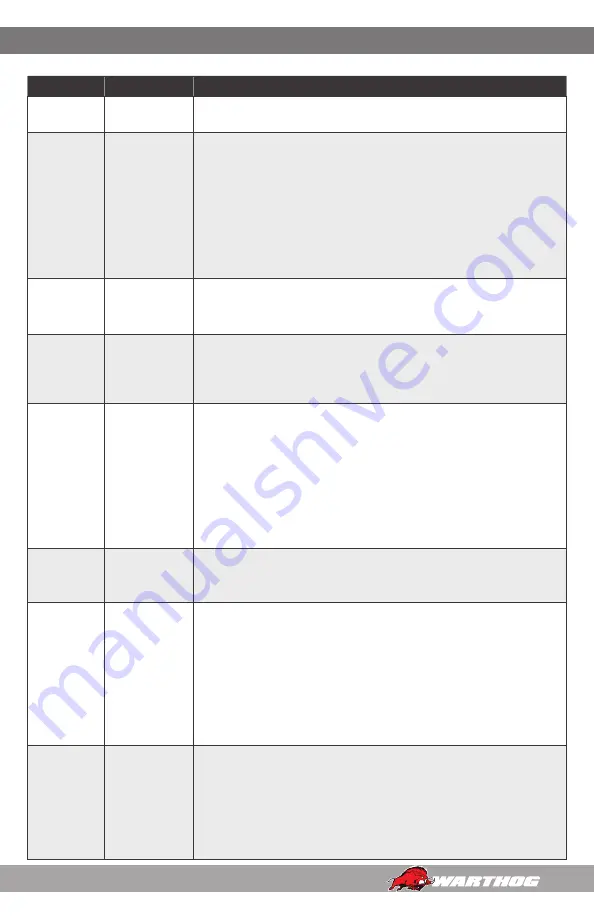
ITEM
FREQUENCY
MAINTENANCE REQUIRED
Nozzle
Weekly
• Rinse the nozzle with clean water to remove debris between the
head, body and shaft.
Inserts
Weekly
• Inspect all inserts for blockages.
• Remove inserts with blockages and clean and dry them thoroughly.
• Use thread sealant and ensure inserts are not cross threaded when
inserting them back into the head.
• Install the inserts back into the exact locations from which they were
removed to ensure the nozzle remains balanced.
• If using the nozzle in recycled water, remove inserts and check for
the following; Erosion or chipping of the orifice, missing or damaged
flow straighteners, and/or visible damage to the insert itself.
Backplates
Weekly
• Inspect the backplate screws.
• If the screws are loose, remove all of them and check screws, body,
and threads are clean and dry.
Fins
Weekly
• Inspect Fins for movement, wear (using wear indicators), and chips
on the ends.
• If the fins are loose, remove all of them and check screws, body, and
threads are clean and dry.
Head
Weekly
• Ensure head is rotating properly; when turned by hand, head should
turn free with slight, smooth resistance.
• If head spins too fast or sounds different than usual, nozzle may be
low on viscous fluid or fluid is contaminated.
• If head feels gritty when turning, flush between head and body.
• If head still feels gritty when turning, rebuild recommended.
• CONTROL CLEAN SWITCHER ONLY- Check the depth of the groove
on the head. If the groove becomes too shallow, it will allow for wear
on the nozzles.
Insert
Orifice
Size
Every 6
months
• Inspect insert orifice size with pin gages.
• Replace inserts as needed to retain most effective jetting capability
and cleaning efficiency during operation.
Body
After one Year
• See “Viscous Fluid Replacement” section of the User Manual.
• Flush viscous fluid with same type (BJ 048-M).
• This procedure is
only
recommended for replacing with the
same
fluid. Not all of the fluid will be replaced during the flushing
procedure, therefore full disassembly and cleaning of the tool is
recommended when changing to a different speed, or viscosity of
fluid.
• Full fluid change is necessary when replacing bearings and shaft
seals.
Nozzle
After two
Years
• Full disassembly, inspection, and overhaul. See complete
Disassembly
and Assembly instructions in the User Manual or Maintenance Video.
(Links provided below.)
• Take care throughout the entire procedure to keep the internals clean
and free from grit, lint, and contamination. Failure to do so could
result in premature failure after service.
WGR SWITCHER ASSEMBLY
WGR MAGNUM AND SWITCHER MAINTENANCE SCHEDULE
25
866-795-1586 • WWW.SEWERNOZZLES.COM