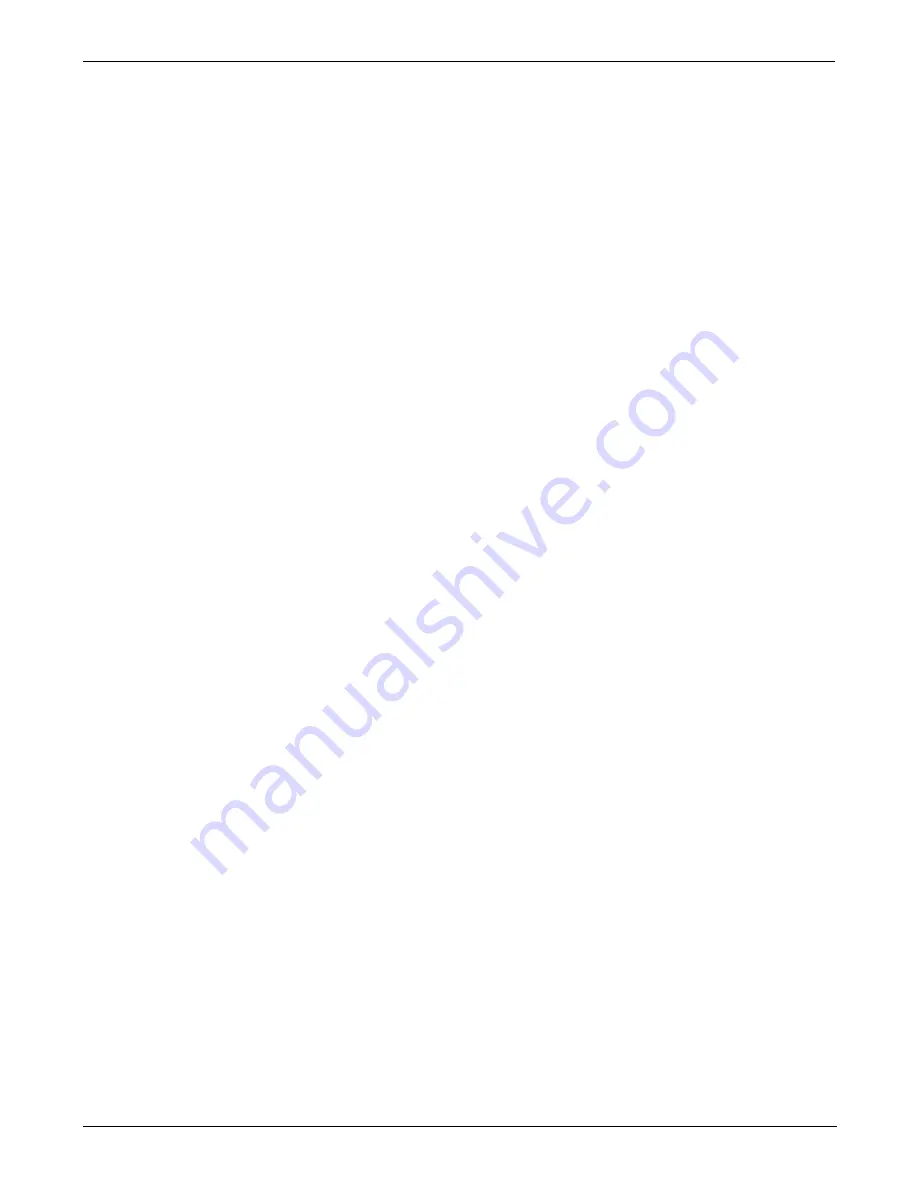
Troubleshooting & Service
Teledyne API - Model T200H/T200M Operation Manual
252
NO
2
converter heater failures can be divided into two possible problems:
•
Temperature is reported properly but heater does not heat to full temperature. In
this case, the heater is either disconnected or broken or the power relay is broken.
Disconnect the heater cable coming from the relay board and measure the
resistance between any two of the three heater leads with a multi-meter. The
resistance between
A and B should be about 1000 Ω and that between A and C
should be the same as between B and C, about 500 Ω each. If any of these
resistances is near zero or without continuity, the heater is broken.
•
Temperature reports zero or overload (near 500° C). This indicates a disconnected
or failing thermocouple or a failure of the thermocouple circuit.
First, check that the thermocouple is connected properly and the wire does not
show signs of a broken or kinked pathway. If it appears to be properly connected,
disconnect the yellow thermocouple plug (marked
K
) from the relay board and
measure the voltage (not resistance) between the two leads with a multi-meter
capable of measuring in the low mV range. The voltage should be about 12 mV
(ignore the sign) at 315° C and about 0 mV at room temperature.
Measure the continuity with an Ohm-meter.
It should read close to zero Ω. If the
thermocouple does not have continuity, it is broken. If it reads zero voltage at
elevated temperatures, it is broken. To test the thermocouple at room temperature,
heat up the converter can (e.g., with a heat gun) and see if the voltage across the
thermocouple leads changes. If the thermocouple is working properly, the
electronic circuit is broken. In both cases, consult the factory.
If the converter appears to have performance problems (conversion efficiency is outside
of allowed range of 96-102%), check the following:
•
Conversion efficiency setting in the CAL menu. If this value is different from 1.000,
this correction needs to be considered. Section 5.2.5 describes this parameter in
detail.
•
Accuracy of NO
2
source (gas tank standard). NO
2
gas standards are typically
certified to only ±2% and often change in concentrations over time. You should get
the standard re-certified every year. If you use GPT, check the accuracy of the
ozone source.
•
Age of the converter. The NO
2
converter has a limited operating life and may need
to be replaced every ~3 years or when necessary (e.g., earlier if used with continu-
ously high NO
2
concentrations). We estimate a lifetime of about 10000 ppm-hours
(a cumulative product of the NO
2
concentration times the exposure time to that
concentration). However, this lifetime heavily depends on many factors such as
absolute concentration (temporary or permanent poisoning of the converter is
possible), sample flow rate and pressure inside the converter, converter tempera-
ture, duty cycle etc. This lifetime is only an estimated reference and not a
guaranteed lifetime.
•
In some cases with excessive sample moisture, the oxidized molybdenum metal
chips inside the converter cartridge may bake together over time and restrict air flow
through the converter, in which case it needs to be replaced. To avoid this problem,
we recommend the use of a sample gas conditioner (Section 1.4). Section 6.3.4
describes how to replace the NO
2
converter cartridge.
•
With no NO
2
in the sample gas and a properly calibrated analyzer, the NO reading
is negative, while the NO
2
reading remains around zero. The converter destroys
NO and needs to be replaced.
07270D DCN7141