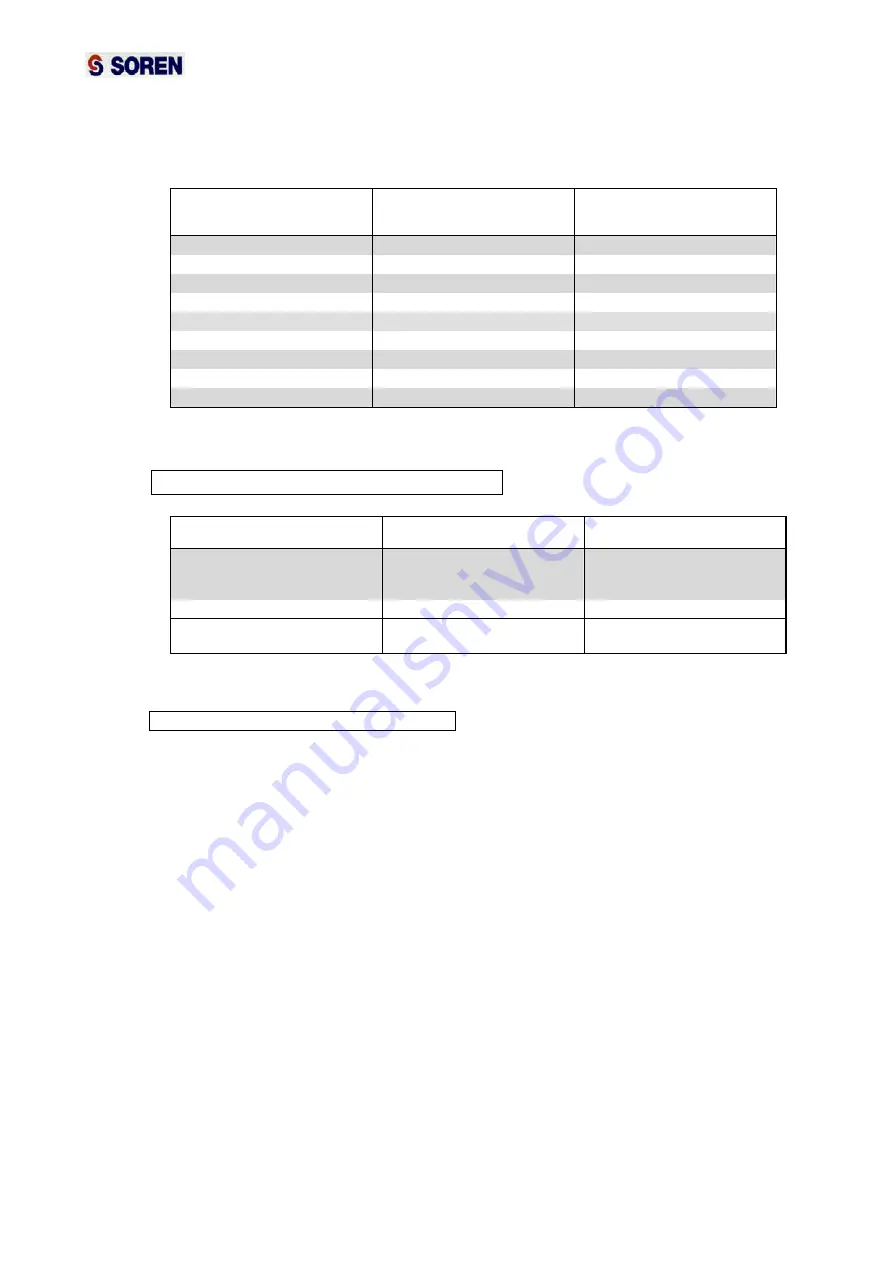
RIPPLE PUMPS INSTRUCTIONS MANUAL mod. N. 1 FAR - s/n V-0067 / V-0068 – Machinery
world
C.2009573
GEAR CASE CAPACITY
PUMP
MODEL
VERTICAL
INLET/OUTLET
CAPACITY LITRES
HORIZONTAL
INLET/OUTLET
CAPACITY LITRES
N. 0
0.18
0.22
N. 0,5
0.33 0.50
N. 1
0.33
0.50
N. 2
0.33 0.50
N. 2,5
0.75
1.20
N. 3
0.75 1.20
N. 4
3.00
4.00
N. 6
3.00 4.00
LUBRICATION PROGRAMME
PART LUBRICANT
TIME
INTERVAL
GEAR CASE
OIL
. CHECK WEEKLY
. CHANGE EVERY 500
WORKING HOURS
ROTOR AND INSIDE BODY
ALIMENTARY TYPE
LUBRICANT
. EACH TIME YOU RE-
ASSEMBLE THE PARTS
OIL CONTROL, TOPPING UP, CHANGE
•
WATER CONTAMINATED OIL
Control regularly for water seeping eventually into gear case. Change the oil
immediately if it is highly contaminated with water.
•
LOW OIL LEVEL
(All models except N.0)
Control oil level every week through the sight glass. Add oil if the level does
not reach the middle of the sight glass, following correct procedures: see OIL
FILLING.
(Mod. N.0 only)
Control the oil level every week removing one of the two level plugs. Add oil
if the level does not reach the middle of the sight glass, following correct
procedures: see OIL FILLING.
•
PROGRAMMED OIL CHANGE
Change oil every 500 working hours.
•
OIL DRAINAGE
Put a suitable container under the bottom oil plug.
Remove the plug and leave the oil to drain until the gear case is completely
empty. Then put back the bottom plug.