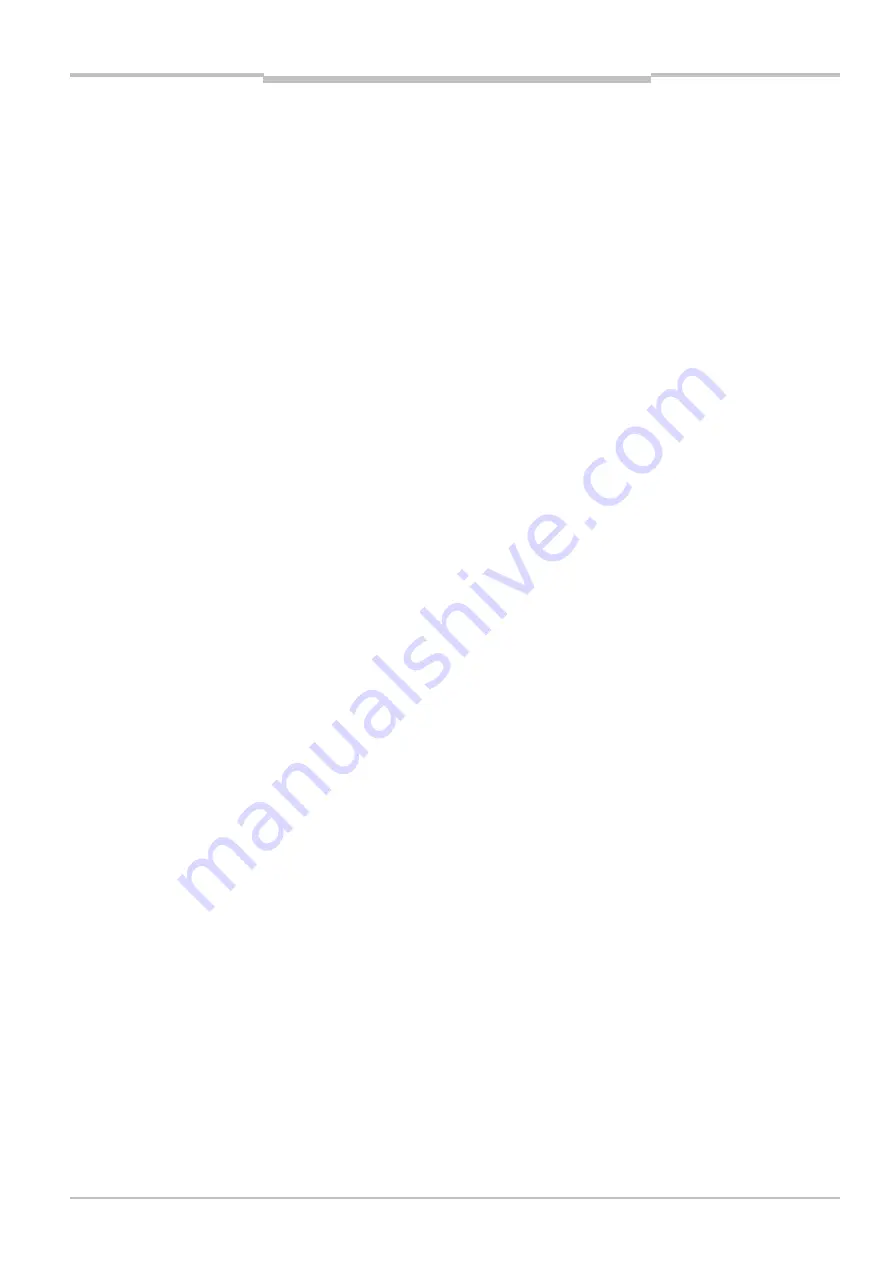
Operating Instructions
Chapter
11
TPS
8021799/2017-09-26
Operating Instructions | SICK
85
Subject to change without notice
Figures and tables
11.3
Keywords index
A
Abbreviations ...........................................7
Application areas .....................................8
B
Black Spot Warning .............................. 19
C
Cleaning
LD-MRS ............................................. 65
LMS151 ............................................ 65
Collision awareness .............................. 63
Commissioning ..................................... 41
Components ................................... 14–15
Control Cabinet ................................. 16
GPS receiver ..................................... 16
LD-MRS ...................................... 14–15
Mounting kit ...................................... 16
Operator display ............................... 15
Tone buzzer ....................................... 16
Configuration
LD-MRS ............................................. 45
LMS151 ............................................ 45
Supervisor setup ............................... 52
Vehicle setup .................................... 44
Configuration mode
Enabling ............................................ 70
Functions .......................................... 43
Connecting the control cabinet ............ 38
Connecting the pause signal ............... 39
Connecting the RDW lights .................. 40
Connecting the reverse signal ............. 39
Connection
Control cabinet ................................. 38
GPS receiver ..................................... 37
LD-MRS ............................................. 30
LMS151 ............................................ 32
Operator display ............................... 34
Pause signal ...................................... 39
RDW lights ......................................... 40
Reverse signal .................................. 39
Tone buzzer ....................................... 37
Contamination control .......................... 75
Control cabinet
Mounting ........................................... 26
Control Cabinet ..................................... 16
D
Day/night mode switching ................... 62
Dimensional drawings .......................... 79
DIP switch ............................................. 21
Disposal ................................................ 13
E
Electrical installation ............................ 28
Environment ......................................... 13
F
Fault diagnosis ..................................... 73
Fault situations
Commissioning ................................. 74
Front Collision Warning ........................ 17
Functionality ......................................... 17
Black Spot Warning .......................... 19
Front Collision Warning .................... 17
Rear End Collision Warning.............. 17
Road Departure Warning ................. 18
G
GPS receiver ......................................... 16
Connecting ........................................ 37
Mounting ........................................... 27
I
Information depth .................................... 6
Intended use ............................................ 9
K
Keywords index..................................... 86
L
LD-MRS ................................................. 14
Cleaning ............................................ 65
Configuring ........................................ 45
Connecting ........................................ 30
Mounting Front ................................. 24
Mounting Rear .................................. 24
Replacing .......................................... 67
LiDAR sensor ................................. 14–15
List of figures ........................................ 84