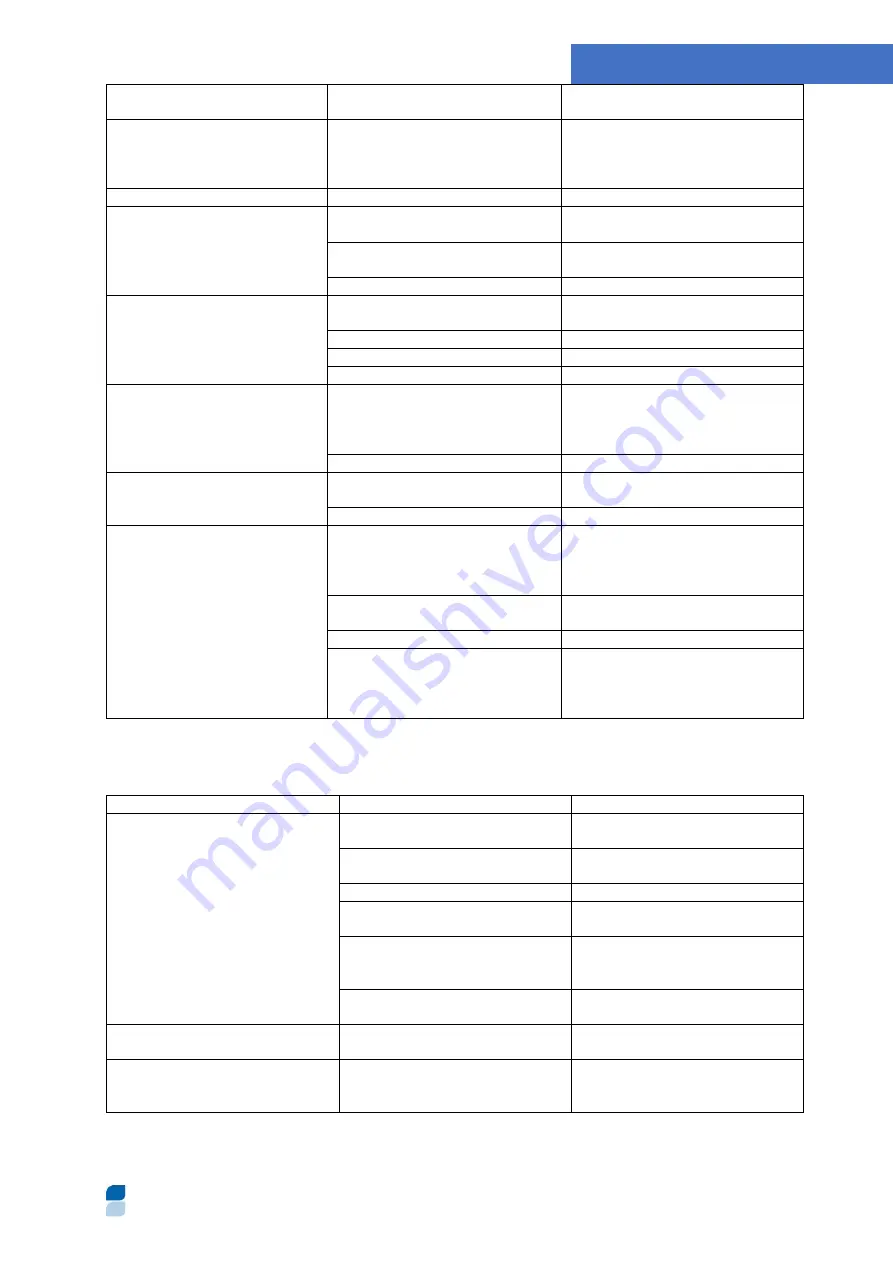
Page 84 of 106
TMS 5001
- Increase secondary air blow
lapse.
Perpendicularity
Misaligned neck after
embossing.
- Check primary air valve
operation.
- Check diameter of blowing mould
semiarid in the necks.
Uneven thickness
- Control preform quality.
External corrugation
Faulty preform conditioning
- Increase temperature in the
preset area.
Excessive delay in low pressure
blowing. It started too soon
- Reduce primary air blow delay
Too low primary air pressure
- Increase primary air pressure.
Internal corrugation
Bad conditioning shape
- Bring temperature down to
optimum point
Faulty heating of preform bottom - Reduce bottom temperature.
Excessive delay of secondary air - Change secondary air delay.
Too low primary air pressure
- Increase primary air pressure.
Stain formation (none or
partial)
Too low secondary air blowing
- Activate secondary air blow
earlier.
- Increase application lapse.
- Check electro valves.
Dirty bottom
- Clean air outlets.
Lenticulation
(too
much
material)
Primary air blow lapse too late
- Reduce the activation of primary
air delay.
Too low primary air pressure
- Increase primary air pressure.
Misalignment
(see also container
perpendicularity)
High pressure too soon
- Delay primary air (Shrink)
- Control the different parts of the
pneumatic facility of primary air.
- Check the stretching rod speed.
Too much distance between the
rod and the bottom
- Check distance between rod and
bottom (3mm)
Stretching unit off axis
-Adjust stretching unit
Uneven preform thickness
- Check lip temperature, if it is too
high, removal may deform the
upper part of the preform. The
stretching rod might be bent.
8.2.3
CONSISTENCY
DEFECTS
CAUSE
SOLUTIONS
Fracture by falling
Incorrectly bi-oriented bottom
Check preform injection point.
Misaligned point.
Incorrect heating of preform
bottom
Check preform and resin quality
(PET).
Too low primary air pressure
Increase primary air pressure.
Excessive
low-pressure
activation time
Reduce primary air blow.
Fragile preform on injection point -Check preform injection point.
-Check
cooling
water
temperature.
Low quality resin (PET)
Check preform and resin quality
(PET)
Explosion on opening the mould Decompression did not take
place
Check
operation
of
decompression electro valve.
Volume changes after some time Too low secondary air pressure
-
Increase
secondary
air
pressure.
-
Increase application lapse.
Summary of Contents for TMS 5001
Page 1: ...TMS 5001 INSTRUCTIONS MANUAL OPERATION MANUAL ...
Page 18: ...Page 17 of 106 TMS 5001 MACHINE ...
Page 19: ...Page 18 of 106 TMS 5001 TOOL FOR MOULD COLOCATION Block mould ...
Page 21: ...Page 20 of 106 TMS 5001 1 A B ...
Page 23: ...Page 22 of 106 TMS 5001 2 3 UP UP DOWN and LEVEL DOWN and CONTACT DOWN and CONTACT ...
Page 106: ...Page 105 of 106 TMS 5001 H 10 30 ...
Page 107: ...Page 106 of 106 TMS 5001 if A B then A B A B A B ...