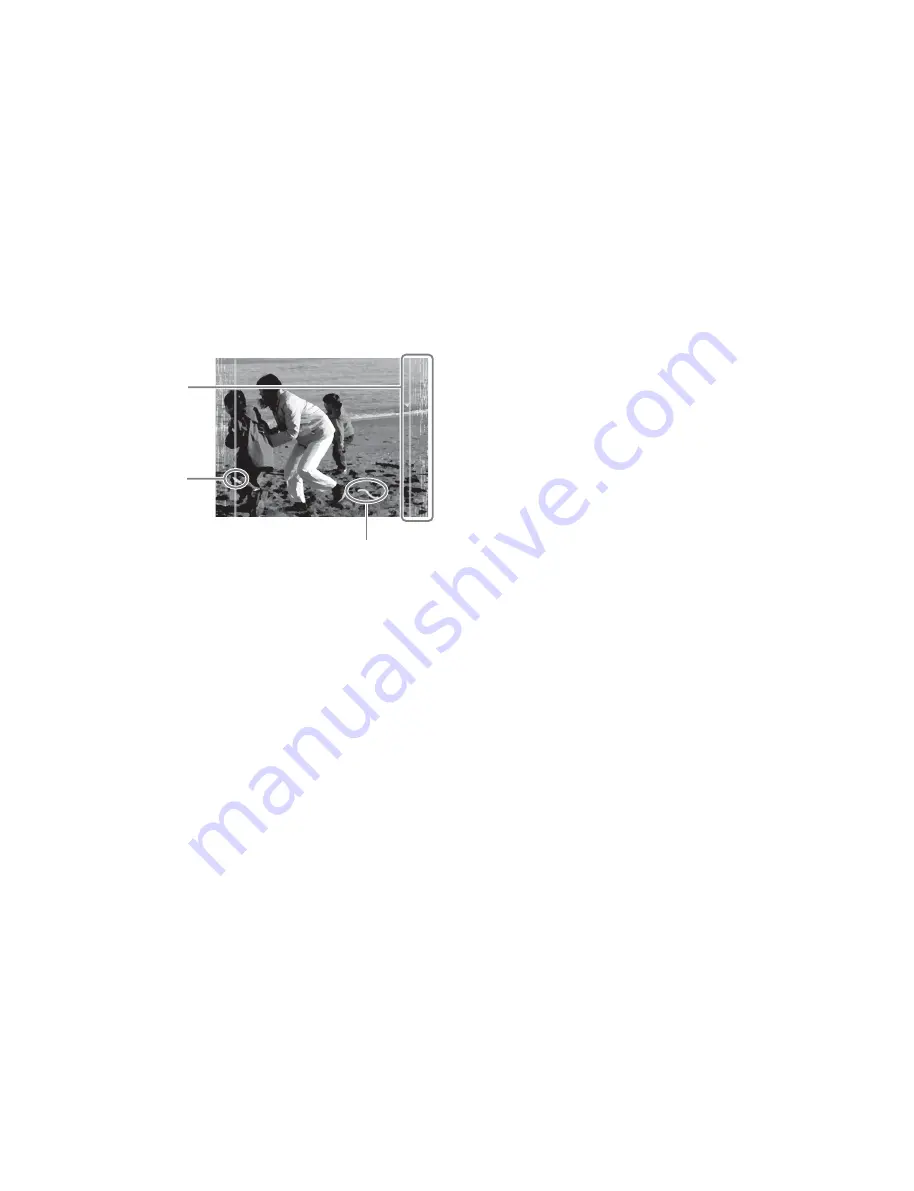
1-34 (E)
UP-CX2
1-10. Cleaning
The following cleaning method is described in Operating Instructions as well.
1-10-1. Cleaning the Inside of the Printer
If defects such as white stripes, fading, or scratches begin to appear in printouts, you may need to clean
the thermal head and rollers. In particular, white stripes and lines tend to appear when using the
2UPC-C54 series or 2UPC-C58 series printing pack after printing a large quantity of prints with the
2UPC-C53 series or 2UPC-C55 series printing pack.
The following items are necessary to perform interior cleaning.
.
The cleaning cartridge supplied with the printer
.
The cleaning sheet supplied with the printing pack
Cleaning Sheet (4-190-886-01)
.
Print paper
m
.
The cleaning cartridge is reusable. Do not throw it away.
.
As the cleaning sheet in not reusable, discard it after the
fi
rst use.
.
If there is insuf
fi
cient print paper remaining, an error may occur. If this occurs, replace the print paper
and begin the cleaning process again.
Threadlike scratch
Speckled
scratch
White stripe or
fading
Summary of Contents for UP-CX2
Page 1: ...DIGITAL PHOTO PRINTER UP CX2 SERVICE MANUAL 1st Edition ...
Page 6: ......
Page 44: ......
Page 62: ......
Page 82: ......
Page 92: ......
Page 94: ...7 2 UP CX2 7 2 Exploded Views Top and Side Panel Block 2 1 3 5 5 5 5 4 6 10 7 9 8 ...
Page 120: ......
Page 121: ......
Page 122: ...Sony Corporation UP CX2 CN UP CX2 SY J E 9 968 775 01 2010 11 08 2010 ...