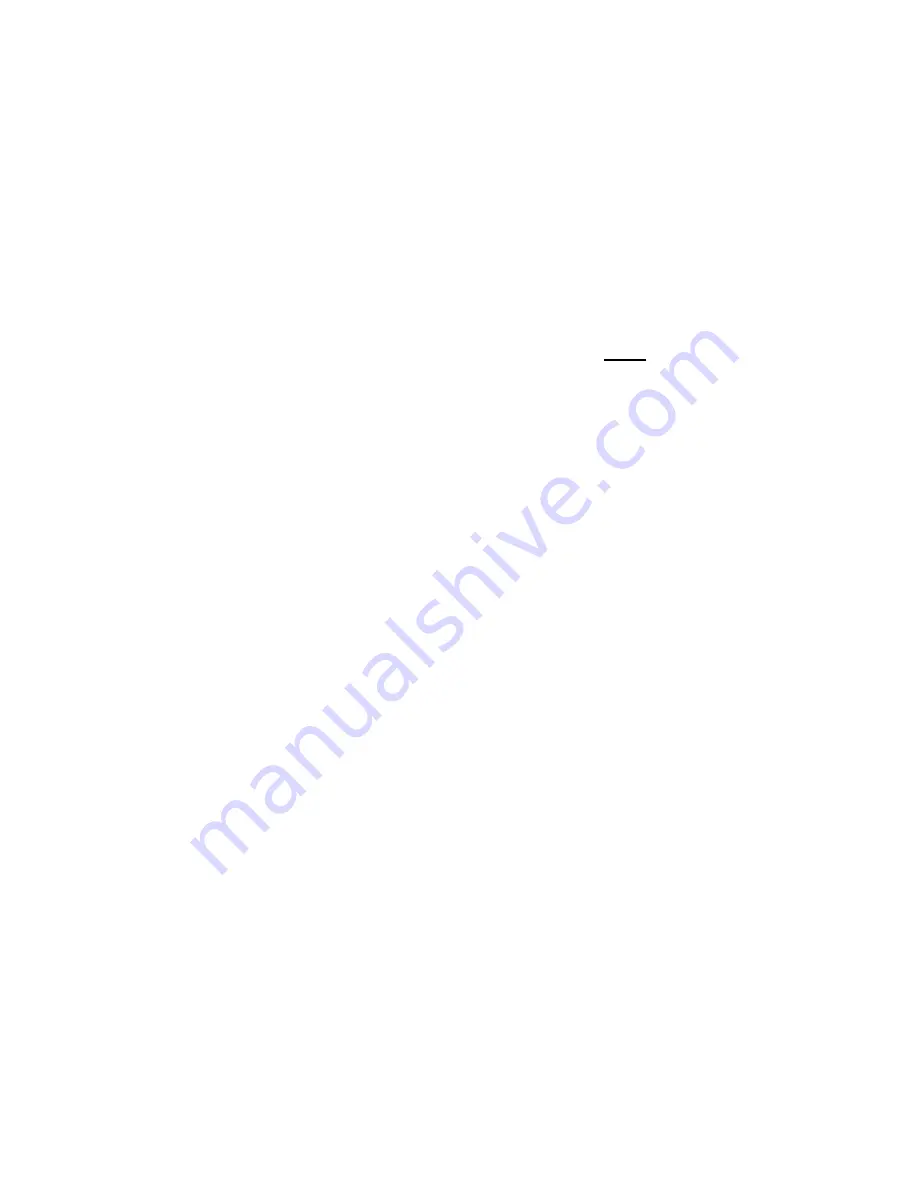
CyberAiR DX Floor Mounted IOM Manual
2.9.6
Head Pressure Controls- Air Cooled
Systems
2.9.6.1
-20°F Condenser Fan Speed
Used for outdoor or indoor installations where ambient
condenser air inlet temperatures may fall to -20°F,
variable speed condenser motor control is used to
maintain head pressure. The variable speed motor
is located closest to the header end of the
condenser.
The fan speed control is a continual modulation of
the motor’s speed. The condenser fan speed
controller
is factory installed in the remote outdoor
condenser electric box. The fan speed controller
requires no adjustment.
Wire the condenser in accordance with the electrical
schematic and appropriate codes. The fan speed
controller will automatically control the head
pressure. On systems with more than one fan on the
condenser, the remaining motors cycle on and off
based on pressure.
Factory setting: Switch contacts are set to close on a
pressure rise to 440 psig and open at 330 psig. Set
point range is 200 to 610 psig. The differential is set
at 110 psi and is adjustable.
2.9.6.2
-30°F Flooded Head Pressure Control
Used for outdoor or indoor installations where
ambient condenser air inlet temperatures may fall to -
30°F, flooded head pressure control is designed to
maintain head pressure during low ambient
conditions. A head pressure control valve and a
receiver is used in the refrigeration circuit to back up
liquid refrigerant into the condenser coil. The head
pressure control valve
is a 3-way modulating valve controlled by discharge
pressure.
When the A/C unit begins to operate, the discharge
pressure rises to 320 psig and the condenser fan is
cycled on, as described in Section 2.10.2.1. When
ambient temperature drops, the discharge pressure
drops also. When the discharge pressure drops, the
head pressure control valve diverts discharge gas
away from the condenser to the receiver. Liquid flow
from the condenser is restricted, causing liquid to
back up in the condenser.
Flooding the condenser reduces the area
available for heat transfer. The desired result is to
increase the pressure into the condenser,
maintaining a minimum
discharge pressure during low ambient operation
thus ensuring proper condensing temperature. The
head pressure control valve requires no adjustment.
While the fan is running, the flooded head pressure
control valve modulates the amount of discharge
gas entering the receiver. As the pressure
increases, the valve diverts more discharge gas to
the condenser, allowing more liquid to flow from
the condenser to the receiver.
When using this method of head pressure
regulation there must be enough refrigerant in the
system to ensure adequate charge at the lowest
expected ambient temperature in which the system
will be operating. A receiver is used to store the
extra refrigerant when the condenser is not using
it.
NOTE
Systems utilizing air cooled condensers,
(D2A models), must not have a refrigerant line
pressure drop over 14 psig across the
condenser and the interconnecting piping to
the condenser sections. See the line sizing
tables in section 2.7.1.2.
2.9.7
Head Pressure Control-
Water-Water/Glycol Cooled Systems
Condensing temperature is maintained by liquid
flowing through a regulating valve and then into the
condenser. The regulating valve opens to increase
the liquid flow as the refrigerant pressure rises (or
closes as the refrigerant pressure falls).
CyberAir DX units have two refrigeration circuits.
Each circuit has its own pressure transducer. The
system controller monitors a signal from each
pressure transducer to determine how far to open the
regulating valve. The controller automatically
changes the control valve position to maintain head
pressure based on the difference between the set
point value and the actual measured value. The
controller transmits a proportional 0 to 10 VDC signal
to the regulating valve with 10 VDC corresponding to
the valve opening 100%.
The system controller is factory set for the
correct condensing pressure however, it can be
adjusted to increase or decrease the pressure.
Adjustment is made by entering the Factory
menu in the
E²
controller. Refer to the IOM manual provided under
separate cover for the system controller before
making adjustments to the controller.
Adjustments should be made in small increments.
Adequate time must be allowed between
adjustments for the valve to fully respond to the
control signal and for the changes in system
operation to be observed.
2-23