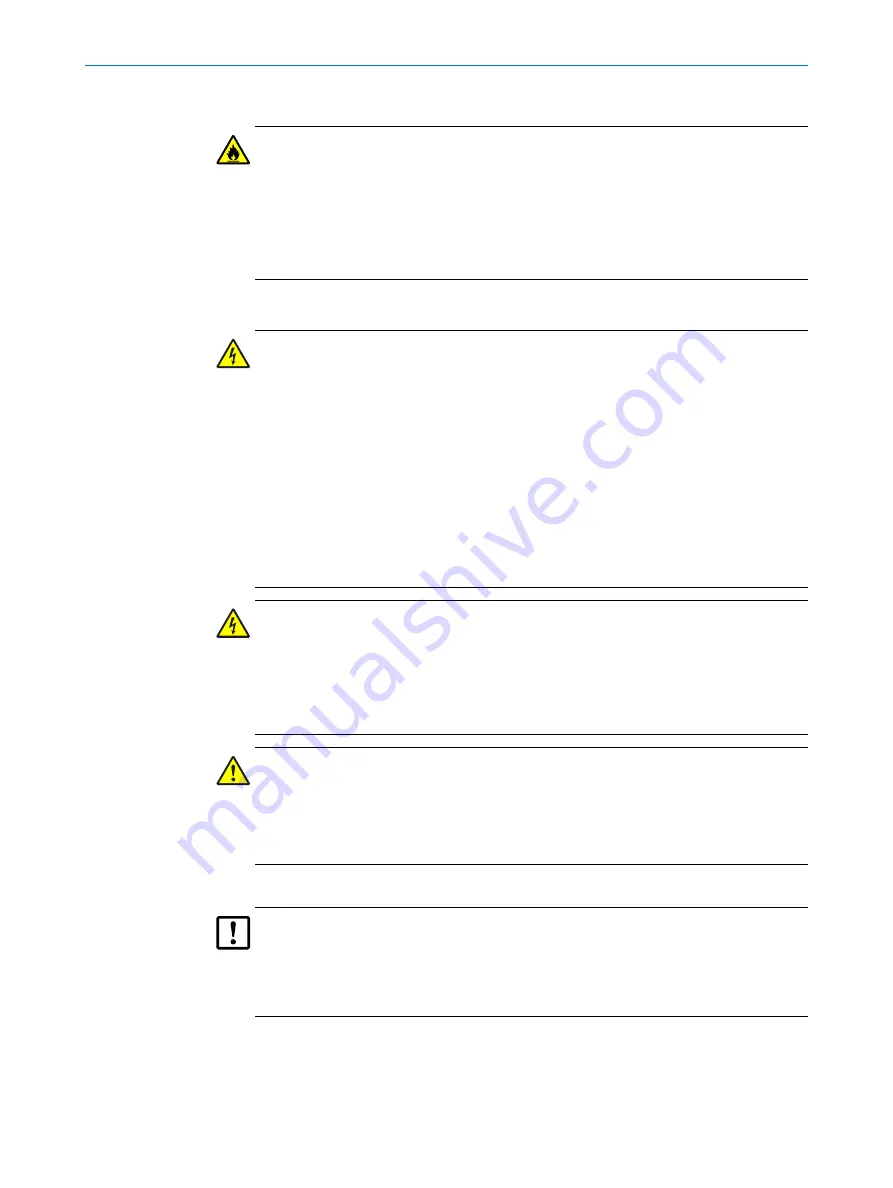
Hot gases in ambient conditions with overpressure
DANGER
Risk of fire through hot gas escaping in installations with overpressure conditions
On installations with overpressure, the purge air hose can be severely damaged by
escaping hot gas and can catch fire depending on the temperature. On installations
with overpressure as well as gas temperatures over 200°C:
b
Ensure reverse flow is prevented by fitting a (trip) flap or a valve.
b
Regularly check the functionality of the reverse flow safeguard.
Electrical safety
WARNING
Endangerment of electrical safety during installation and maintenance work when the
power supply is not switched off
b
Before starting the work on the device, ensure the power supply can be switched
off using a power isolating switch/circuit breaker in accordance with DIN EN
61010.
b
Make sure the power isolating switch is easily accessible.
b
An additional disconnecting device is mandatory when the power isolating switch
cannot be accessed or only with difficulty after installation of the device connec‐
tion.
b
The power supply may only be activated again after the end of the work or for test
purposes by personnel carrying out the work under consideration of valid safety
regulations.
WARNING
Endangerment of electrical safety through power cable with incorrect rating
When a removable power cable is used, electrical accidents can occur when the specifi‐
cations are not fully observed.
b
Always observe the exact specifications in the Operating Instructions (Technical
Data Section) when replacing a removable power cable.
DANGER
Danger of electrical accidents
Incorrect performance of electrical work could result in serious electrical accidents.
b
The following tasks must be performed by skilled electricians who are aware of
potential hazards.
Grounding
CAUTION
Device damage through incorrect or missing grounding
During installation and maintenance work, it must be ensured that the protective
grounding to the devices and/or lines involved is effective in accordance with EN
61010-1.
7
COMMISSIONING
50
O P E R A T I N G I N S T R U C T I O N S | GM32-Ex
8015558/YYJ8/V1.7/2016-07 | SICK
Subject to change without notice