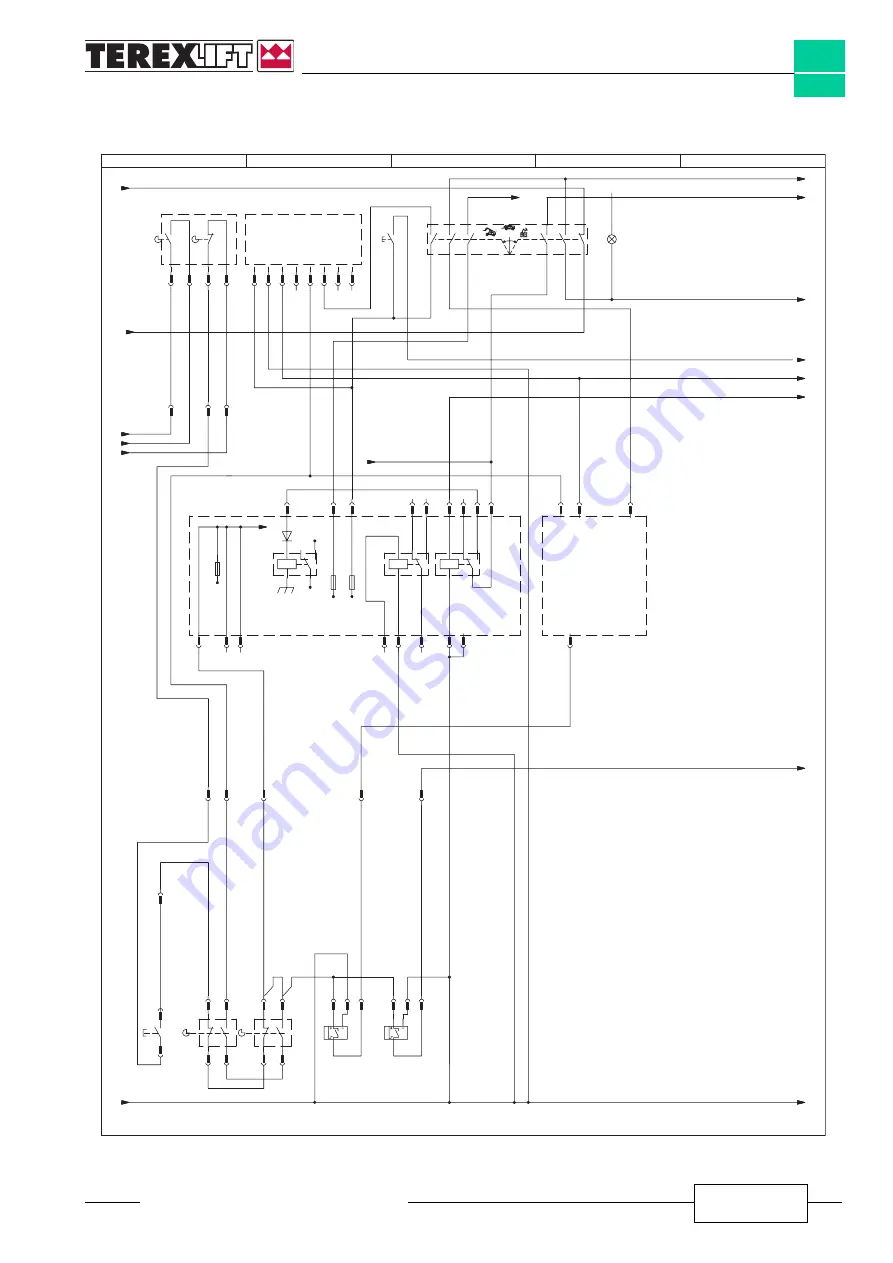
Document 57.4400.7200 - 1
st
Edition 03/2005
INDEX
6
17
TELELIFT 3713 Elite - 4017 - 4514
SCHEMES
6.4.7
Sheet 7 of 9
TECNORD
CONTROL UNIT
+15
S31
2
0
1
BOOM LIFTING
RIGHT SENSOR
PLA
T.SCALE CHANGE
OUTRIGGER DOWN
OVERLOAD SIGNAL
GROUND
POWER SUPPL
Y
+15
+30
+30
LIMIT SWITCH
RIGHT
OUTRIGGER
LIMIT SWITCH
LEFT
OUTRIGGER
BOOM LIFTING
LEFT SENSOR
S52
S51
OVERLOAD WARNING SYSTEM
3B6
+30
SWITCH GEAR
NOT ENGAGED
N1
N1
N1
A-N1
R-N1
A-N1
70
H-R1.5
Z-N1.5
C1
R-N1
B-G1
B-N1
G-M1
XJ1
A7
XJ1
B4
XJ1
C7
XJ1
A3
H/N1
9.1
A/R1
A-G1
H-R1.5
1.2
G-M1
9.1
V1.5
8.1
X6
2
F13
10A
H-R1.5
9.1
C-R1
2.5
G-M1
2.5
H/N1
H/N1
A/N1
8.1
M-N1
B-G1
9.1
H9
S35
S34 S33 S32
S30
A-N1
9.1
X21
6
X53
B
X53
A
X53
C
B41
C-B1
X7
10
X7
3
X7
11
X7
4
X7
2
K18
86
87a
87
85
30
S6b
S6a
N1
X7
13
X7
11
X7
12
X7
6
X7
7
X7
5
K19
86
87a
87
85
30
K22
86
87a
87
85
30
X4
6
X5
6
F25
10A
X21
1
X5
4
S10
B-N1
R-N1
B-G1
B-G1
A-G1
B-G1
A/R1
A/R1
A-R1
C-N1
C/N1
S-G1
B-G1
L-G1
N1
B-N1
9.1
X53
C
X53
A
X53
B
X22
6
X5
3
X22
10
X22
7
X26
3
S-G1
3.5
X26
4
N1
6.5
L-G1
1.5
3
B38
X52
3
X52
4
X52
1
X52
2
X51
3
X51
4
X51
1
X51
2
X25
7
X25
4
X25
5
X25
6
X25
8
X25
2
X25
3
X25
1
2
4
1
X26
2
31
8.1
31
6.5
X5
9
53
9.2
F18
10A
3
1
2
4
5
X22a
B54
RELAY
CARD
WORK
SELECTOR
Summary of Contents for TELELIFT 3713 Elite
Page 4: ...Courtesy of Crane Market...