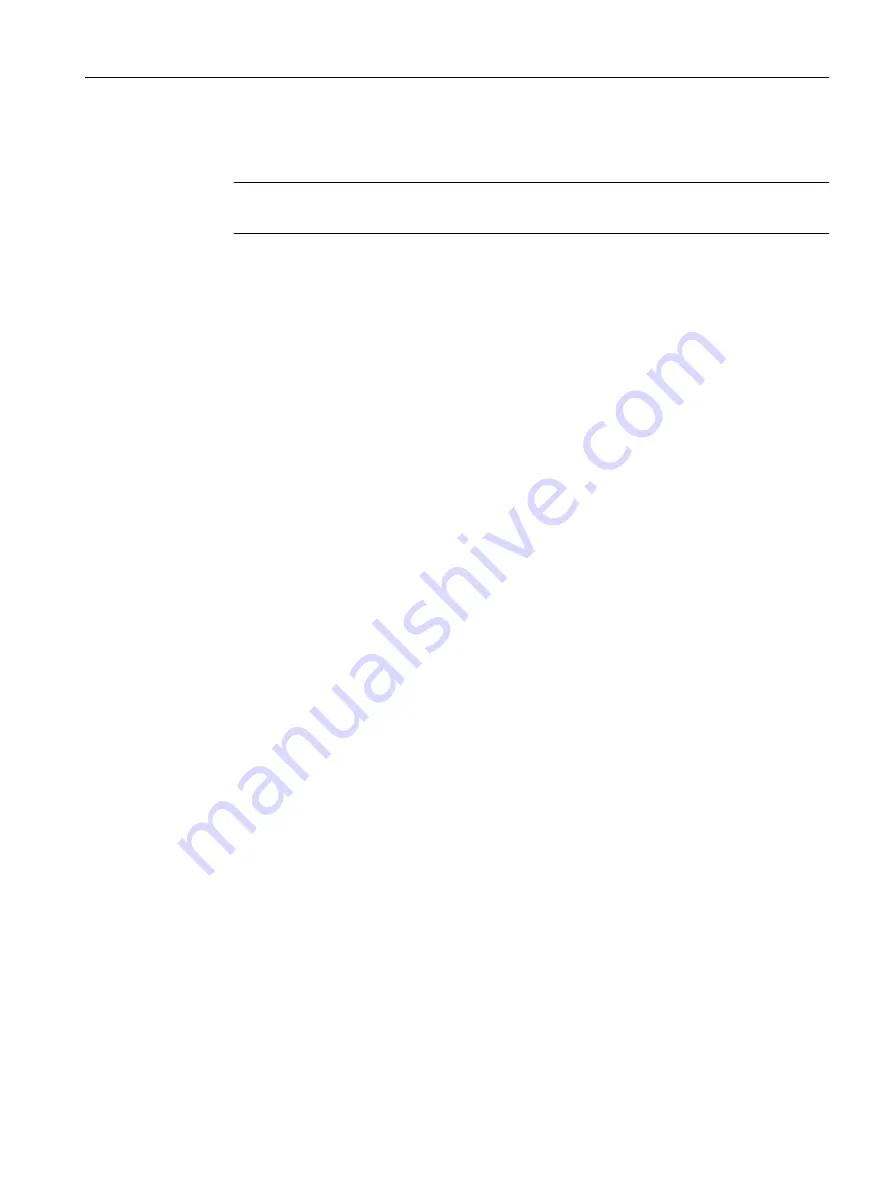
Entering the data
1. Enter the sensor diameter (Di) (menu 7.1.3.1).
Note
If Di is smaller than registered, the setting in step 9 (displacement) must be changed first.
2. Choose appropriate engineering unit for flow (menu 3.1.1).
3. Enter maximum flow (menu 3.1.2).
4. Choose "AUTO" for calibration choice (menu 7.1.1).
5. Enter viscosity for media (menu 7.1.3.1), otherwise the default value (0.01 cm
2
/s for water
20 °C) will be used.
6. Enter inside roughness of the sensor pipe (menu 7.1.3.2), otherwise the default value (0.4
mm) will be used.
7. Enter the measured transducer distance for each path (menus 7.1.4.x.1).
8. Enter the measured angle for each path (menus 7.1.4.x.2).
9. Enter the measured displacement for each path (menu 7.1.4.x.3). Enter 0 for paths not used.
10.Check the number of paths (menu 7.2). They are preset from factory according to order.
11.Go to service menu and check for each path that:
– control values for amplitude (menus 6.5.2.x) have a value within the interval 95 to 105.
– control values for error counters (menus 6.5.4.x) are 0.
– control values for TOF (menus 6.5.5.x) are stable an only vary in the nanosecond range
(for example ±10 ns).
12.Make sure that an absolute flowrate of zero is present and that the zero point adjustment
procedure is activated via menu 6.6.3 Zero calibr..
13.Calculation of flow can be corrected by use of the customer correction factor (menu 7.1.2.2)
which is a scaling factor.
Based on the entered data the transmitter is capable of measuring and calculating the actual
flow. The accuracy of the system at this stage is dependent on for example the entered accuracy
of the geometry data.
Service and maintenance
8.3 Keying in sensor data
SITRANS FUS060 with PROFIBUS PA
Operating Instructions, 09/2021, A5E02225054-AD
73