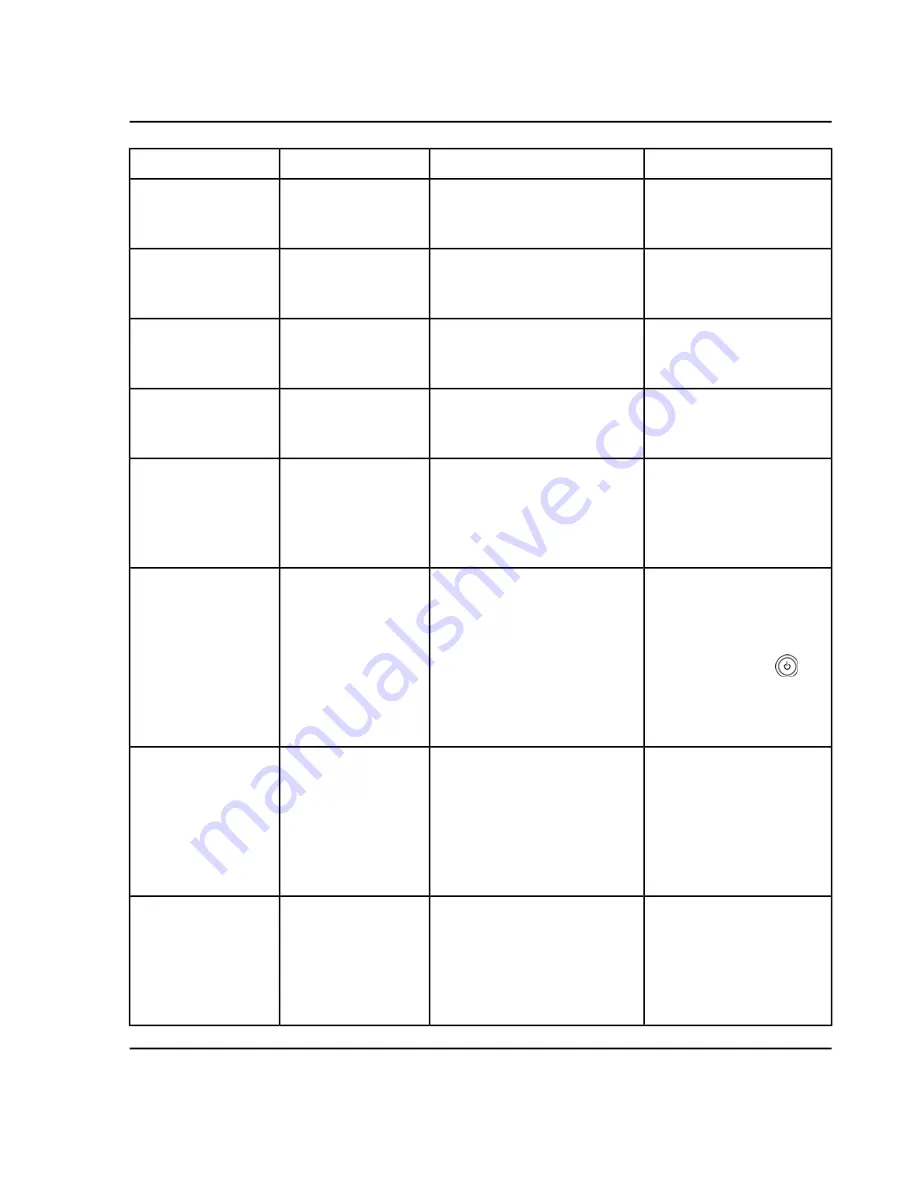
Recommended Action
Type / Cause
Error Message
Error Code
Replace the mobile phase
and then set the mobile
phase volume again.
Warning
The remaining amount
of Mobile Phase B
liquid is low.
0x9113
Replace the mobile phase
and then set the mobile
phase volume again.
Warning
The remaining amount
of Mobile Phase C
liquid is low.
0x9114
Replace the mobile phase
and then set the mobile
phase volume again.
Warning
The remaining amount
of Mobile Phase D
liquid is low.
0x9115
Replace the mobile phase
and then set the mobile
phase volume again.
Error 2
The pressure increased
during purge of the
pump.
0x9116
Press the
Power OFF
button in the error window
to turn the power to the
system off, and then contact
the FSE.
Fatal error
Pump is stopped
because a rotation
error was detected in
the cooling fan for the
pump.
0x9117
Inspect the analysis condition
for mistakes or
inconsistencies.
If no mistake or inconsistency
is found, then press
(Power button) to turn the
power off, and then contact
the FSE.
Error 1
There is a mistake in
the analysis
parameters or settings.
0x9200
Inspect the low-pressure
valve, measuring pump, or
unit positioned above the
low- pressure valve for liquid
leakage, and then wipe off
the liquid around the leak
sensor.
Error 2. Liquid leaks from the
low-pressure valve, measuring
pump, or a unit (such as a
high-pressure valve, column oven,
or detector) positioned above the
low-pressure valve.
The leak sensor of the
autosampler low
pressure valve has
detected a liquid leak.
0x9201
Inspect the high-pressure
valve or unit positioned
above the high-pressure
valve for liquid leakage, and
then wipe off the liquid
around the leak sensor.
Error 2. Liquid leaks from the
high-pressure valve or a unit
(such as a detector) positioned
above the high-pressure valve.
The leak sensor of the
autosampler high
pressure valve has
detected a liquid leak.
0x9202
Hardware User Guide
ExionLC
™
100 System
RUO-IDV-05-1839-C
202 / 219
Error Messages