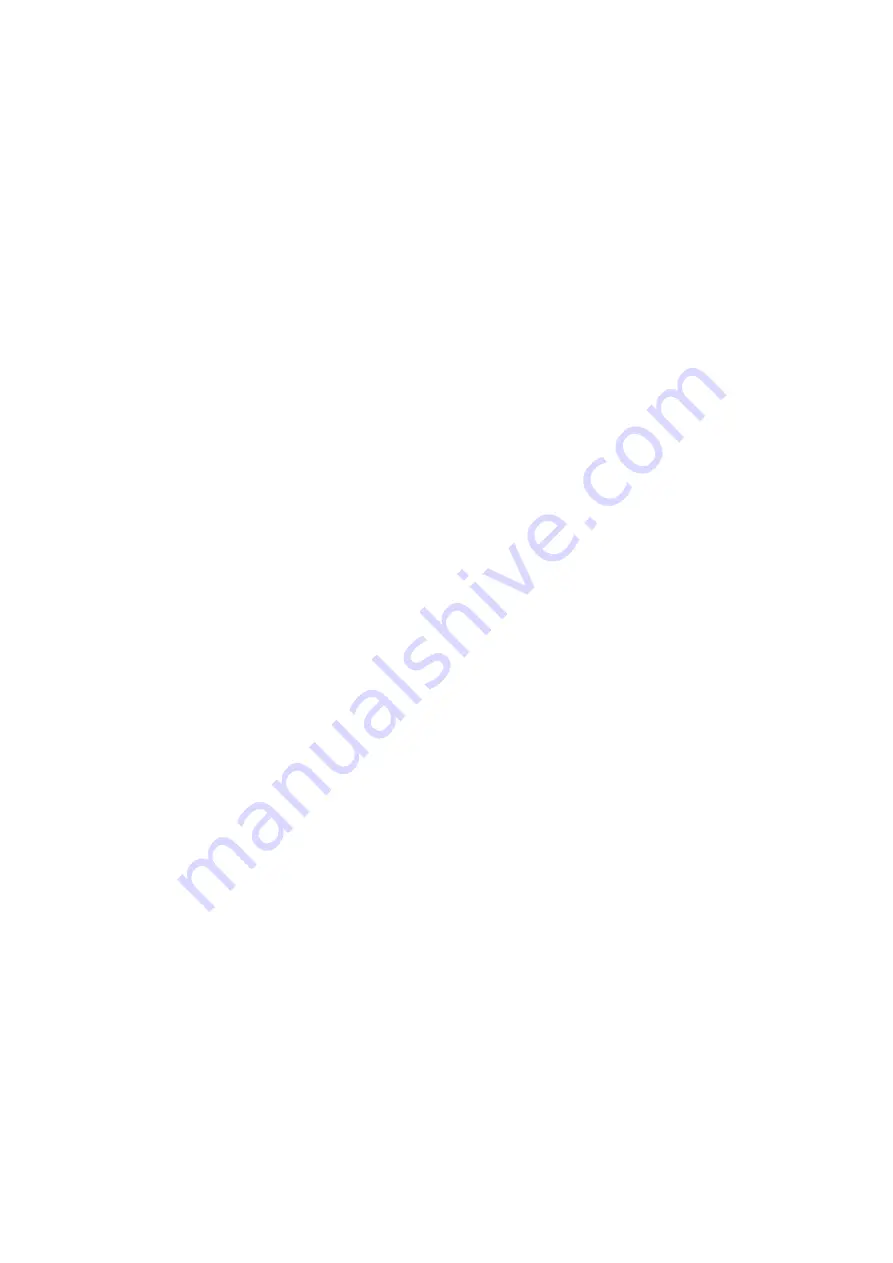
PREFORM CARRIER
5.9.
DELIVERY
5.10.
PRESS FEED CONVEYOR
5.11.
LOADING AND NAILING
5.12.
NOZZLE COOLING
5.13.
HOPPER AND FEEDER
5.14.
CONVEYOR BRAKE
6.
SCREEN
6.1.
EXTERNAL SWITCHES
6.2.
MANOEUVRES
6.3.
SCREENS
6.4.
ALARMS (MALFUNCTION – CAUSE – SOLUTION)
7.
FORMAT CHANGE
7.1.
PREVIOUS PROCEDURES
7.2.
FORMAT CHANGE START-UP
8.
BLOWING ADJUSTMENTS
8.1.
PARAMETERS OF THE HEAT FIXATION PROCESS
8.2.
LIST OF SHAPING DEFECTS AND SOLUTIONS
9.
MAINTENANCE
9.1.
CHECKING THE BLOWING MACHINE
9.2.
LUBRICATING THE BLOWING MACHINE
9.3.
MECHANIC LINING-UP
Summary of Contents for TMS 5001
Page 1: ...TMS 5001 INSTRUCTIONS MANUAL OPERATION MANUAL ...
Page 18: ...Page 17 of 106 TMS 5001 MACHINE ...
Page 19: ...Page 18 of 106 TMS 5001 TOOL FOR MOULD COLOCATION Block mould ...
Page 21: ...Page 20 of 106 TMS 5001 1 A B ...
Page 23: ...Page 22 of 106 TMS 5001 2 3 UP UP DOWN and LEVEL DOWN and CONTACT DOWN and CONTACT ...
Page 106: ...Page 105 of 106 TMS 5001 H 10 30 ...
Page 107: ...Page 106 of 106 TMS 5001 if A B then A B A B A B ...