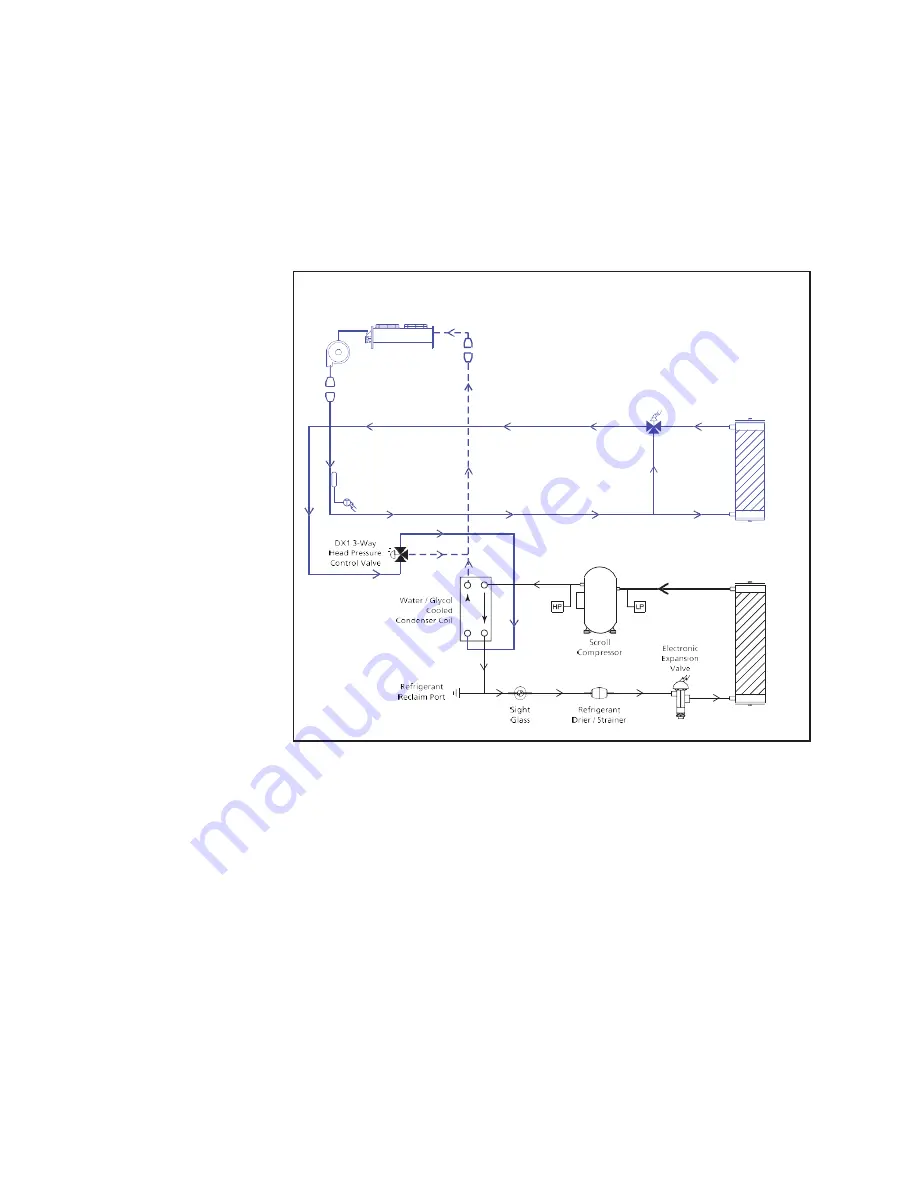
CyberAiR DX Floor Mounted IOM Manual
1.7 Free-Cooling Operation
The free-cooling configuration is available to minimize the use of compressor operation during low ambient
conditions for system energy savings. A FC (free-cooling) system utilizes a remote drycooler to provide
water/glycol coolant to a free-cooling coil positioned within a DX refrigerant system. If outdoor air temperatures
permit free-cooling operation (adjustable user set point), the free-cooling mode is enabled to take advantage of
the low ambient conditions to provide cooling with partial use or without the use of the system compressor(s).
Free-cooling provides an excellent opportunity for reduced operational cost by reducing the compressor
operating hours.
The free-cooling sequence is
enabled if the entering fluid
temperature is below the user
adjustable free-cooling enable
set point and the return air
temperature rises to the free-
cooling set point plus dead
band.
The drycooler pump activates
and the 3-way control valve
directs chilled water/glycol
coolant to the FC coil. The
outdoor fluid cooler is controlled
by first switching
the leaving fluid control set
point from typical DX heat
rejection to free-cooling control
(adjustable set point, ambient
air) and by controlling the
leaving fluid to its user
adjustable set point. The free-
cooling control valve opens
proportionally to the demand for
cooling based on the return air
temperature’s deviation from set
point.
If the return air temperature
continues to rise, the free-
cooling valve position eventually
reaches 100% open,
maximizing the
flow of coolant through the free-
cooling coil. Continued
operation
in this position indicates the A/C unit is unable to
lower the air temperature to the desired set point in
the free- cooling mode.
The compressor activates if the DX cooling stage
enable temperature set point has been reached or if
the control valve position reaches 100% open for 20
seconds (default). The free-cooling circuit and the
compressor operate in series to provide maximum
cooling. The 3-way control valve continually
modulates the flow of coolant in response to
temperature with the compressor running.
The compressor cycles off based on the normal
compressor temperature cut-out settings once the
set point is maintained.
Figure 5- Free-Cooling Diagram
As the outside air temperature increases above the
ambient air switch-over setting, the fluid cooler
controls cycle back to typical DX heat rejection
allowing the leaving fluid control set point to increase
above
the prevailing ambient conditions. The indoor unit’s
inlet fluid temperature sensor monitors the fluid
temperature and deactivates the free-cooling
mode once the fluid temperature increases above
the user adjustable enable set point. The system
compressors become the primary cooling source
and will activate as the return air temperature
increases above the set point.
1-10
DX Cooling
Coil
Free-
Cooling
Free-
Cooling
3-Way Mixing
Modulating Valve
Pump
(Optional
Remote
Drycooler