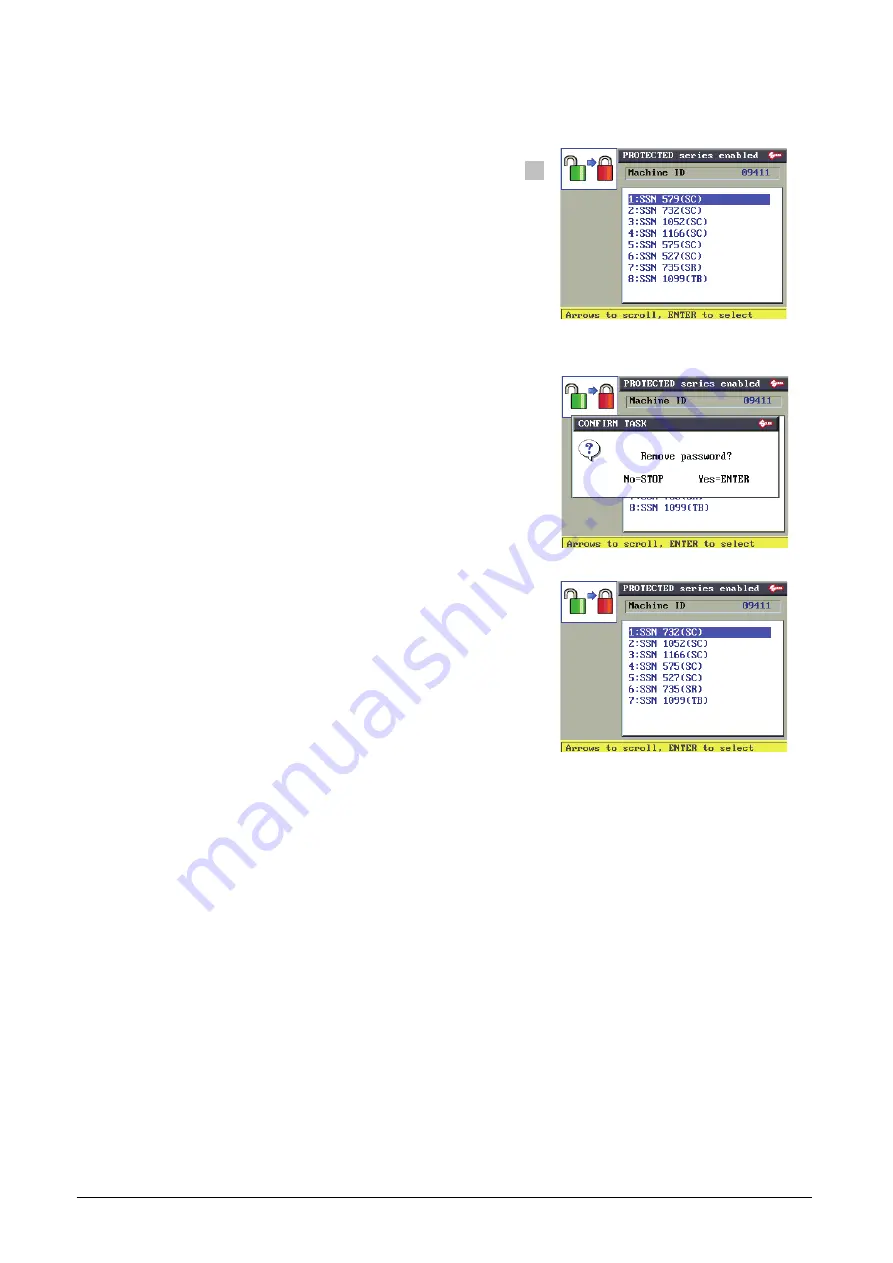
Operating Manual - English
Triax QUATTRO
- 64 -
Copyright Silca 2011
1
5.13
PROTECTED SSN (DISABLE)
F1
From the screen press MENU and/or
F4
to enable the
function.
List of protected systems already enabled.
They can be protected again.
Use the arrow keys (up and down) to select the protected
system already enabled.
F1
to protect the SSN again.
The display shows another message requiring confirmation of removal:
STOP to quit the operation without editing.
ENTER to confirm.
After confirmation the display will show.
Summary of Contents for Triax Quattro
Page 2: ......
Page 4: ......
Page 8: ......
Page 106: ...Triax QUATTRO Copyright Silca 2011 1 II ...
Page 107: ...Triax QUATTRO Copyright Silca 2011 III ...
Page 108: ...Triax QUATTRO Copyright Silca 2011 1 IV ...
Page 109: ...Triax QUATTRO Copyright Silca 2011 V ...
Page 110: ...Triax QUATTRO Copyright Silca 2011 1 VI ...
Page 111: ...Triax QUATTRO Copyright Silca 2011 VII ...
Page 112: ...Triax QUATTRO Copyright Silca 2011 1 VIII ...
Page 113: ...Triax QUATTRO Copyright Silca 2011 IX ...