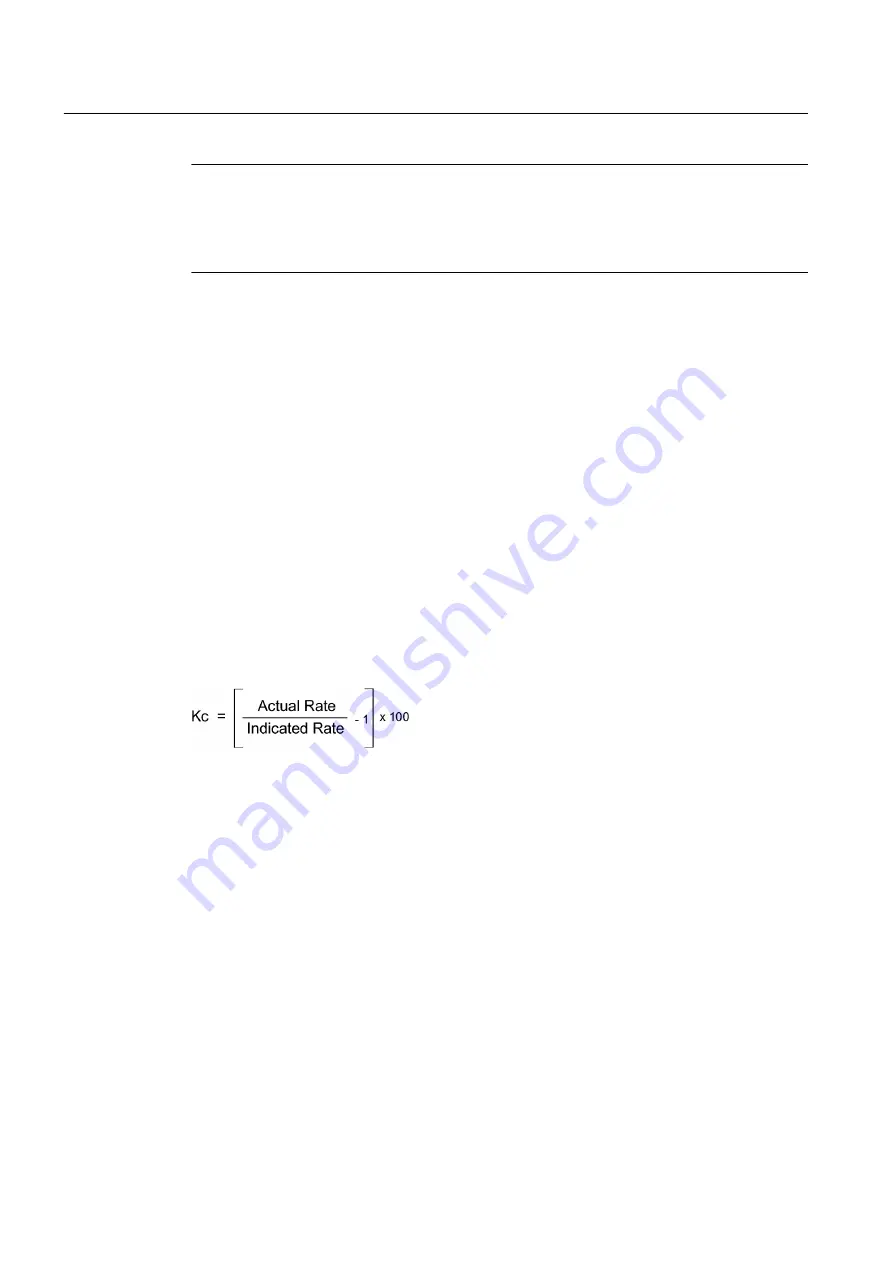
Note
Changing the calibration can cause profound changes in flowmeter operating characteristics.
Use only the most respected flow standard to obtain a correction factor. The percentage
entered must provide an accurate and consistent shift across the entire flow range anticipated
for the application.
