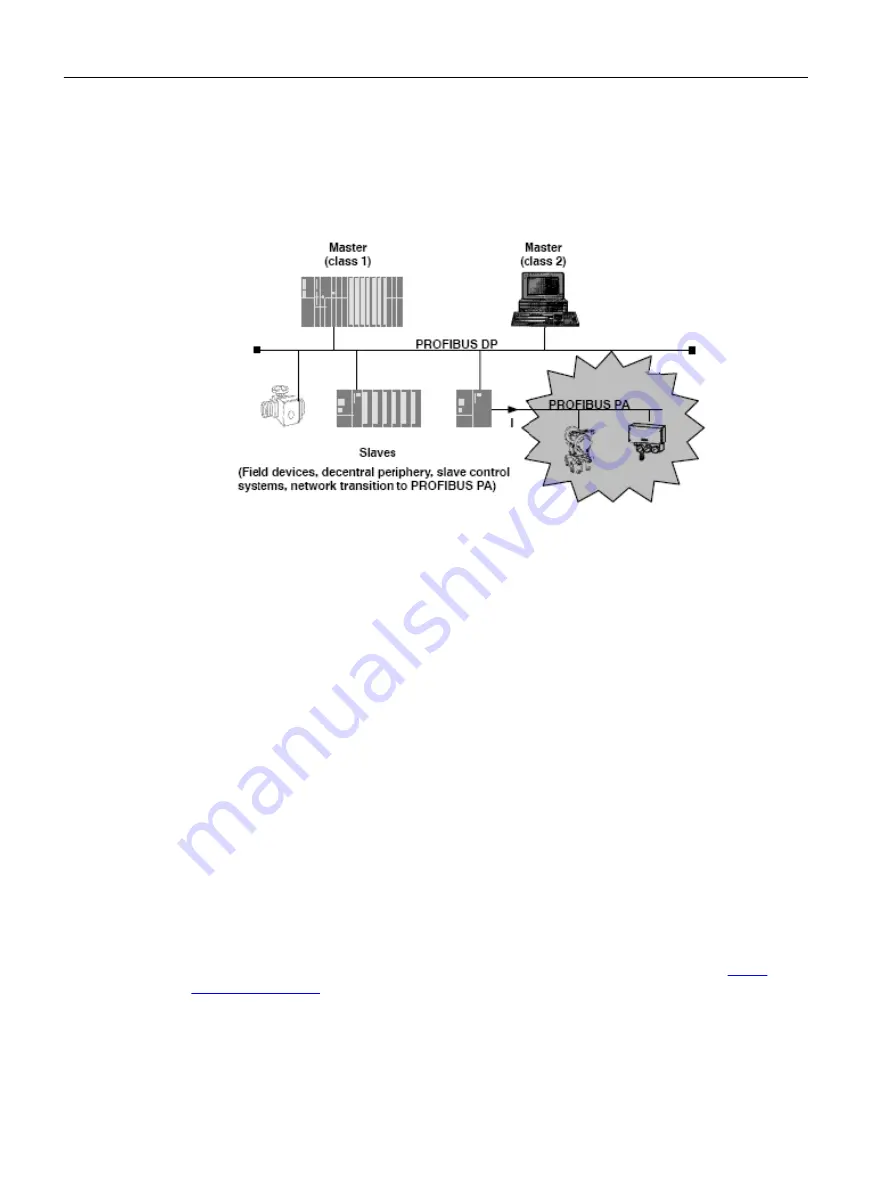
Use in the automation system
Several PROFIBUS PA lines are linked to the fast PROFIBUS DP in an automatic system. The process
control system is also linked to this. Both bus systems use a uniform protocol layer. Thus the
PROFIBUS PA is a communication-compatible extension of the PROFIBUS DP into the field.
Figure 3-4
Section of typical PROFIBUS automation system
Masters
The control system consists of two masters with shared tasks:
• Master class 1 takes care of the control and regulating tasks
Measuring and actuating data are exchanged cyclically between Master class 1 and the field
devices. The status information signals of the field devices are transmitted parallel to these
data and evaluated in the class 1 master. No field device parameters are set or other device
information read during cyclic operation. The information necessary for establishing
communication is available to the control system from the stored, device-specific device data
base files GSD.
• Master class 2 allows operating and monitoring functions.
One or more class 2 masters can access the field devices acyclically in addition to the cyclic
mode. With this communication type further information can be fetched from the devices or
settings made in the devices.
PROFIBUS PA Architecture
PROFIBUS PA enables bi-directional communication between a bus master and the field devices
over a two-wire cable. At the same time the power is supplied to the two-wire field devices
through the same cables.
Supplementary to the EN standard 50170, the PNO (PROFIBUS user organization (
)) has defined the scope of functions of the individual field device types in a
so-called profile description. These profiles define the minimum functional requirements and
optional extensions. A device-internal "Device Management" supplies all necessary basic
information for finding the profile parameters to the control system configuration tools. In this
Description
3.5 PROFIBUS communication
SITRANS FUS060 with PROFIBUS PA
22
Operating Instructions, 09/2021, A5E02225054-AD