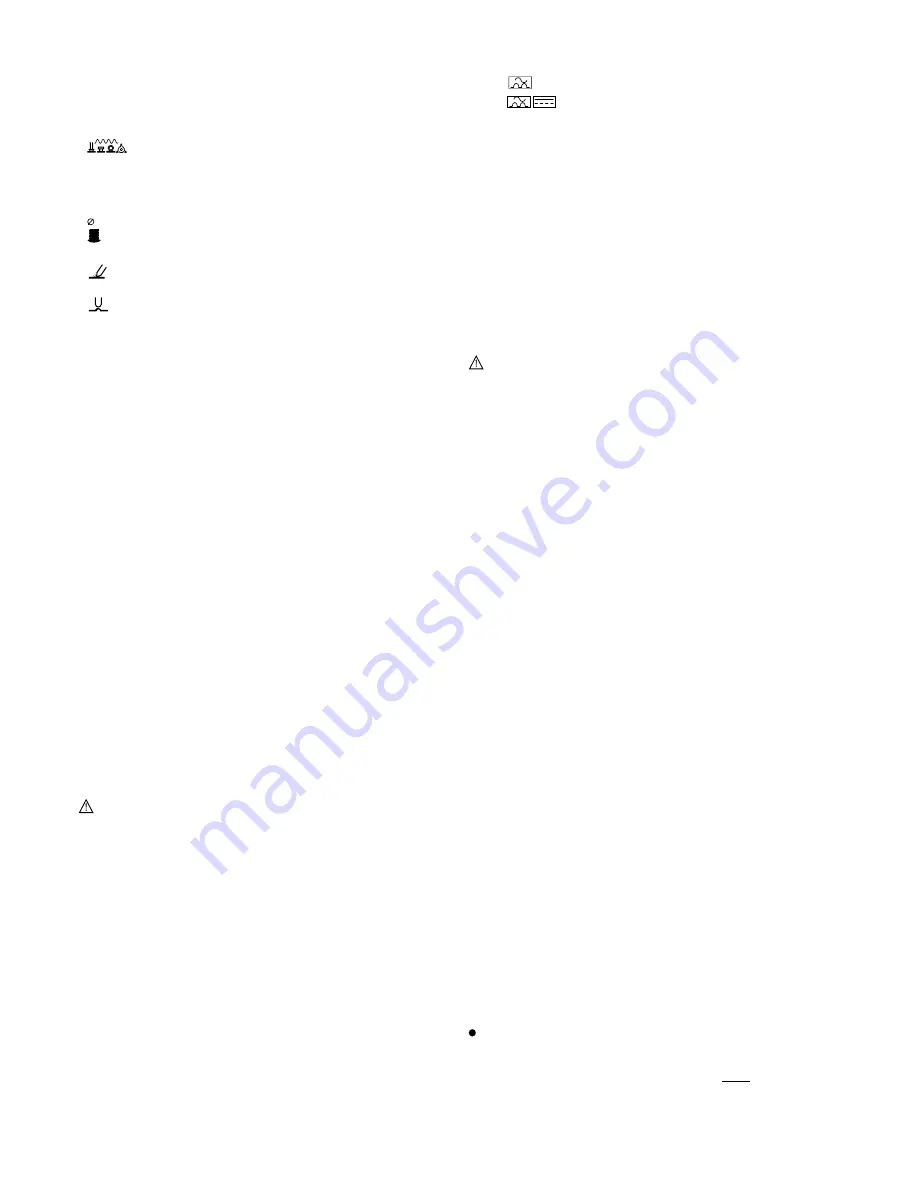
it being damaged.
neutral conductor connected to earth.
_____________________________________________________________________________________________________________________
In order to guarantee protection against indirect contact use RCD's of the following
types:
4.2 CONTROL PANEL (FIG. B2)
1- Spot welding operation selection key
- Type A (
) for single phase machines;
Allows the user to select the different spot welding operations.