Kc Factor
To obtain the Kc factor, compare flow total data taken simultaneously from the flowmeter and
a reference meter whose accuracy meets the required standard. Allow both meters to
accumulate flow total data long enough to average out any differences due to flow fluctuation
between the two meter locations. Compare outputs of the two totalizers to determine
percentage increase (+) or decrease (-) that is necessary to produce the best average
correlation between the flowmeter and the reference standard.
Selecting the Kc Factor
When the [Kc] menu cell is selected, the flowmeter imposes this percentage slope adjustment
of its rate output. Output data is zeroed and corrected for the Reynolds number (flow profile
compensated), however, a percent change in the rate output is imposed based on the data
entered in this cell. The number entered by the user is evaluated into a slope correction factor
by dividing it by 100 and algebraically adding it to 1. The resulting factor is used as a multiplier
on the rate register of the instrument. Thus an entry of -3% will multiply the rate register by
0.97, for example.
To calculate Kc:
To enter the Kc Factor
1. To enable numeric entry press <Right>.
2. Use the numeric keys to type the required Kc (as calculated above). Note that the Kc value
can be negative or positive. Enter the - or + sign first, then type in the calibrated value.
3. To store the data press <ENT>. Note that Kc now appears in the right-hand column of the
[Calibrate Flow Rate] menu cell with its new value. Also note that this Kc value can be
viewed on the site printout.
Calibration Tables 1 through 3
SITRANS F 1010 instruments offer a unique methodology by which a particular flow response
of an instrument may be linearized or optimized by tabulating the results of a series of
calibration exercises or collected batch data points. Basically, the flowmeter allows the user
to select any of a wide variety of system variables (flowrate, pressure, viscosity, etc.) as a
pointer into a table of calibration factors (up to 32). As the system variable is updated, the value
of the table’s output factors (or positive and negative flow) is re-evaluated and used as a
Appendix
A.5 Flowrate Calibration and Calibration Tables
FUP1010 IP67 Portable Flowmeter
146
Operating Instructions, 02/2010, A5E02951522A Revision 01
Summary of Contents for SITRANS FUP1010
Page 2: ......
Page 66: ......
Page 136: ......
Page 138: ......
Page 150: ......
Page 153: ...1010WP 7 21614 C ...
Page 154: ...1010WP 7 21614 C ...
Page 155: ...1010WDP 7 21614 C ...
Page 156: ...1010WDP 7 21614 C ...
Page 157: ...1010WP 8 21614 C ...
Page 158: ...1010WDP 8 21614 C ...
Page 159: ......
Page 161: ...1012FP 8 DIRECT MODE REFLECT MODE INSTALLED ON PIPE 21614 C ...
Page 162: ...1011PPS 8 TRANSDUCER PART NUMBER L H W NET WT PAIR X Z 21614 C SIZES A B C D SIZE E ...
Page 163: ...21614 C ...
Page 164: ......
Page 165: ......
Page 166: ......
Page 167: ......
Page 168: ...21614 C ...
Page 169: ...21614 C ...
Page 170: ...21614 C ...
Page 171: ...21614 C ...
Page 172: ...21614 C ...
Page 173: ...21614 C ...
Page 174: ...21614 C ...
Page 175: ...1015BC 1W 8 21614 C ...
Page 176: ......
Page 177: ...21614 C ...
Page 178: ...21614 C ...
Page 179: ...1012TP S 8 OUTLINE DIMENSIONS REFLECT MODE DIRECT MODE 1012TP S SERIES 21614 C MOUNTING TRACK ...
Page 180: ...REFLECT MODE DIRECT MODE 21614 C ...
Page 181: ...21614 C ...
Page 182: ...1015BC 1 8 21614 C ...
Page 183: ...21614 C INPUT OUTPUT TERMINALS 1015WP T10 8 ...
Page 184: ...21614 C INPUT OUTPUT TERMINALS 1015WP T26 8 ...
Page 185: ......
Page 186: ......
Page 187: ......
Page 188: ......
Page 190: ...DUAL HEAD CONFIGURATION 21614 C IN LINE CONFIGURATION FLOW ...
Page 191: ......
Page 192: ......
Page 194: ......
Page 204: ......
Page 206: ......
Page 207: ......