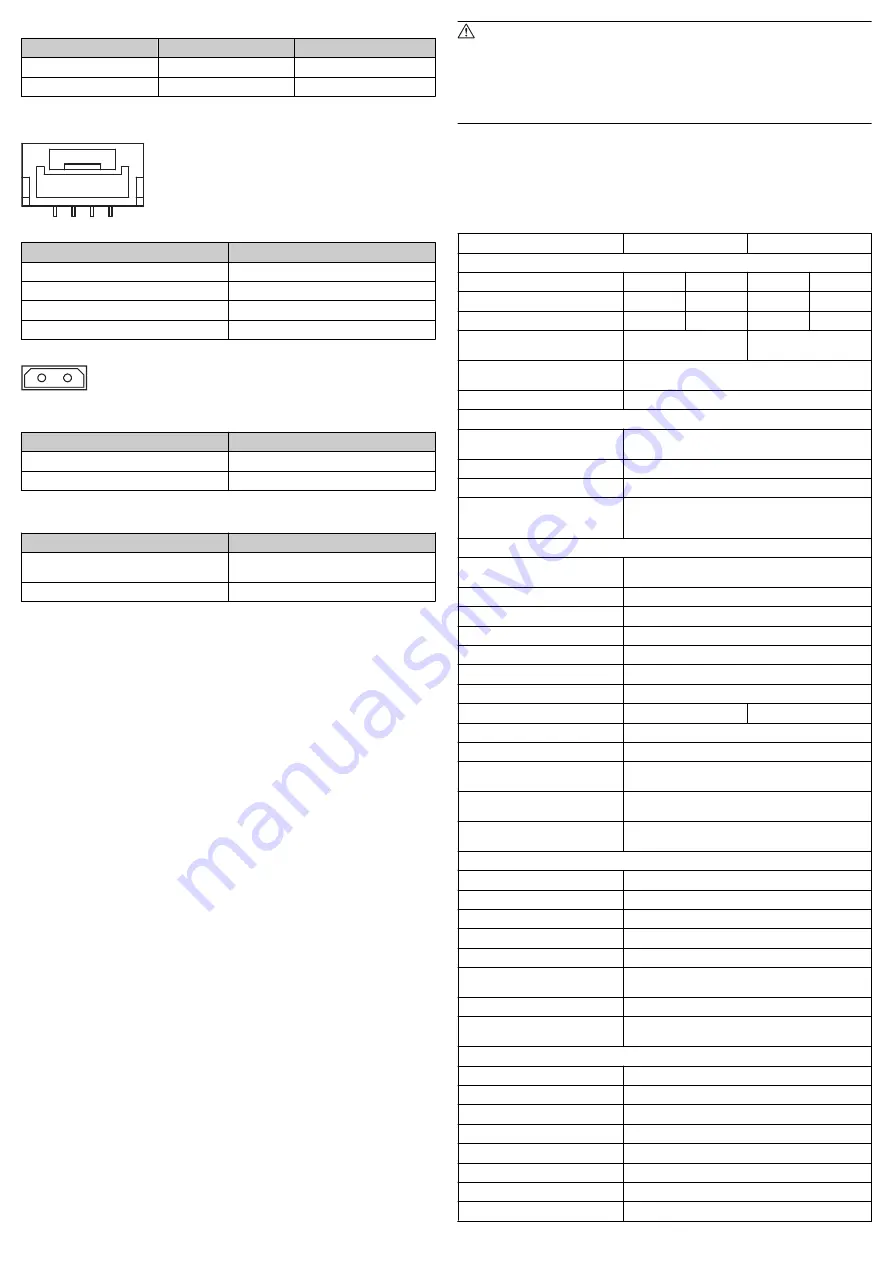
5.2 Connecting interfaces
Type
Male connector
Female connector
DSL
6
10
Temperature
9
5
Table 1: Male/female connector position
5.2.1
DSL female connector
1
2
3
4
Figure 3: JST BM04B-GHS-GB-TBT (gold-plated) - Device pin assignment
Pin
Signal
1
not assigned (spare)
2
US+ / DSL+
3
GND / DSL-
4
not assigned (spare)
5.2.2
Temperature sensor male connector
2 1
Figure 4: Harwin M80-8820242 - Device pin assignment
Pin
Signal
1
T+
2
T- / GND
5.2.3
Recommended components
Cable connector
Connector
Type
DSL
JST GHR-04V-S (Housing) SSHL-002GA1-
P0.2 (Contact, gold-plated)
Temperature
Harwin M80-xxx-02-XX
Table 2: recommended connector
5.3 Electrical Installation procedure
1.
If necessary, carefully remove the cover (7) from the encoder (12). If neces‐
sary, undo the Torx T08 screw (8) using a screwdriver.
2.
Insert the male connector for the set of DSL stranded wires (6) into the DSL
female connector (10) on the encoder far enough that it clicks into place,
but without mechanical stress.
3.
Optional: Insert the female connector for the temperature sensor (5) into the
temperature sensor male connector (9) without mechanical stress.
4.
Mount the cover (7) and tighten the Torx T08 screw (8). Tightening torque:
0.5 ± 0.05 Nm.
5.
