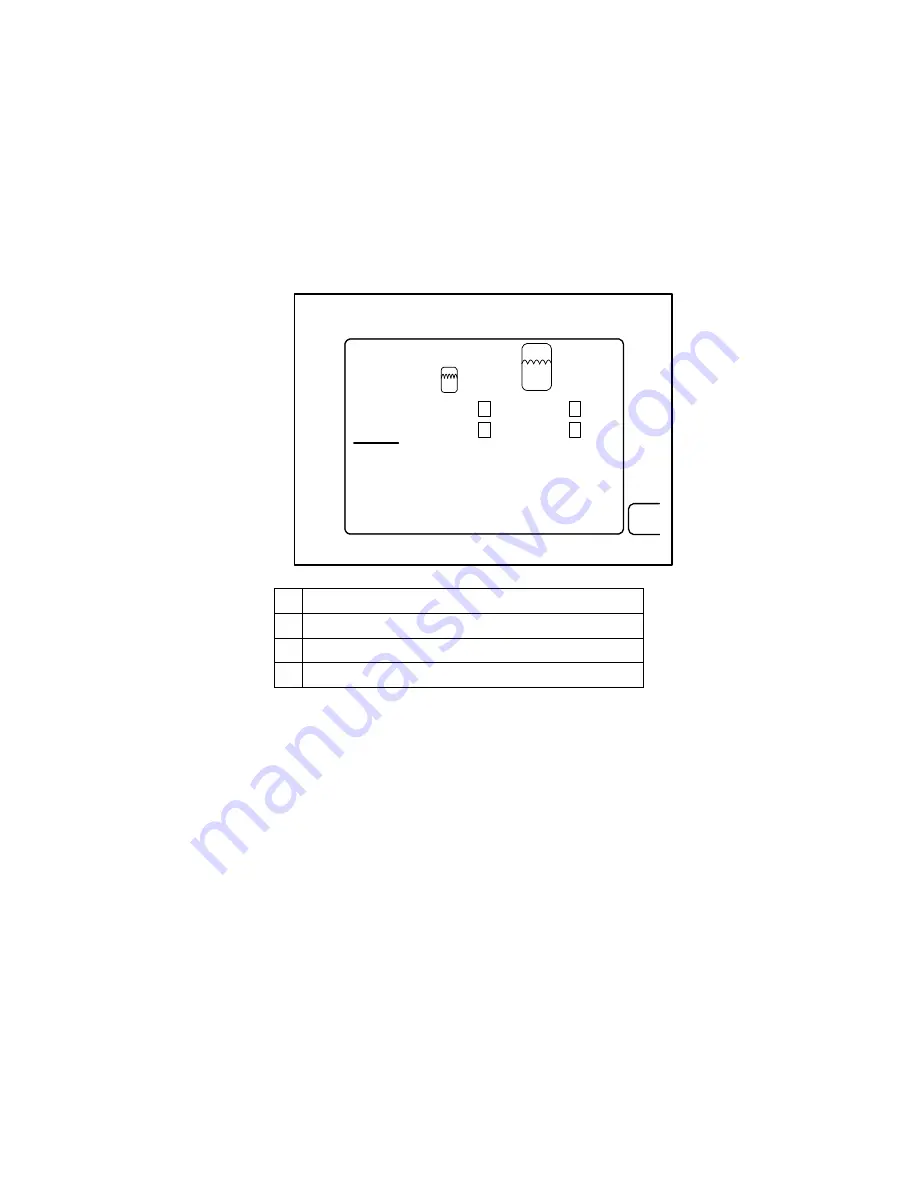
Once a response comes back, that value is displayed in the level sensor data
screen. The value will be a hexadecimal figure representing the physical location of
each magnet. (See Figure 2) The first value will be received from the small tank’s float
sensor, since it is the closest to the top of the transducer rod. Next the signal from the
small canister reference magnet will be received, followed by the signal from the large
canister’s float sensor. Finally, the signal from the large tank’s reference magnet will be
received. Under normal operation the values will be placed as shown in figure 2.
ESC
FLOAT
LEVEL SENSOR DATA
REF
1F341
192B8
06089
DIFF
VOLUME 00445
APP
35D40
3CF40
07200
01071
B
C
D
E
B
Response From Small Tank Float Sensor
C
Response From Small Tank Reference Magnet
D
Response From Large Tank Float Sensor
E
Response From Large Tank Reference Magnet
Figure 2. Response Time Values For Level Sensor
Each magnet has a number range that it should fall between. (Especially the
reference magnets since they do not move) The software does not compare the actual
returned values to make sure they are within an expected returned value range. It
simply takes the first response and
assumes
the value is the response for the small
canister’s float sensor [B]. Likewise, the second response is automatically assumed to
be the response for the small canister’s reference magnet [C]. Therefore, if only one
magnet has failed, the remaining three responses will be entered as if they were the
expected
first three. The data for the fourth response will be missing. (It was placed in
the 3
rd
slot) Consequently, the large tank’s reference magnet’s slot will display all zeros.
Figure 3 illustrates the expected value range for all four magnets, while Figure 4 is an
example of what the level sensor data screen will display when a magnet has failed.
6-36
Summary of Contents for 0702-002-620
Page 1: ......
Page 3: ......
Page 5: ......
Page 15: ......
Page 17: ......
Page 19: ......
Page 21: ......
Page 22: ...Chapter 1 Operational Description...
Page 23: ......
Page 27: ......
Page 28: ...Chapter 2 Ultra Rover Disassembly...
Page 29: ......
Page 31: ...4 Remove front cover assembly P N 0702 001 070 CH and place aside 2 2...
Page 37: ...4 Remove front cover assembly P N 0702 001 070 CH and place aside 2 8...
Page 42: ...4 Remove front cover assembly P N 0702 001 070 CH and place aside 2 13...
Page 49: ...4 Remove front cover assembly P N 0702 001 070 CH and place aside 2 20...
Page 81: ...4 Remove front cover assembly P N 0702 001 070 CH and place aside 2 52...
Page 103: ......
Page 105: ......
Page 106: ...Chapter 4 Docker Disassembly...
Page 107: ......
Page 133: ......
Page 134: ...Chapter 5 Troubleshooting...
Page 135: ......
Page 167: ......
Page 168: ...6 33 Chapter 6 Technical Procedures...
Page 169: ......
Page 219: ......
Page 220: ...Chapter 7 Installation...
Page 221: ......
Page 224: ...7 3...
Page 228: ...Chapter 8 Appendices...
Page 229: ......
Page 231: ......