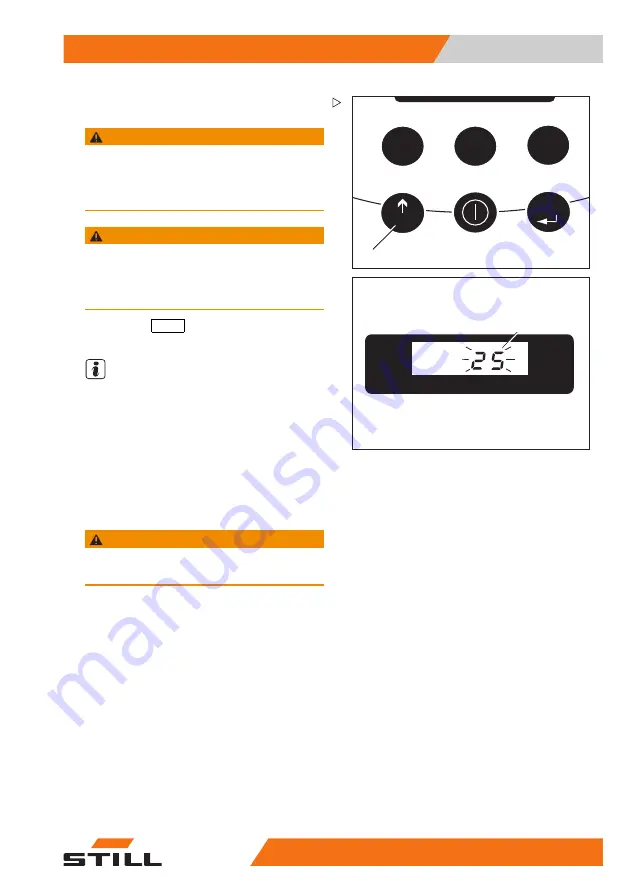
Maintenance
6
Maintenance as required
123
456
789
PRG
PRG
1044_606-008
1
%
2
1044_606-016
Charging the lead battery
WARNING
The battery could be damaged, shorted or an
explosion could occur.
Do not place any metallic objects or tools on the
battery. No naked lights, no smoking permitted!
WARNING
The electrolyte (diluted sulphuric acid) is poisonous
and caustic!
Follow the safety precautions for handling battery
electrolyte.
– Press the
PRG ↑
(scrolling) button (1) to
display the existing battery charge (2).
NOTE
After the battery is connected, the correct state
of charge appears only after approx. 1 minute.
Charging the gel battery
– Refer to instructions for this battery.
WARNING
Disconnect the battery plug only when the truck and
charger are switched off.
50108043033 [EN]
127
Summary of Contents for KANVAN-05
Page 2: ......
Page 8: ...Table of contents g 7 Technical data Datasheet VDI 146 Wheels and tyres 149 VI 50108043033 EN ...
Page 9: ...1 Foreword ...
Page 18: ...1 Foreword Environmental considerations 10 50108043033 EN ...
Page 19: ...2 Introduction ...
Page 32: ...2 Introduction Residual risks 24 50108043033 EN ...
Page 33: ...3 Safety ...
Page 49: ...4 Overview ...
Page 65: ...5 Operation ...
Page 121: ...6 Maintenance ...
Page 139: ...Maintenance 6 Maintenance as required 1050_003 028 F5 F3 F1 F4 F8 50108043033 EN 131 ...
Page 140: ...6 Maintenance Maintenance as required 132 50108043033 EN ...
Page 152: ...6 Maintenance Maintenance every 5000 hours 144 50108043033 EN ...
Page 153: ...7 Technical data ...
Page 158: ...7 Technical data Wheels and tyres 150 50108043033 EN ...
Page 162: ......
Page 163: ......
Page 164: ...STILL GmbH Berzeliusstrasse 10 D 22113 Hamburg Ident no 50108043033 EN ...