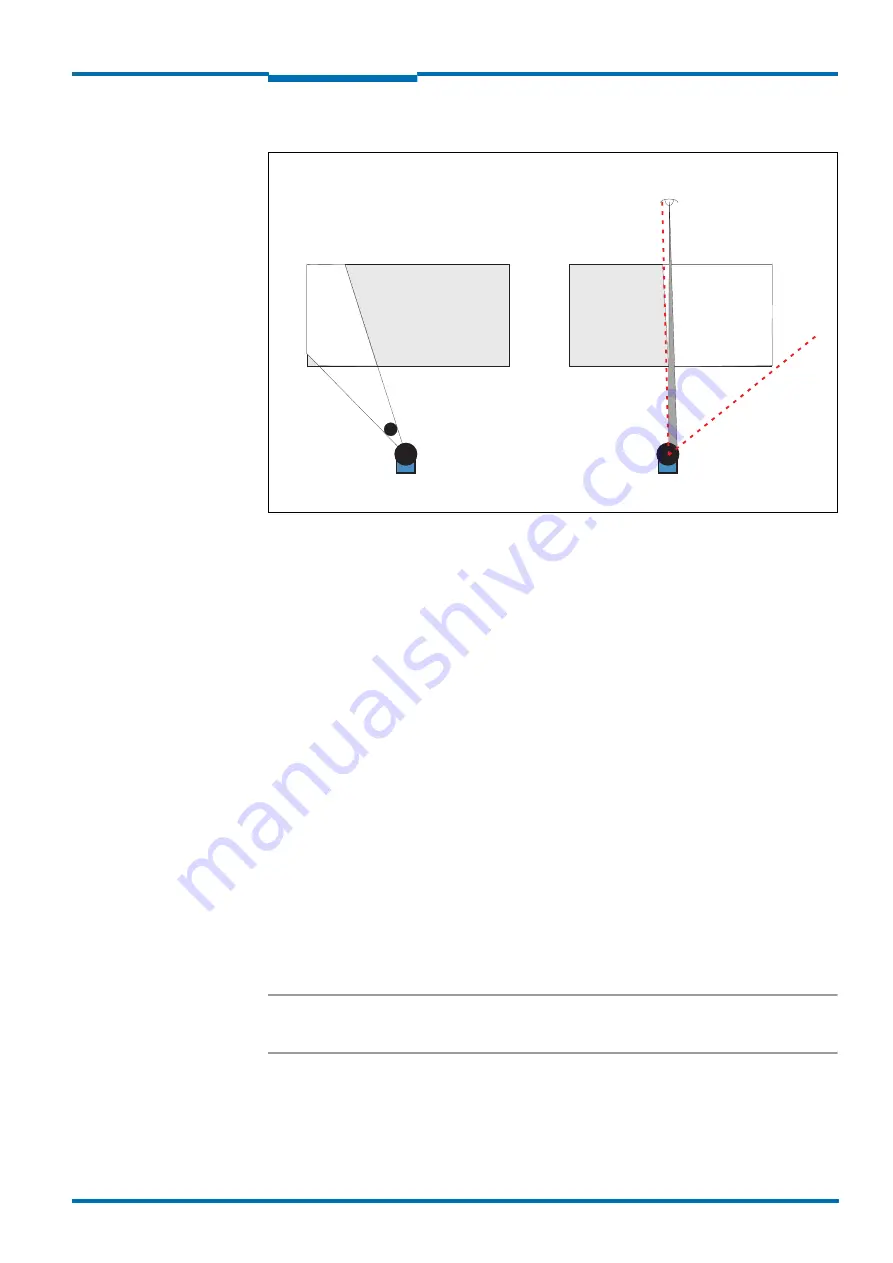
Operating Instructions
LMS1xx Laser Measurement Sensors
Product description
8012471/ZN27/2017-06-09
© SICK AG · Germany · All rights reserved · Subject to change without notice
43
Chapter
3
To prevent this situation arising, you can configure the O
BSTRUCTION
PROTECTION
option.
Fig. 26:
Protection against tampering due to shading and glare
The Obstruction protection option switches the evaluation field at the following events:
An object that is smaller than or equal to the blanked object size is in front of the laser
output aperture on the LMS1xx for the configured response time for Obstruction
protection.
The LMS1xx is dazzled for longer than the configured response time for Obstruction
protection.
Evaluation field
Choose one of the evaluation fields already configured for the evaluation case. Its shape
must match the evaluation strategy (see
section 3.9.2 “Evaluation fields” on page 44
). If,
for instance, you select the evaluation strategy C
ONTOUR
AS
REFERENCE
, then a contour field
must be configured so that the LMS1xx functions correctly.
Output
Choose one of the outputs for the evaluation case. If several evaluation cases act on an
output, you must define how the results of the evaluation cases are linked (see
section 3.9.3 “Operator for the evaluation cases on the output” on page 45
Negating the result
By negating the result the field evaluation is signalled in reverse on the output. The output
used is, e.g., then switched if the evaluation field is clear or if the contour is not infringed.
Important
Do not confuse the negation of the result with the setting active high/active low for the
outputs (see
section 3.9.3 “Operator for the evaluation cases on the output” on page 45
Object smaller than
blanking
Area hidden
by glare
Shading
Light source
Evaluation field at a distance from the
LMS1xx