Optional: Attach the shield wire of the set of DSL stranded wires to the
shielding connection (13) using a self-tapping M2.5x5 screw.
5.4 Motor feedback system signals
The motor feedback system has the following signals:
HIPERFACE DSL
®
interface:
•
US+ / DSL+: Supply voltage for the encoder with superimposed positive data
signal. The supply voltage range of the encoder is b7 VDC and
+12 VDC.
•
GND / DSL–: Ground connection of the encoder with superimposed negative
data signal.
•
T+: Sensor signal for passive temperature sensor/temperature resistor.
•
T- / GND: Reference ground for sensor signal of passive temperature sensor/
temperature resistor.
6
Commissioning
To commission the safe motor feedback system, it is assumed that the manufac‐
turer of the connected drive system has complied with the safety requirements for
the drive system design, as described in the “HIPERFACE DSL
®
MASTER” technical
information.
6.1 Checking
During commissioning ensure that an EDS35-2 / EDM35-2 safe motor feedback
system is used and not an EDS35-0 / EDM35-0 standard motor feedback system.
In addition, the POST bit (Power-On-Self-Test) must be set for an EDS35-2 /
EDM35-2 safe motor feedback system after an encoder RESET (hardware or soft‐
ware RESET). The POST bit can be acknowledged after a positive thorough check
(see “HIPERFACE DSL
®
MASTER” technical information).
If the position offset of the motor feedback system is changed using the 101h
(“Set position”) resource or the 108h (“Factory settings”) resource, it is then nec‐
essary to verify that the sensor is providing the required position value.
Further inspection measures are not required during operation.
WARNING
Observe the service life!
The EDS35-2/EDM35-2 safe motor feedback systems have a maximum ser‐
vice life, after which they must always be put out of service. The bearing ser‐
vice life must be taken into account in addition to the mission time. The para‐
meter which is first reached depending on the application determines the
time when the system must be taken out of operation.
The year of manufacture of the motor feedback system is specified on the device
label and/or on the packaging label as a four digit code (yyww). The first two digits
(yy) represent the year (without the century), and the last two digits (ww) repre‐
sent the calendar week of the last manufacturing process.
7
Technical data
Technical specifications
Singleturn
Multiturn
Performance
Resolution per revolution
20 Bit
24 Bit
20 Bit
24 Bit
Position noise (σ)
1
± 3“
± 1“
± 3“
± 1“
System accuracy
2
± 50“
± 25“
± 50“
± 25“
Number of the absolute ascertain‐
able revolutions
1
4,096
Speed when switching on and reset‐
ting the motor feedback system
3
≤ 6,000 min
-1
Available memory area
8,192 bytes
Interface
Code sequence
Increasing on rotation of shaft. Clockwise while looking
towards "A" (see dimensional drawing).
2
HIPERFACE DSL
®
interface signals
4
2-wire H-DSL: Digital, RS485 combined with Power
Initialization time
5
Max. 500 ms
Measurement of external tempera‐
ture resistance
6
Output format: 32 bit value without sign; Output unit:
1 Ω; Measuring range: 0 ... 209,600 Ω Additional recal‐
culation function from PT1000 to KTY84-130
Electrical data
Operating voltage range/supply
voltage
7 V … 12 V
Switch on timing voltage ramp
7
Max. 180 ms
Power consumption
8
Max 1.0 W (Vs = 7 V … 12 V)
Mechanical data
Dimensions
See dimensional drawing
Mass
Max. 100g
Rotor moment of inertia
5 gcm²
Operating speed
Max. 12,000 min
–1
Max. 9,000 min
–1
Max. angular acceleration
250,000 rad/s²
Start-up torque at 20°C
≤ 0.4 Ncm
Permissible shaft movement axial
( dynamic)
± 1 mm
Permissible shaft movement radial
(dynamic
± 0.025 mm
Service life of ball bearings
50,000 h at 6,000 rpm (at defined measuring point of
70 °C)
Ambient conditions
Operating temperature range
9
–40 … +115 °C
Storage temperature range
–40 … +125 °C (without packaging)
Operating altitude
≤ 2,000 m above sea level. (80 kPa)
Relative air humidity/condensation 90 % (condensation impermissible)
Resistance to shocks
1,000 m/s
2
/6 ms (as per EN 60068-2-27:2009)
Resistance to vibrations
500 m/s
2
/10 … 2,000 Hz (as per
EN 60068-2-6:2008)
Protection class
10
IP40 as per IEC 60529:2014
EMC
11
As per EN 61000-6-2:2016, EN 61000-6-4:2006,
IEC 6100-6-7:2014
Safety characteristics
Safety integrity level
12
,
13
SIL2 (IEC 61508:2011), SILCL3 (EN 62061:2010)
Systematic capability
13
SC3 (IEC 61508:2011)
Category
3 (EN ISO 13849-1:2015)
Test rate
24 h
Maximum demand rate
14
216 µs
Performance level
PL d (EN ISO 13849-1:2015)
Safety related resolution
13 bits
Safety related information
Safe Absolute Singleturn Position
8022479 /14FB/2019-06-19/de, en, es, fr, it
EDS35-2.../EDM35-2... | SICK
7