- Type B (
) for 3-phase machines.
In order to satisfy the requirements of the EN 61000-3-11 (Flicker) standard we
2 – Spot welding function LEDs:
recommend connecting the spot welder to interface points of the main power supply that
have an impedance of less than Zmax = 0,362 ohm.
: For the spot welding of : plugs, rivets, washers, special washers with the
The spot welder does not fall within the requisites of IEC/EN 61000-3-12 standard.
Should it be connected to a public mains system, it is the installer's responsibility to
correct electrodes.
verify that the spot welding machine itself is suitable for connecting to it (if necessary,
consult the distribution network company).
2
: For the spot welding of Ø 4mm screws with the correct electrode.
5.4.2 Plug and socket
Connect the power supply cable to a standardised plug
(
3P
+
T
:
only
2
poles
are
used
for
the
400V
INTERPHASE
SYSTEM
connection
;
2P
+
T
:
230V
INTERPHASE
connection
)
: For the spot welding of Ø 5mm screws with the correct electrode.
of adequate capacity and prepare a power outlet protected by fuses or by an automatic
circuit-breaker; the appropriate earth terminal should be connected to the (yellow-
green) earth conductor of the power line.
The capacity and specifications of the fuses and circuit-breaker are given in the
: For sheet drawing with carbon electrode.
paragraph on “TECHNICAL DATA”.
Should more than one spot-welder be installed, distribute the power cyclically among
the three phases in order to obtain amore balanced load; e.g.:
: For sheets upsetting with the correct electrode.
spot-welder 1: power supply L1-L2;
spot-welder 2: power supply L2-L3;
spot-welder 3: power supply L3-L1.
3- Keys for adjusting the spot welding energy:
_____________________________________________________________________________________________________________________
The spot welding energy value of each spot welding function can be varied using these
keys
WARNING! Failure to observe the rules given above will invalidate the (class
I) safety system provided by the manufacturer causing serious risks to people
4- Display:
(e.g. electric shock) and objects (e.g. fire).
_____________________________________________________________________________________________________________________
Shows the energy level set between a limited interval of increasing or decreasing
numbers: each figure increase/decrease corresponds to a higher / lower energy level.
5.5 CONNECTING THE MANUAL CLAMP AND STUDDER GUN WITH EARTH
Shows any alarm signals (A1, A2, A3, A4).
CABLE (only for model 3kA - FIG. C)
- Connect the DINSE plugs to their corresponding sockets.
- Insert the control cable connector into its socket.
5-
*
:
"Spot welder operating" signalling LEDs.
6-
+
:
Thermal safeguard signalling LED (A1, A2).
6. (SPOT) WELDING
Signals that the spot welder has stopped because of overheating at the
6.1 PRELIMINARY OPERATIONS
output bars. Resetting is automatic when the temperature returns within
Before carrying out any spot-welding operation it is necessary to make a series of
the permitted limits.
checks and adjustments, which should be carried out with the main switch in the “O”
The display (4) shows "A1" when the thermostat cuts in during normal
position.
use, and "A2" when the thermostat cuts in because of a fault (in this
- Ensure that the electrical connections are correct, in accordance with the above
case switch off the machine and contact the technical support centre).
instructions.
Only for model 3kA:
- When using the manual clamp (Optional), remember that the force exercised by the
7-
,
:
Main power line signalling LEDs (A3, A4):
electrodes during the spot welding can be adjusted using the knurled nut
(Fig. D)
;
turn it clockwise to increase the force in proportion to the increase in sheet thickness
but make the adjustment that allows the clamp to close (triggering the corresponding
-
: Low power line voltage (spot welder being undersupplied). The display (4)
microswitch) with very little effort.
shows "A4".
- Between the electrodes, slide a shim equivalent to the thickness of the sheets;
ensure that the arms, brought together manually, are parallel and that the electrode
holders are centred (tips coincide).
.
