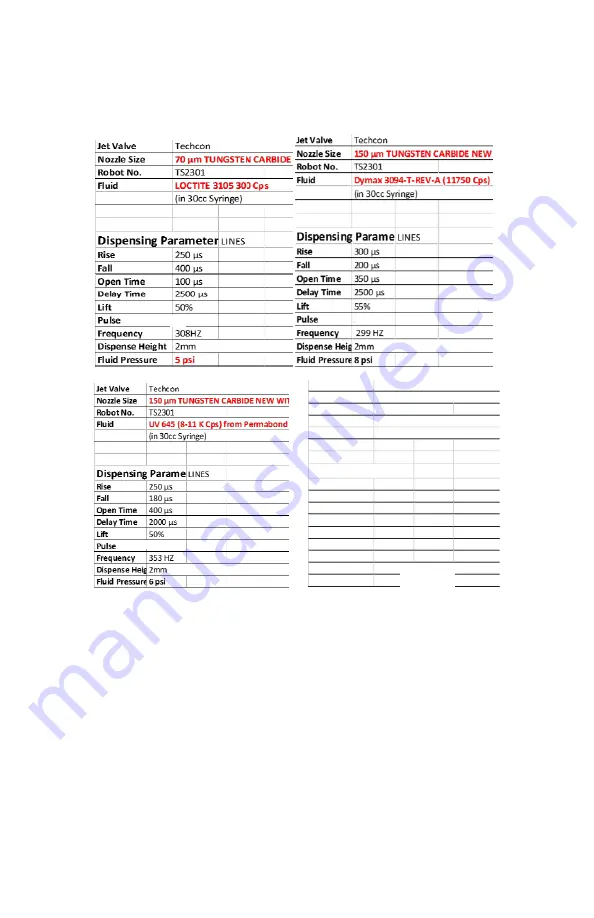
49
11.3 Sample parameters
Note:
parameters shown are for references only
Controller
Jet Valve
Nozzle Size
Robot No.
Fluid
Dispensing Parameters:
LINES
Rise
500 µs
Fall
180 µs
Open Time
800 µs
Delay Time
2200 µs
Lift
60%
Pulse
2
Frequency
272 HZ
Dispense Height
Fluid Pressure
60
(in 30cc Syringe)
2mm
Techcon
150 µm ceramic
TS2301
RHEOTEMP 768G (200-300K Cps)
PV UNIT FROM CHINA
Equipment:
75 Psi