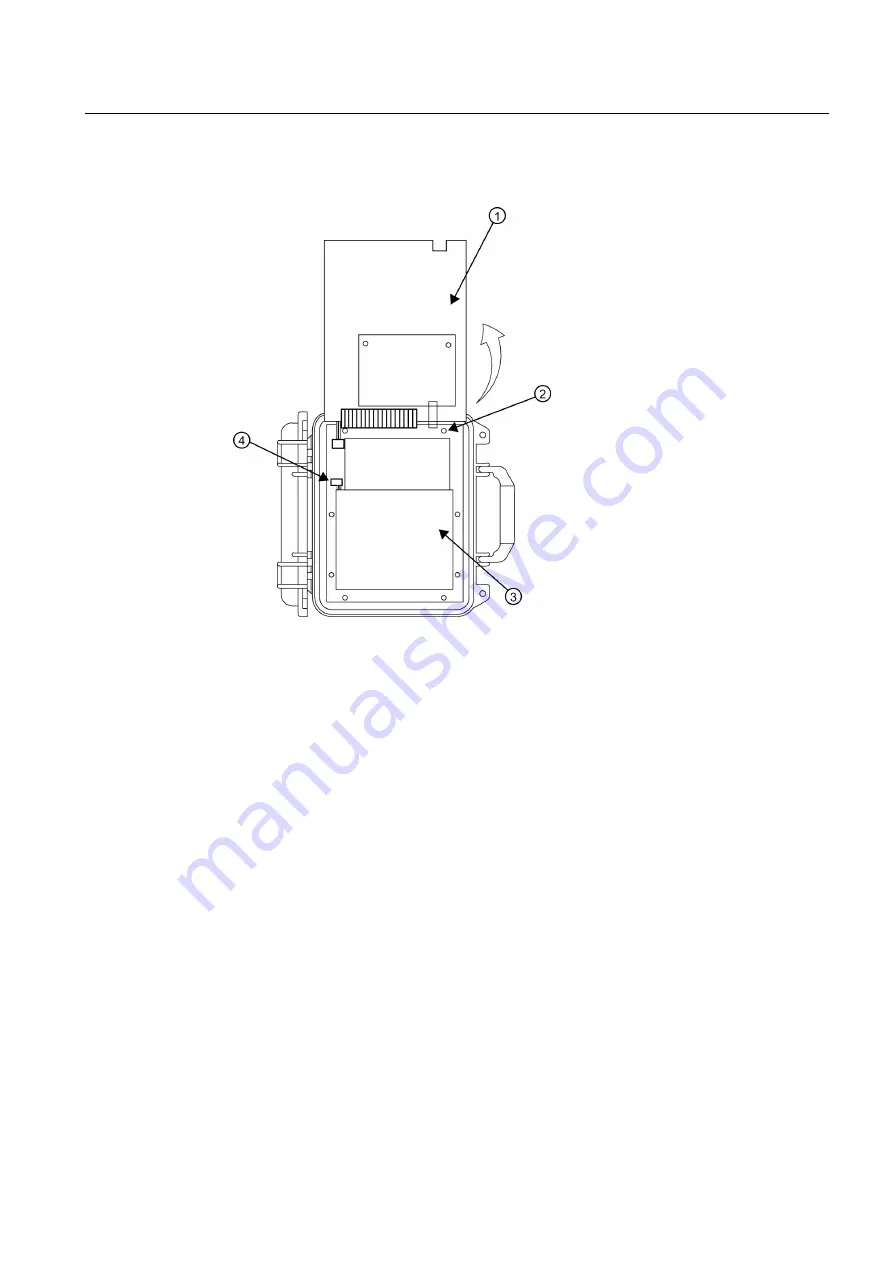
5. Pry up faceplate and gently lift upwards. Tilt faceplate back and rest it securely so that the
inside of the flowmeter is accessible but that there is no pressure on the wiring harnesses.
①
Faceplate tilted up and back
③
Battery Cover Plate
②
Battery Cover Screws (8)
④
Battery Connector P2
Figure 9-2
Battery Cover Removal
6. Remove 8 screws securing the battery cover. Set aside screws.
7. Disconnect pendant battery connector (J2). Note that it is a keyed-type plug.
Maintenance and service
9.2 Replacing the battery
FUP1010 IP67 Portable Flowmeter
Operating Instructions, 02/2010, A5E02951522A Revision 01
113
Summary of Contents for SITRANS FUP1010
Page 2: ......
Page 66: ......
Page 136: ......
Page 138: ......
Page 150: ......
Page 153: ...1010WP 7 21614 C ...
Page 154: ...1010WP 7 21614 C ...
Page 155: ...1010WDP 7 21614 C ...
Page 156: ...1010WDP 7 21614 C ...
Page 157: ...1010WP 8 21614 C ...
Page 158: ...1010WDP 8 21614 C ...
Page 159: ......
Page 161: ...1012FP 8 DIRECT MODE REFLECT MODE INSTALLED ON PIPE 21614 C ...
Page 162: ...1011PPS 8 TRANSDUCER PART NUMBER L H W NET WT PAIR X Z 21614 C SIZES A B C D SIZE E ...
Page 163: ...21614 C ...
Page 164: ......
Page 165: ......
Page 166: ......
Page 167: ......
Page 168: ...21614 C ...
Page 169: ...21614 C ...
Page 170: ...21614 C ...
Page 171: ...21614 C ...
Page 172: ...21614 C ...
Page 173: ...21614 C ...
Page 174: ...21614 C ...
Page 175: ...1015BC 1W 8 21614 C ...
Page 176: ......
Page 177: ...21614 C ...
Page 178: ...21614 C ...
Page 179: ...1012TP S 8 OUTLINE DIMENSIONS REFLECT MODE DIRECT MODE 1012TP S SERIES 21614 C MOUNTING TRACK ...
Page 180: ...REFLECT MODE DIRECT MODE 21614 C ...
Page 181: ...21614 C ...
Page 182: ...1015BC 1 8 21614 C ...
Page 183: ...21614 C INPUT OUTPUT TERMINALS 1015WP T10 8 ...
Page 184: ...21614 C INPUT OUTPUT TERMINALS 1015WP T26 8 ...
Page 185: ......
Page 186: ......
Page 187: ......
Page 188: ......
Page 190: ...DUAL HEAD CONFIGURATION 21614 C IN LINE CONFIGURATION FLOW ...
Page 191: ......
Page 192: ......
Page 194: ......
Page 204: ......
Page 206: ......
Page 207: ......