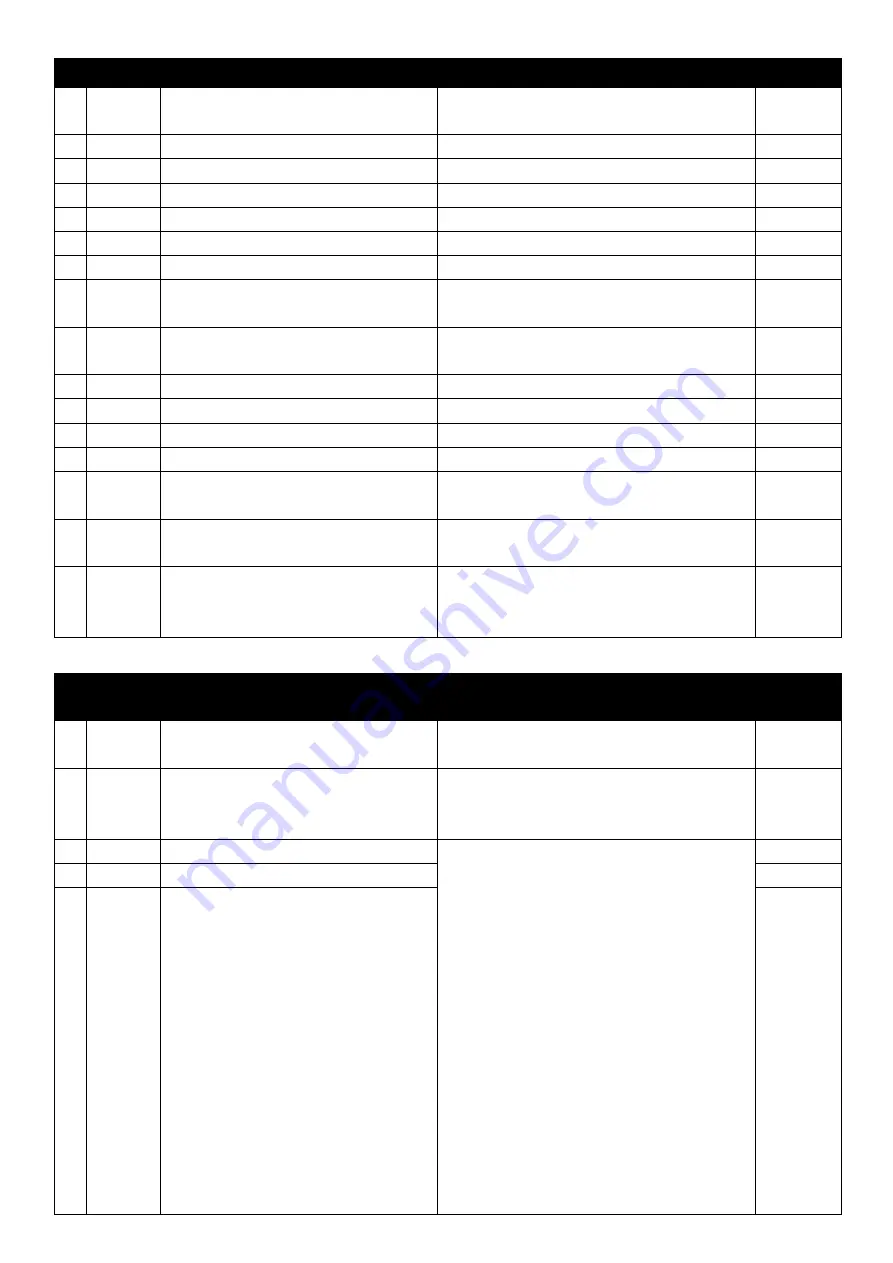
22
01:Basic Parameters
Set during running available * the values of different machine models are different.
Parame
ter
Parameter functions
Setting range
Factory
setting
01-03
Max voltage frequency setting
10.00
~
600.00 Hz
50.00
01-04
Max output voltage setting
200.0
~
500.0*V
380.0*
01-05
Intermediate frequency setting
1.00
~
600.00Hz
1.50
01-06
Intermediate voltage setting
2.0
~
500.0*V
12.0*
01-07
Min output frequency setting
0.00
~
20.00Hz
1.50
01-08
Min output voltage setting
2.0
~
100.0*V
12.0*
01-09
Upper limitation of output frequency
setting
1.00
~
600.00 Hz
600.00
01-10
Lower limitation of output frequency
setting
0.00
~
600.00 Hz
0.00
01-11
1
st
acceleration time setting
0.10
~
400.00 Sec
10.00
01-12
1
st
deceleration time setting
0.10
~
400.00 Sec
10.00
01-13
2
nd
acceleration time setting
0.10
~
400.00 Sec
10.00
01-14
2
nd
deceleration time setting
0.10
~
400.00 Sec
10.00
01-15
Motor Stop mode selection
0:Deceleration and stop
1:Coast to a stop
0
01-16
Inhibit REV rotation function setting
0:REV rotation available
1:REV rotation inhibited
0
01-17
Carrier frequency selection
0:fc=3kHz 1:fc=6 kHz
2:fc=8 kHz 3:fc=10 kHz
4:fc=12 kHz 5:fc=15 kHz
2
02:External Terminal Parameters
Set during running available * the values of different machine models are different.
Parame
ter
Parameter functions
Setting range
Factory
setting
02-00
2 wire style/3 wire operation control
0:Fwd run/stop, Rev run/stop
1:Run/stop, Rev run/fwd run
2:Three wire operation control
0
02-01
Multi-functional input option 1
0:Multi-step speed command 1
1:Multi-step speed command e 2
2:Multi-step speed command 3(EF)
3:Jog frequency command
4:Acceleration/Deceleration inhibition
command
5:Switching of 1
ST
and 2
nd
acceleration/deceleration time
6:reserved
7:reserved
8:Up command
9:Down command
10:RST input
11:EF input
12:Set frequency in the keypad while select
the specified ACI frequency.
3
02-02
Multi-functional input option 2
1
02-03
Multi-functional input option 3
2