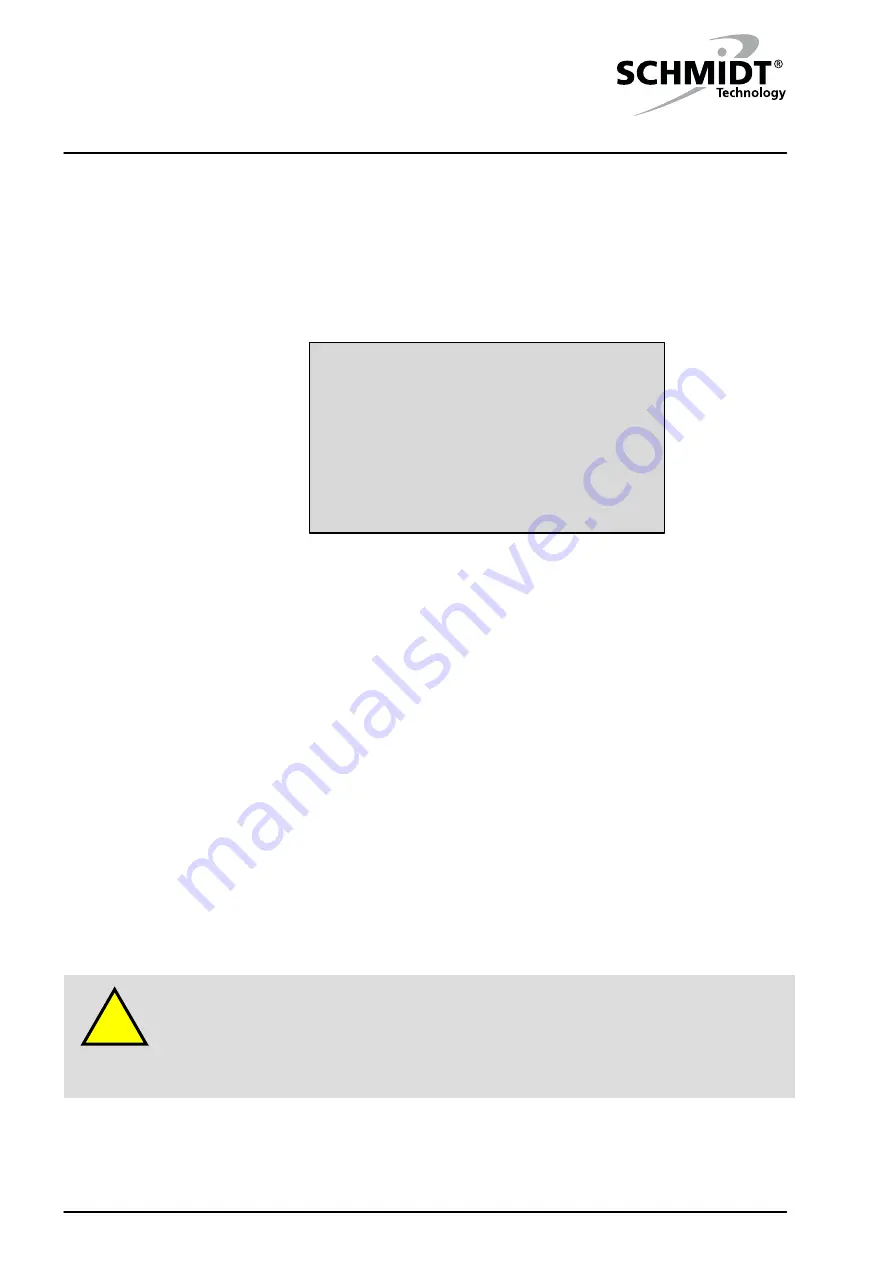
5 Data Input
SCHMIDT
®
PressControl 3000 – V1.3
18
5 Data Input
Various parameters (data input, system options, etc.) can be input directly at
the control unit.
Select the "Data Input" system function key.
1
CtrON
CtrOFF
...
...
Servic
3.0 sec
3.0 sec
20
1
5.000 mm
2.0 sec
30.000 mm
20.000 mm
1500 N
1
9 BDC-stroketakeover
8 Alarmtime press error
7 Alarmtime quan. reached
6 Target count
5 Counter access
4 Start/Stop PDA
3 Returnstroke Time
2 Returnstroke Stroke
1 Returnstroke Force
0 Mode : F=0,s=1,t=2,m=3
Input Dataset 1
Figure 5-1: Data input
Mark the desired parameter. The selected line is given a dark
background.
Press the "Enter” key. The previously set value is deleted and the
cursor blinks at the input position.
Enter the desired value using the numeric keys. Input errors can be
corrected by means of the "Left" cursor key.
Confirm the entry by pressing the “Enter” key.
10 input parameters can be displayed simultaneously on the display of the
control unit. You can move from one parameter to the next by using the “Up”
/ “Down” cursor keys. With the "Left" and "Right" cursor keys, you can jump
from on block of 10 to the next.
5.1 Default
settings
Contrast
The display is blank
With increasing operating temperature, the contrast of the display
diminishes. Since nothing can be seen any longer on the display, the user
may think that the control is defective.
Check if the contrast is set correctly using the "Contrast setting" key.
Calling data input
Scrolling
CAUTION
!