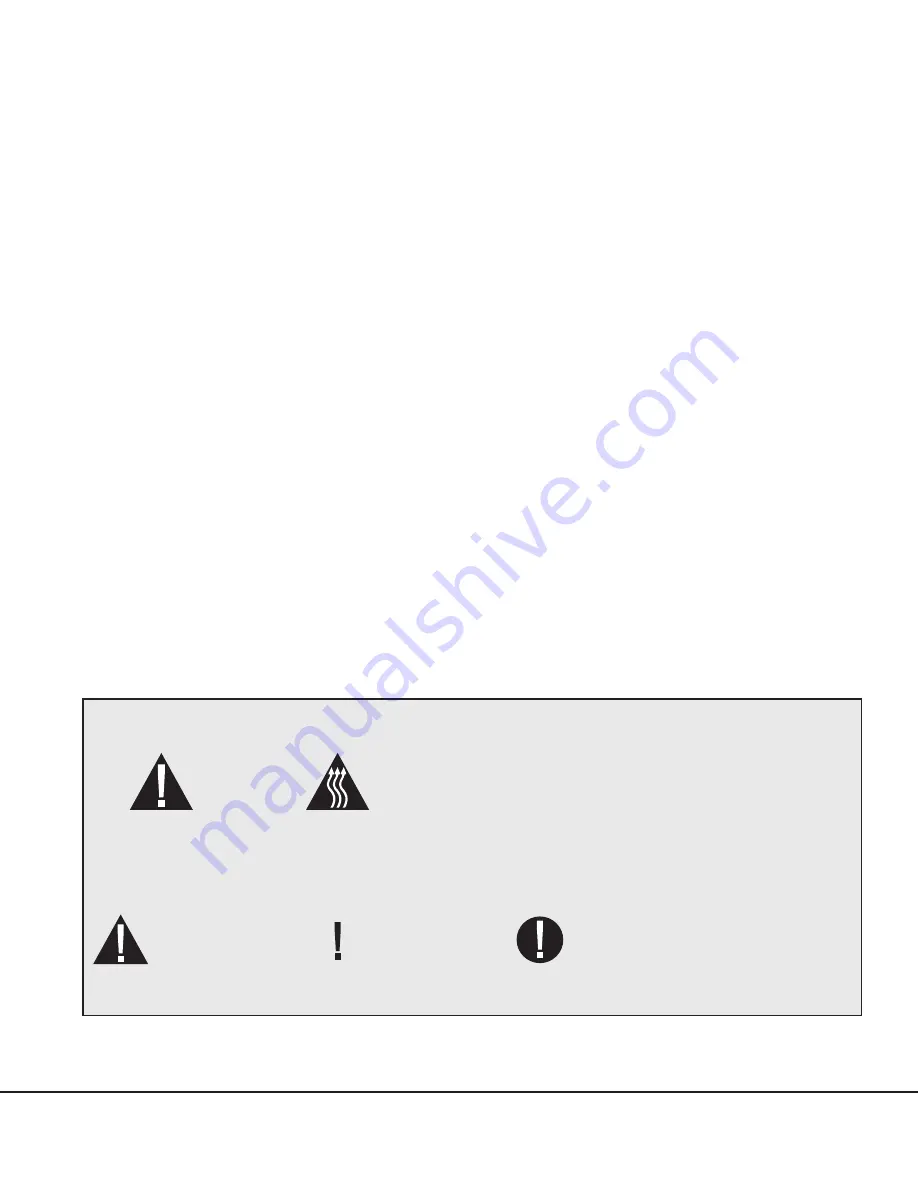
Height: 475
mm
Width:
600 mm
Depth:
460 mm
Depth with door open:
780 mm
Weight:
35 kg
Running Noise:
60 dB(A)
Hot water connection:
50-70˚C
Water softener:
0.5 kg salt capacity
Filling system:
3.5 L safety maximum
Dryer Heater
1kW
Wash temperature:
50˚C + / - 5˚C
Electrical Rating:
220 - 240V
50 Hz
10 A
Equipment pollution degree:
Pollution Degree 2
Equipment
Installation Category:
Installation Category II
Maximum relative humidity:
80% for temperatures up to 31˚C
50% for temperatures up to 40˚C
Operating temperature range:
- 5˚C to 40˚C
Maximum altitude:
2000 m
Mains supply:
+ / - 10% of nominal
Page 3
HYDR
IM
C51wd Service Guide
1. Introduction
1.2 Specifications
Pay close attention to the following symbols that appear in this book.
Caution, a potential
hazard to the operator
A situation which may lead
to a mechanical failure
Important information
Pay close attention to the following symbols that appear on the unit:
Caution,
hot surface
Caution, a potential
hazard to the operator