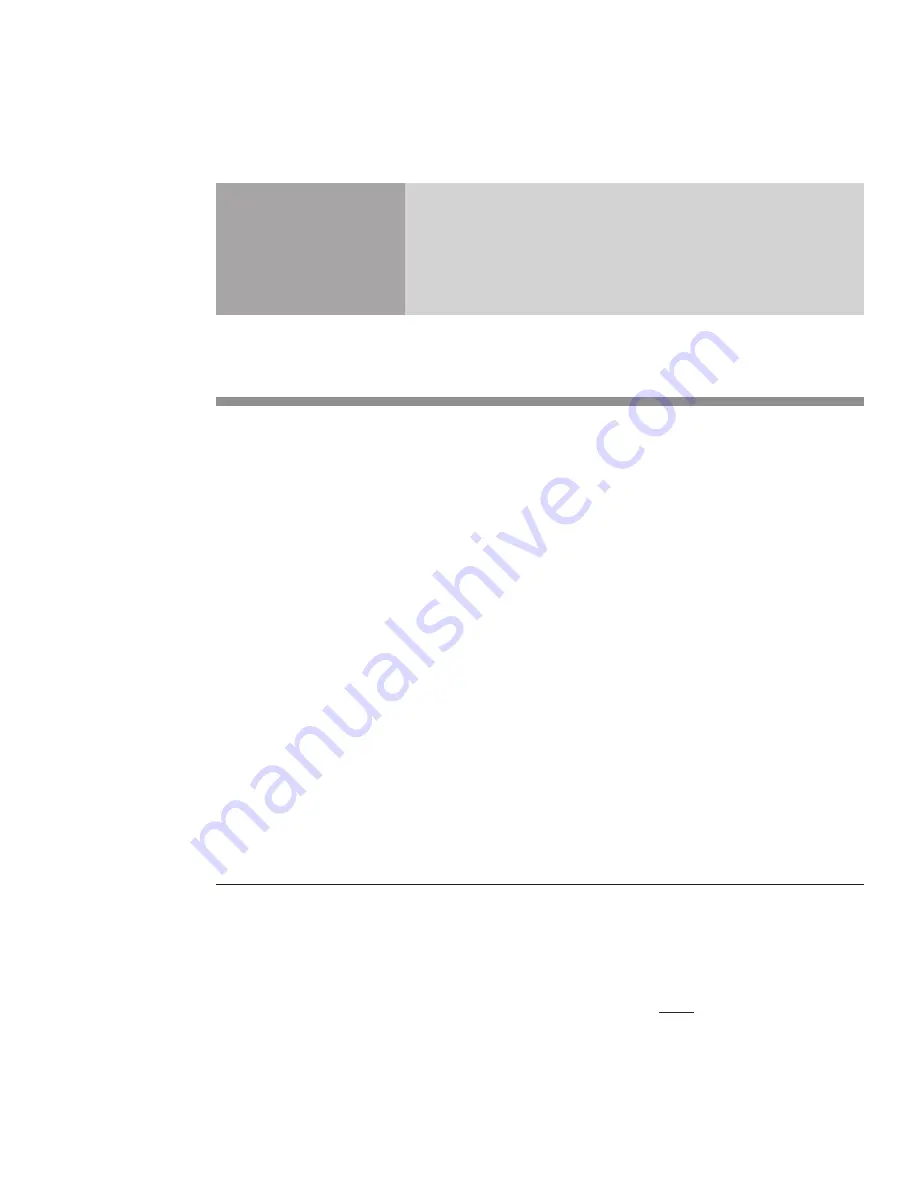
getting started
1
13
Synrad
Firestar i401
operator’s manual
Connecting
Caution
possible
equipment
damage
Operating the laser at coolant temperatures above 22 °C (72 °F) may
result in decreased performance and/or premature failure of electronic
components.
Table 1-2
Dew point temperatures
Dew Point Temperature Chart °F (°C)
Relative Humidity (%)
20 25 30 35 40 45 50 55 60 65 70 75 80 85 90 95
Air Temp
°F (°C)
60 (16)
— — — 32 36 39 41 44 46 48
50
52
54
55
57
59
(0) (2) (4) (5) (7) (8) (9) (10) (11) (12) (13) (14) (15)
65 (18)
—
—
33
37
40
43
46
48
51 53 55 57 59 60 62 64
(1) (3) (4) (6) (8) (9) (11) (12) (13) (14) (15) (16) (17) (18)
70 (21)
—
33
37
41
45
48
51 53 56 58 60 62 64 65 67 69
(1) (3) (5) (7) (9) (11) (12) (13) (14) (16) (17) (18) (18) (19) (21)
75 (24)
—
37
42
46
49
52 55 58 60 62 65 67 68 70 72 73
(3) (6) (8) (9) (11) (13) (14) (16) (17) (18) (19) (20) (21) (22) (23)
80 (27)
35
41
46
50 54 57 60 62 65 67 69 71 73 75 77 78
(2) (5) (8) (10) (12) (14) (16) (17) (18) (19) (21) (22) (23) (24) (25) (26)
85 (29)
40
45
50 54 58 61 64 67 70 72 74 76 78 80 82 83
(4) (7) (10) (12) (14) (16) (18) (19) (21) (22) (23) (24) (26) (27) (28) (28)
90 (32)
44
50 54 59 62 66 69 72 74 77 79 81 83 85 87 88
(7) (10) (12) (15) (17) (19) (21) (22) (23) (25) (26) (27) (28) (29) (31) (31)
95 (35)
48
54 59 63 67 70 73 76 79 81 84 86 88 90 92 93
(9) (12) (15) (17) (19) (21) (23) (24) (26) (27) (29) (30) (31) (32) (33) (34)
100 (38)
52 58 63 68 71 75 78 81 84 86 88 91 93 95 97 98
(11) (14) (17) (20) (22) (24) (26) (27) (29) (30) (31) (33) (34) (35) (36) (37)
To use Table 1-2, look down the
Air Temp
column and locate an air temperature in Fahrenheit or Cel-
sius (°C values are shown in parentheses) that corresponds to the air temperature in the area where your
laser is operating. Follow this row across until you reach a column matching the relative humidity in your
location. The value at the intersection of the
Air Temp
and
Relative Humidity
columns is the
Dew Point
temperature in °F (or °C). The chiller’s temperature setpoint must be set
above the dew point tempera-
ture. For example, if the air temperature is 85 °F (29 °C) and the relative humidity is 60%, then the dew
point temperature is 70 °F (21 °C). Adjust the chiller’s temperature setpoint to 72 °F (22 °C) to prevent
condensation from forming inside the laser.