Normal power line voltage (spot welder being supplied correctly).
- If necessary loosen the arm locking screws to adjust the arms by turning them both or
moving them in either direction along their axis; on completion secure the locking
screws tightly.
/
: High power line voltage (spot welder being oversupplied). The display (4)
shows "A3".
6.2 ADJUSTING THE (spot-welding) PARAMETERS
The parameters that affect the diameter (section) and mechanical strength of the spot
ATTENTION:
If supply is irregular, the oversupply or undersupply LED is illuminated,
weld are:
and you hear an intermittent beep, it is advisable to switch off the spot welder to avoid
- Force exerted by the electrodes.
damaging it.
- Spot-welding current.
- Spot-welding time.
If without specific experience, it is advisable to carry out some spot welding tests using
5. INSTALLATION
sheets of the same quality and of the correct thickness for the work to be carried out.
_____________________________________________________________________________________________________________________
Correct spot execution can be verified by draw testing the sample. If the kernel of the
welding point can be extracted from one of the two sheets, execution is correct.
WARNING! CARRY OUT ALL INSTALLATION OPERATIONS AND
ELECTRICAL AND PNEUMATIC CONNECTIONS WITH THE SPOT-WELDER
Model 3kA (Fig. B-1):
COMPLETELY SWITCHED OFF AND DISCONNECTED FROM THE POWER
The current and spot welding time parameters are automatically adjusted by selecting
SUPPLY OUTLET.
the thickness of the sheets to be welded using the key (2). The spot welder automatically
THE ELECTRICAL AND PNEUMATIC CONNECTIONS MUST BE MADE ONLY AND
sets the best welding time. The standard value (DEFAULT) of the spot time can be
EXCLUSIVELY BY EXPERT OR SKILLED PERSONNEL.
modified using the key (1), but must remain within the pre-set limits. As an example,
_____________________________________________________________________________________________________________________
with a low supply voltage (LED (
-
) lit) it may be necessary to slightly increase the
spot welding time, and viceversa if the (
/
) LED is lit. This modification is possible at
5.1 PRELIMINARY OPERATIONS
all times, in order to satisfy specific requirements.
Unpack the spot-welder, assemble the separate parts included in the package.
Model 2.5kA (Fig. B-2):
5.2 LIFTING THE SPOT-WELDER
The current and spot welding time parameters are set automatically when the required
WARNING:
None of the spot-welders described in this handbook have lifting devices.
spot welding function is selected using the key (1). The standard value (DEFAULT) of
the energy emitted during spot welding can be modified using the "+" and "-" keys (3) but
5.3 POSITION
must remain within the pre-set limits.
The installation area must be sufficiently large and without obstacles, suitable for
ensuring completely safe access to the control panel, to the main switch and to the
6.3 PROCEDURE
working area.
Ensure that there are no obstacles near the cooling air inlets and outlets and that no
conductive dusts, corrosive vapour, moisture etc. can be sucked in.
STUDDER GUN
0
Position the spot-welder on a plane surface made of uniform, compact material able to
WARNING!
support the weight (see the “technical data”) so as to prevent it from tipping or moving
- To fit or release the accessories on the studder chuck use the two fixed hexagon
dangerously.
wrenches to stop the chuck turning.
- When operating on doors and bonnets the earth bar MUST be connected to the
5.4 CONNECTION TO THE MAIN POWER SUPPLY
same part to prevent current passing through the hinges, and the bar must always
5.4.1 Warnings
be set near the welding area (if the current has to travel over long distances this will
Before making any electrical connection, make sure the rating data of the spot-welder
reduce the efficiency of the weld).
correspond to the mains voltage and frequency available at the place of installation.
- Spot-welding time is automatic and depends on which studder procedure has
The spot-welder should be connected only and exclusively to a power supply with the
been selected.
5
- 7 -
Summary of Contents for Digital Car Puller 5000
Page 102: ...FIG F FIG G FIG H FIG I 102 ...